Silicone molding has evolved into a vital manufacturing method for industries that demand durable, flexible, and biocompatible products. Whether it’s developing cutting-edge medical devices, robust automotive components, or high-performance electrical components, the choice of material directly impacts the product’s success.
And the choice might be more effort than first thought. Silicone molding is actually a term used to describe several forms of silicone and methods of processing them, with the two main ones being Liquid Silicone Rubber (LSR) and Solid Silicone Rubber (SSR). And knowing the key differences between both is crucial in today’s competitive environment. Their distinctive characteristics determine which material becomes the ideal choice for various industrial applications.
In this post, we’ll guide you through the wide range of applications, manufacturing processes, and physical properties of LSR and SSR, and how their differences influence decisions on production volume, mold design, and overall product quality.
Choosing between liquid silicone rubber injection and compression molding techniques is a matter of matching material properties to performance characteristics.
So, whether you’re scaling up for high-volume production with liquid silicon rubber or prototyping with solid forms through conventional methods, this guide will help you transform your concept into reality with precision.
Understanding the Basics — What Are LSR and SSR?
When planning a silicone injection molding project, understanding the difference between silicone materials, specifically liquid silicone rubber (LSR) and solid silicone rubber (SSR)—is the foundation of successful material selection. Each type of silicone material has its own processing methods, physical characteristics, and ideal applications depending on the product’s required performance.
What is Liquid Silicone Rubber (LSR)?
LSR is a two-part synthetic polymer system, characterized by its liquid form before curing. LSR is typically processed using the LSR injection molding process, which involves metering, mixing, and injecting the material directly into a hot mold where it vulcanizes rapidly. The use of vulcanizing agents enhances its cross-linking reaction, resulting in products with superior flexibility, temperature resistance, and excellent resistance to chemical attack.
LSR’s liquid nature makes it highly suitable for forming complex shapes, intricate parts with thin wall thicknesses, and intricate mold cavities. Its broad range of applications includes medical devices, automotive components, electrical seals, and portable computing devices, especially where biocompatible nature, abrasion resistance, and thermal stability are critical.
Typical characteristics of LSR include:
- Exceptional heat resistance (up to 250°C and beyond)
- Extreme temperature performance, from cryogenic to high-heat conditions
- Excellent chemical resistance and weather resistance
- High tensile strength and tear strength
- Natural transparency allowing for multi-color or self-adhesive LSR applications
These properties make liquid silicone rubber the material of choice for high-performance applications in the medical industry and beyond.
What is Solid Silicone Rubber (SSR)?
On the other hand, solid silicone rubber (sometimes simply referred to as solid silicone) is supplied in a solid or semi-solid material state, usually as sheets, strips, or blocks. It is often manually processed using silicone compression molding or transfer molding, although it can also be adapted to injection molding machines through preforming.
SSR materials feature longer polymer chains compared to LSR, contributing to mechanical strengths like higher tear resistance and abrasion resistance. Solid silicone rubber sheets and molded components excel in high-stress environments requiring resistance to chemical exposure and extreme conditions.
Key properties of SSR include:
- Strong mechanical properties and durability
- Superior tear strength and elongation under stress
- Reliable insulation properties for electrical components
- Wide temperature range performance, though slightly less flexible than LSR
- Suitability for larger wall thicknesses and simpler shapes
Because of its physical properties and solid forms, SSR is often the better selection for low-volume production, engineering prototypes, protective covers, and custom logo silicone products that must endure harsh conditions and bodily fluids without rapid degradation.
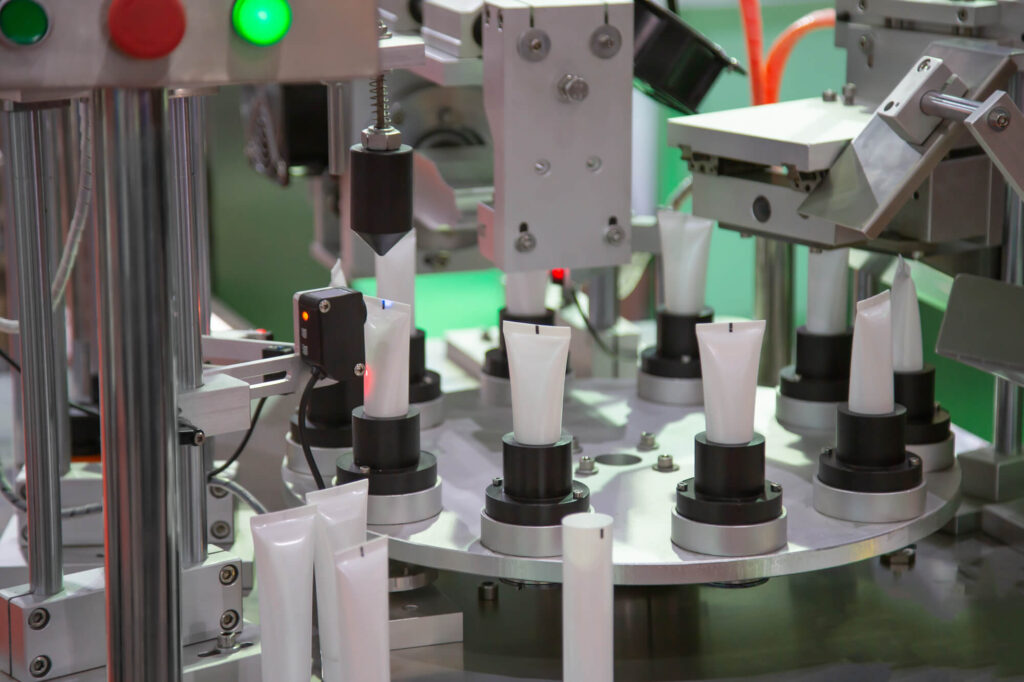
Molding Methods Explained
Choosing between liquid silicone rubber injection and solid silicone rubber molding is not only about material properties; it’s also about selecting the right manufacturing process to achieve the desired product quality, efficient production times, and cost control. Once you truly grasp how each material is processed—through liquid injection molding or compression molding—you will have an easier time deciding which is more compatible with your production volume and product requirements.
LSR Molding Process
The LSR injection molding process is how liquid silicone rubber is used in manufacturing and is known for its efficient process flow, making it ideal for high-volume production.
During liquid silicone rubber injection molding, two components of the liquid silicon rubber material (typically including vulcanizing agents) are precisely mixed in a static mixer and injected into a hot mold using specialized injection molding machines.
Once injected, the liquid form rapidly undergoes heat-activated curing inside the mold cavity, creating parts with exact reproduction of intricate details, complex shapes, and complex designs.
Main features of the LSR molding process:
- Fully automated, reducing labor costs and enabling automatic production
- Excellent for multi-cavity molds and multi-color part production
- Exceptional for thin-walled components, medical devices, and medical applications
- Best suited for exact reproduction of fine features in complex molds
- Shorter cycle times, enhancing time to market for products
The liquid injection molding method ensures a precise process that is perfect for biocompatible devices that must endure harsh environments, bodily fluids, or extreme temperatures without compromising integrity.
SSR Molding Process
Solid silicone rubber is typically processed using the compression molding process or transfer molding, which are more traditional manufacturing methods. In compression molding, pre-formed solid silicone material is manually placed into the open silicone mold cavity, and then high heat and pressure are applied to cure the material into the desired shape.
This more traditional method is particularly advantageous for producing solid forms with thicker profiles, durable protective covers, and solid silicone rubber sheets where design flexibility and ultra-fine details are less critical.
Key features of the SSR molding process:
- Lower upfront materials costs and tooling investment
- Ideal for low-volume production runs and large, sturdy parts
- Allows use of abrasion-resistant, high-temperature resistant formulations
- Better suited for parts with substantial wall thickness or simpler silicone product design
While compression molding takes longer than liquid injection molding, it remains a reliable method for industries needing rugged components with strong mechanical properties and chemical stability.
Comparative Analysis — LSR vs. SSR
To choose the right type of silicone material for your project, a clearer comparison between how liquid silicone rubber and solid silicone rubber score across core performance metrics is extremely useful. These distinct characteristics—ranging from mechanical properties and processing methods to temperature resistance and design flexibility—can greatly influence the success of a part under extreme conditions.
This comparative analysis lays out key factors across use-case-specific needs and performance expectations.
Physical and Mechanical Properties
Property | Liquid Silicone Rubber (LSR) | Solid Silicone Rubber (SSR) |
Physical Form | Liquid two-part compound | Solid or semi-solid sheets or blocks |
Processing Method | Liquid injection molding | Compression or transfer molding |
Tear Strength | Moderate to high, good for thin-walled features | High, excellent for rugged components |
Tensile Strength | Consistent and high across thin profiles | Higher in thick sections due to longer polymer chains |
Chemical Resistance | Excellent, especially for acids, oils, and solvents | Excellent, depending on compound formulation |
Heat Resistance | Up to 250°C or more, stable at high temperatures | Strong, though slightly less stable at upper extremes |
Temperature Range | Wide (-50°C to +250°C) | Wide (-40°C to +230°C) |
Biocompatibility | Medical-grade options are widely available | Also available, but limited to specific grades |
Flexibility | Superior in complex geometries | More rigid in large/thick parts |
Transparency / Appearance | Naturally transparent, good for pigmentation | Typically opaque |
Production Efficiency and Volume Suitability
When assessing scalability and production volume alignment, LSR shines in automatic production settings, while SSR is better matched with low-volume production runs.
- LSR is preferred when:
- Products require precise duplication of complex molds
- Projects demand shorter cycle times and a fast time to market
- Manufacturers use multi-cavity tools and advanced injection units
- SSR is preferred when:
- Parts have thicker walls or simpler silicone rubber mold cavity shapes
- Budgets are limited for tooling, and labor costs are manageable
- There is a need for abrasion resistance in solid silicone applications
Design Considerations and Part Complexity
Because of its liquid nature, LSR enables exact reproduction of complex shapes, including undercuts, microfeatures, and ultra-thin geometries. In contrast, SSR’s physical rigidity limits it to silicone rubber products designed with fewer features requiring intricate flow control.
LSR also supports multi-color, multi-material molding through silicone over-molding, making it a natural fit for custom logo silicone products, biocompatible devices, and medical prototypes.
SSR, however, offers unmatched value when producing protective covers, solid silicone rubber sheets, or thick-section parts used in automotive and industrial applications that face harsh environments.
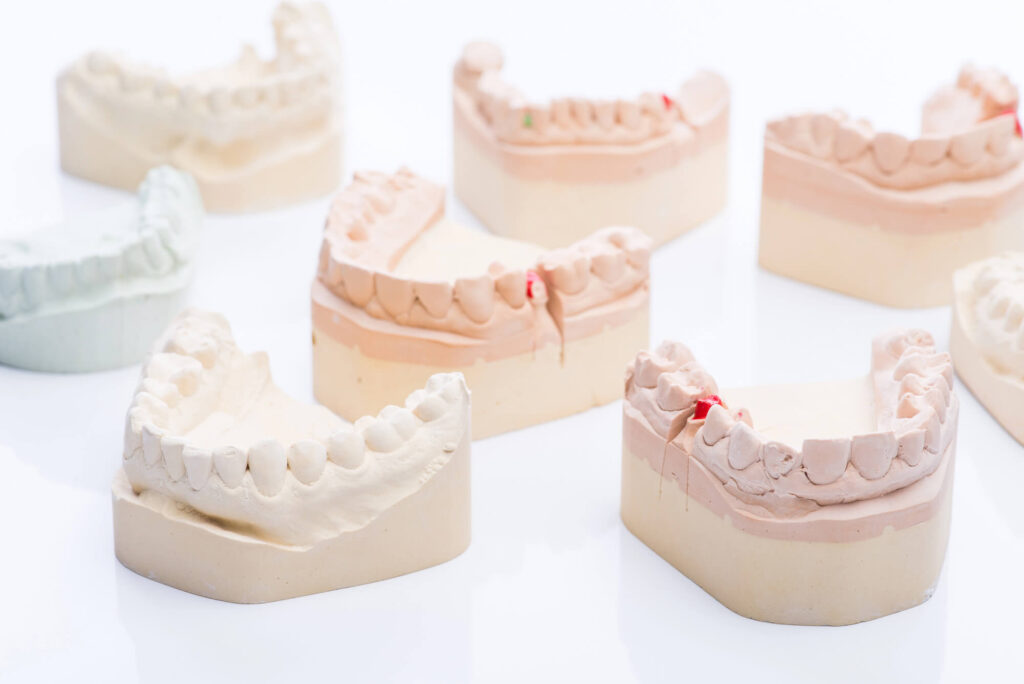
Applications by Industry
Both liquid silicone rubber (LSR) and solid silicone rubber (SSR) serve a wide range of industries due to their shared yet distinct strengths in handling extreme temperatures, chemical resistance, and complex product requirements. However, knowing which type of silicone suits which field is key to optimizing performance, cost-efficiency, and manufacturing process flow.
Medical Industry
In the medical industry, biocompatibility, chemical stability, and resistance to bodily fluids are non-negotiable. LSR’s medical-grade variants make it the dominant choice for medical applications that demand clean-room manufacturing, sterilization compatibility, and precision.
LSR Applications:
- Catheters, valves, and feeding tubes
- Baby pacifiers and medical-grade teething rings
- Biocompatible seals and soft-touch instrument grips
- Wearable health and diagnostic devices
These components benefit from LSR’s liquid injection molding process, ensuring consistent physical properties, seamless geometry, and a short time to market.
SSR Applications:
- Surgical tool grips and handles
- Dental molds
- Thicker medical support pads or cushions
SSR’s solid forms are suited for low-complexity, durable parts in high-stress environments where mechanical properties such as tear strength are vital.
Automotive and Aerospace
In transportation, materials face harsh environments including vibration, thermal cycling, oil exposure, and UV radiation.
LSR Applications:
- Electrical connector seals and housings
- Vibration-damping pads
- Under-hood gaskets for high-temperature resistance
SSR Applications:
- Engine bay grommets and dust covers
- Thicker insulation mats and cabin seals
- Die-cut sheets for mounting and sealing large panels
SSR’s robust mechanical strengths and ability to be formed into solid silicone rubber covers make it ideal for demanding conditions over long service lives.
Consumer and Electronics Products
In electronics and lifestyle products, surface treatment, design flexibility, and compact sizing drive material selection.
LSR Applications:
- Keypads, buttons, and switch covers
- Smartwatch bands and wearable shells
- Personal care device over-molds
SSR Applications:
- Protective sleeves for chargers or cables
- Large molded grips for gaming or ergonomic products
Baby and Kitchenware Products
Here, food-grade certification, anti-yellowing, and sensory characteristics are top priorities.
LSR Applications:
- Baby bottles, nipples, and spoons
- Silicone bakeware and spatulas
- Soft-touch kitchen tools and suction bases
SSR Applications:
- Jar seals, thick cutting mats
- Oven mitts and heat-resistant handle sleeves
While both materials can be food-safe, LSR’s compatibility with multi-color molds, precision geometry, and vulcanized material finish gives it an edge in premium-grade kitchenware and baby products.
Cost Considerations
Cost is a central factor in determining whether liquid silicone rubber or solid silicone rubber is the better fit for a given silicone rubber injection molding project. While both materials are cost-effective in their own right, they differ in upfront costs, processing methods, and long-term production efficiency.
Tooling and Setup Costs
LSR molding typically requires a higher initial investment due to the need for precision-built molds, injection units, and metering devices. These tools are designed to accommodate the liquid nature of LSR and support automatic production with multi-cavity mold capabilities.
- Higher tooling cost but optimized for repeatability and long-term ROI
- Ideal for high-volume production where the cost-per-unit decreases significantly over time
- Upfront cost offset by fewer labor inputs and reduced excess material
SSR processing, usually via compression molding, involves simpler tooling. These molds are generally less expensive to produce, making SSR attractive for low-volume production runs or early-stage engineering prototypes.
- Lower tooling cost and faster to build
- Better suited to small batches and traditional methods
- Tooling may require more manual intervention, increasing labor over time
Materials and Manufacturing Costs
Both LSR and SSR use high-quality silicone raw materials, but LSR compounds may include more specialized additives such as flame retardants, conductive agents, or self-adhesive properties. This can increase material cost, though it offers added functionality and process efficiency.
- LSR materials often allow for shorter curing cycles, reducing energy and labor costs
- SSR materials may be slightly less expensive per kg, but result in longer manufacturing process durations and more manual handling
Lifecycle Cost and Scalability
For projects requiring thousands or millions of parts over time, LSR is clearly more cost-effective due to:
- Shorter cycle times on injection molding machines
- Efficient production times with low reject rates
- Enhanced quality control inspection built into automated systems
SSR offers lower-cost entry for simpler or custom logo silicone products, thicker parts, or solid silicone rubber sheets, but is less efficient at scale.
In summary, LSR is the better financial decision for long-run, high-performance applications, while SSR provides a practical choice for small series production, basic geometries, or budget-limited initiatives.
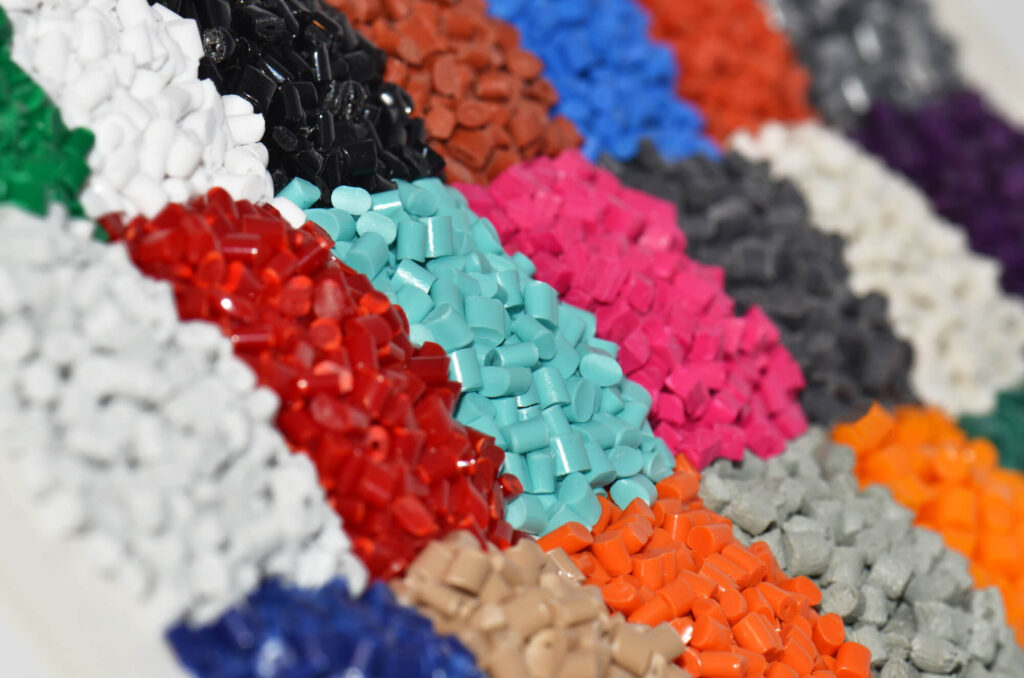
Material Selection: When to Choose LSR vs. SSR
Selecting between LSR vs SSR silicone molding isn’t just about understanding their material properties—it’s about aligning the right silicone type with your part’s end-use, performance requirements, and production parameters. Below is a decision-making framework to help engineers, designers, and procurement teams choose with clarity and confidence.
Choose LSR If Your Project Requires:
- High-volume production with tight tolerances and automation
- Complex geometries or intricate mold cavities where exact reproduction is critical
- Thin-walled parts or multi-cavity mold runs
- Biocompatibility for use in medical devices, wearable health monitors, or components in contact with human tissue
- Resistance to bodily fluids, extreme temperatures, or aggressive cleaning agents
- Excellent surface finish and the option for multi-color or self-adhesive molding
- Faster time to market and reduced manual labor through an efficient process
Use cases include medical-grade tubing, baby products, personal care devices, over-molded electronics, and seals for automotive or aerospace environments.
Choose SSR If Your Project Involves:
- Small batch production or limited-run prototyping with budget constraints
- Parts that require thick cross-sections or a solid silicone rubber sheet format
- Simpler shapes or traditional compression molding methods
- Durable components for high-stress environments such as protective covers, industrial grommets, or vibration dampers
- Strong tear resistance and mechanical strength in harsh operating conditions
- Situations where tooling needs to be low-cost and quickly fabricated
Use cases include engine bay insulators, custom-molded electrical protectors, thick-section cushioning pads, and ergonomic industrial grips.
The Importance of Application Context
No silicone rubber type is universally superior. Each has strengths tailored to specific design constraints, production volumes, and operating environments. Understanding the material’s physical characteristics, from tensile strength and thermal stability to resistance to chemical exposure and abrasion, is essential in determining the right path forward.
Working with an experienced partner like Kenvox ensures your project benefits from correct material selection, optimized tooling design, and quality control throughout every phase of silicone product development.
Ready to Mold Your Next Idea Into Reality?
Understanding the nuances between liquid silicone rubber and solid silicone rubber is essential for anyone involved in silicone injection molding projects. Each material offers a distinct balance of physical properties, processing methods, and application-specific advantages—from the precision and automation of LSR to the rugged durability and cost-efficiency of SSR.
By mapping your product’s needs to the right form of silicone, you unlock greater efficiency, reliability, and long-term value.
Kenvox’s Capabilities in Silicone Molding
At Kenvox, we don’t just deliver molded parts; we help you bring high-performance ideas to market with speed, confidence, and precision.
- Over 20 years of experience in both LSR and SSR molding.
- State-of-the-art silicone facilities with 50+ machines.
- In-house mold design and ERP-integrated traceability.
- Case studies in medical, automotive, baby products, and kitchenware.
Contact Kenvox today to discuss your project requirements and discover which silicone solution is best suited to your performance, design, and production goals.