Rapid prototyping is a critical step in the product development process, allowing manufacturers to quickly test, refine, and improve designs before committing to full-scale production. Among the various methods and materials used for quick prototypes, silicone molding stands out as one of the most effective rapid prototyping techniques due to its flexibility, precision, and cost efficiency.
From automotive components to medical devices and consumer products, silicone molding enables the creation of high-quality physical models and prototypes that closely resemble the final product.
Read and explore how silicone molding revolutionizes rapid prototyping, its different methods, and the benefits it offers across industries.
What Is Silicone Molding for Rapid Prototyping?
Silicone molding is a manufacturing process that uses silicone materials to create physical prototypes and small-batch production parts. This prototyping process is highly valued for its high fidelity to original designs, mechanical properties, and ability to replicate intricate details.
How Businesses Benefit from Rapid Prototyping Before Full-Scale Production
- Identifies design flaws early: Prevents the design process from making costly errors before mass production, which is especially useful with complex designs.
- Speeds up product development cycles: Reduces time to market, giving the business a competitive edge.
- Allows for cost-effective testing: Evaluates material properties, aesthetics, surface finish, and functionality.
- Facilitates investor and customer feedback: Helps refine the finished product.
- Enables quick design iteration: Adjustments can be made without expensive production tooling changes.
Key Features of Silicone Molding for Prototyping
- Exceptional Precision: Silicone molding excels in delivering remarkable precision, which is crucial for prototyping.
- Quick Turnaround Times: One of the standout benefits compared to traditional methods is its ability to significantly reduce time to market and turnaround times.
- Material Versatility: Silicone molding offers impressive material versatility, allowing for easy replication of both rigid and flexible materials.
- Cost-Effectiveness for Low-Volume Production: When it comes to low-volume production runs, silicone molding proves to be a cost-effective solution.
Types of Silicone Molding Used in Rapid Prototyping
Different silicone molding techniques are used depending on the prototype’s complexity, material properties, and end-use application.
Liquid Silicone Rubber (LSR) Molding
This is a type of liquid injection molding process where a compound called liquid silicon rubber is inserted into molds for high-precision and complex prototypes.
Key Benefits:
- High tensile strength and durability.
- Excellent resistance to extreme temperatures.
- Ideal for a variety of industries, from the medical industry to the automotive industry and even wearable tech.
- Scalable for low-volume to high-volume production.
Common Applications:
- Medical prototypes (implants, tubing, drug delivery devices).
- Electronics (protective casings, keypads).
- Consumer products (soft-touch grips, baby products).
Compression Molding with Silicone
Compression molding uses solid silicone rubber (SSR) placed into a heated mold and compressed into shape.
Key Benefits:
- Best for high-strength mechanical components.
- Excellent for automotive and aerospace applications.
- Works well with thermally resistant materials.
Common Applications:
- Aerospace components.
- Automotive components (gaskets, seals).
- Industrial machine prototypes.
Room-Temperature Vulcanization (RTV) Silicone Molding
RTV silicone molding is a low-cost, fast-prototyping method where silicone cures at room temperature.
Key Benefits:
- No need for heat curing – Reduces gel time and vacuum time.
- Best for quick-turnaround prototypes.
- Works well for soft and flexible parts.
Common Applications:
- Custom gaskets and seals.
- Concept models for product testing.
- Wearable components with silicone rubber molds.
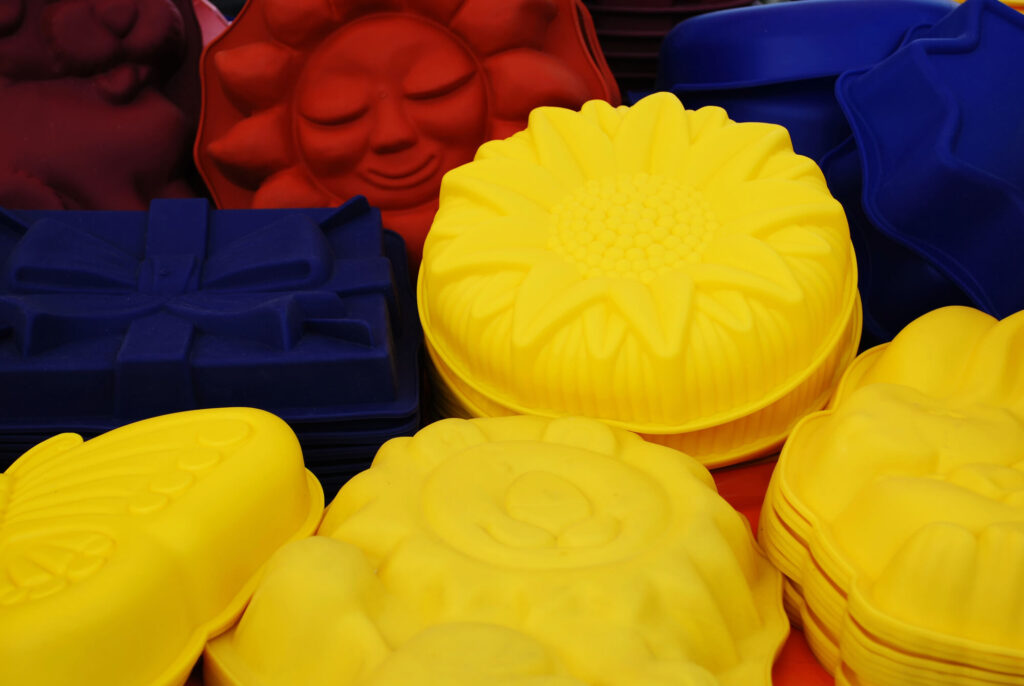
How the Silicone Molding Process Works for Rapid Prototyping
Silicone molding follows a streamlined and efficient process, making it ideal for rapid prototype development.
Key Steps in the Silicone Molding Process
- Creating the Master Pattern: This initial step usually involves producing a master pattern using a 3D printer or employing CNC machining techniques, ensuring precision and detail in the design.
- Making the Silicone Mold – The master pattern serves as the foundation for crafting a flexible mold cavity, which will later be used to replicate the design reliably.
- Injecting or Pouring Silicone – Once the mold is ready, the molding machines get to work, and the cavity is filled with either liquid silicone rubber (LSR) or room-temperature vulcanizing (RTV) silicone, depending on the specific requirements of the project.
- Curing and Finishing – After the silicone is poured, the prototype undergoes a curing process to solidify it, followed by finishing touches to achieve a polished and smooth finish and surface, ready for testing or production.
Different Mold Materials for Rapid Silicone Prototyping
Aside from silicone molds, various materials can be used in the rapid prototyping process.
- Thermoplastic Mold: Created using 3D printing materials, plastic molds allow for quick manual injection of liquid silicone rubber. However, the 3D printing method can still have higher upfront costs than silicone, especially if the project scope does not require it.
- Aluminum Molds (Soft Tooling): Lightweight and cost-effective, soft aluminum molds replicate details with high precision. Typically used for runs of up to 10,000 parts. Aluminum molds are standard soft tooling options for prototyping but mean higher upfront costs and might not be viable for low-volume prototyping.
- Steel Molds (Pre-Production Tooling): Durable and accurate, these molds produce all part details without secondary operations.
- Steel Insert in Mold Base: Some manufacturers use low-cavity mold bases with interchangeable steel inserts for more economical solutions.
How Rapid Prototyping with Silicone Molding Compares to Other Methods
Method | Speed | Cost | Complexity | Ideal Use Case |
3D Printing Technologies | Fast | Low | Moderate | Concept models |
Silicone Molding | Fast | Medium | High | Functional prototypes |
CNC Machining | Medium | High | High | Rigid parts, metal components |
The Key Benefits of Rapid Prototyping with Silicone Molding
Silicone molding offers a range of advantages that make it a top choice for fast, high-quality prototyping.
1. Production Efficiency and Speed
One of the standout benefits of silicone molding is its ability to significantly reduce time to market and turnaround times compared to the traditional injection molding process. This rapid prototyping method enables designers to quickly produce and iterate on prototypes, facilitating swift functional testing. By accelerating the prototyping process and shortening the overall product development process, teams can gather feedback and make necessary adjustments faster, ultimately leading to more efficient product development cycles.
2. Cost Savings for Low-Volume Production
When it comes to low-volume production runs, silicone molding proves to be cost-saving. Traditional tooling methods like metal molds often incur high initial costs, making them prohibitive for smaller production needs. It is cost-effective for batch prototypes and testing for this reason and minimizes these expenses while still delivering high-quality, functional prototypes, ensuring that businesses can innovate without straining their budgets.
3. High Precision & Detail Replication
With this type of molding, manufacturers get remarkable precision with their prototypes. This technique allows designers to achieve intricate details, tight tolerances, coarse details, and complex geometries that are challenging to create using other methods. Each prototype can accurately reflect the intended design, ensuring that every fine element is captured without compromise. Suitable for medical prototypes and engineering prototypes.
4. Material Flexibility & Versatility
It offers impressive material versatility, allowing for easy replication of rigid, soft, heat-resistant, and even biocompatible and flexible materials. This adaptability means that designers can test various material properties and behaviors before committing to a final product choice. For this reason, it’s used heavily in engineering prototypes for automotive components and consumer electronics. Being able to simulate different material scenarios enables more informed decision-making in the early stages of development.
5. Easy Design Iteration & Modification
Molds can be quickly adjusted to accommodate design changes, allowing for rapid tooling and bridge production prior to full-scale manufacturing. This flexibility facilitates a smoother transition from the prototype phase to mass production, ensuring that any needed modifications can be made efficiently without significant delays in the development timeline.
Industries That Benefit the Most from Rapid Custom Silicone Prototypes
Silicone molding is widely used across various industries for product testing and design validation.
- Medical Industry: Biocompatible medical prototypes, such as implants, drug delivery systems, and surgical instruments, are created using silicone molding. This process allows for advanced prototype molding, enabling thorough functional testing of medical devices before they are brought to market.
- Automotive & Aerospace: The automotive and aerospace sectors use silicone molding to produce heat-resistant gaskets and seals, which are crucial for ensuring safety and efficiency in vehicles and aircraft. Moreover, lightweight and durable precision-machined components are created, contributing to improved performance and fuel efficiency.
- Consumer Electronics & Wearables: Silicone molding is used to design protective casings, soft-touch grips, and keypads for consumer electronics and wearables. This technology facilitates the development of high-fidelity prototypes, allowing manufacturers to test user experience and ergonomics effectively.
- Industrial & Robotics: Silicone molding supports the industrial and robotics sectors by providing custom silicone prototypes for robotics and automation tools. This includes the production of shock-resistant and flexible components that enhance the functionality and reliability of robotic systems in various applications.
Kenvox – Your Partner in Rapid Prototyping with Silicone Molding
Rapid prototyping with silicone molding is the fastest way to bring innovative designs to life with high-quality, cost-effective materials.
Kenvox specializes, among other methods, in:
- Liquid Silicone Rubber (LSR) Molding
- High-Precision Prototyping for Various Industries
- Silicone Compression Workshops
- Silicone Epoxy
- Solid Silicone Injection
If you’re looking for a reliable contract manufacturer for silicone molding, Kenvox can help bring your ideas to life quickly and efficiently.
Contact Kenvox today to discuss your rapid prototyping needs!