Liquid Silicone Rubber (LSR) is a high-performance silicone rubber material widely used in precision molding due to its exceptional flexibility, durability, and resistance to extreme temperatures. Among its many applications, LSR is frequently utilized in the overmolding process, where it is bonded to another substrate material such as metal or plastic to enhance functionality.
Overmolding is particularly beneficial in industries requiring strong chemical resistance, mechanical bonding, and high-performance requirements, such as medical device manufacturing, automotive components, electronic devices, and industrial equipment.
However, overmolding LSR onto rigid substrates comes with unique challenges, including adhesion issues, material compatibility concerns, mold design complexities, and cost optimization.
Kenvox specializes in overcoming these challenges by offering high-quality overmolding solutions, ensuring strong bond strength, product quality, and enhanced durability for a wide range of industries. This blog explores the key challenges of LSR overmolding and the best solutions to optimize performance, production efficiency, and product design.
What Is Liquid Silicone Rubber Injection Molding and Why It’s Used in Overmolding?
Liquid Silicone Rubber (LSR) is a two-part thermosetting material that is processed through liquid injection molding, which allows for high precision, soft material flexibility, and tight tolerances in finished products.
The injection molding process involves mixing the raw material using a static mixer, injecting it into a pre-designed mold, and curing it under controlled heat and pressure. This process ensures that LSR retains its mechanical properties, making it an ideal material for multi-shot molding, insert molding, and complex designs.
Advantages of LSR in Molding
- Extreme Temperature Resistance: Withstands both high and low temperatures, making it suitable for medical applications, automotive industry, and industrial applications.
- Chemical Resistance: Resists exposure to hydrochloric acid, industrial chemicals, and harsh environmental conditions.
- Biocompatibility: Suitable for surgical instruments, medical equipment, and food-grade applications.
- Mechanical Properties: Provides enhanced durability, excellent tear strength, and consistent quality in finished products.
- Intricate Designs & Precision Molding: Liquid Silicone Rubber allows for intricate details and complex geometries with tight tolerances.
Why Overmolding with Liquid Silicone Rubber is Widely Used
Overmolding with LSR, also known as two-shot molding, LSR insert molding, silicone overmolding, or liquid silicone rubber overmolding, involves molding silicone rubber material over another rigid material, such as metal substrates or plastic substrates. This process is used across a wide range of applications, including:
- Medical Devices: Protective seals, soft-touch surfaces, biocompatible coatings for surgical instruments and medical equipment.
- Automotive Industry: Rubber overmolding for vibration-dampening components, gaskets, and high-performance seals.
- Electronic Components: Protective covers, handheld devices, and overmolded features in consumer electronics.
- Industrial Equipment: High-strength, chemically resistant seals for heavy-duty machinery.
Overmolding enhances product durability, provides waterproofing, and creates soft-touch ergonomic surfaces. Different overmolding materials can be used, including metal inserts, plastic inserts, and rigid substrates, depending on design constraints and functional requirements.
Overview of the LSR Overmolding Process
- Preparation of Substrate Material: Initially, the surface of metal protective layers or plastic materials undergoes a pre-treatment process. This step is crucial as it is designed to enhance and ensure optimal adhesion between the two different materials used in the overmolding process.
- Injection Molding Process: The actual liquid silicone injection molding phase is conducted with great care and precision. It is essential to utilize highly accurate injection parameters and settings to ensure that the liquid silicone is injected into the mold effectively and uniformly, resulting in high-quality components.
- Curing Process: Following the injection, the silicone rubber material is exposed to a controlled heating process. This step is vital as it facilitates the formation of a robust chemical bond, ensuring that the silicone adheres firmly to the substrate and provides the necessary strength and durability.
- Post-Molding Quality Control: After the molding procedure is complete, product durability and mechanical features undergo rigorous testing. This phase ensures that the finished products comply with necessary regulatory requirements while also confirming consistent wall thickness uniformity throughout the various components.
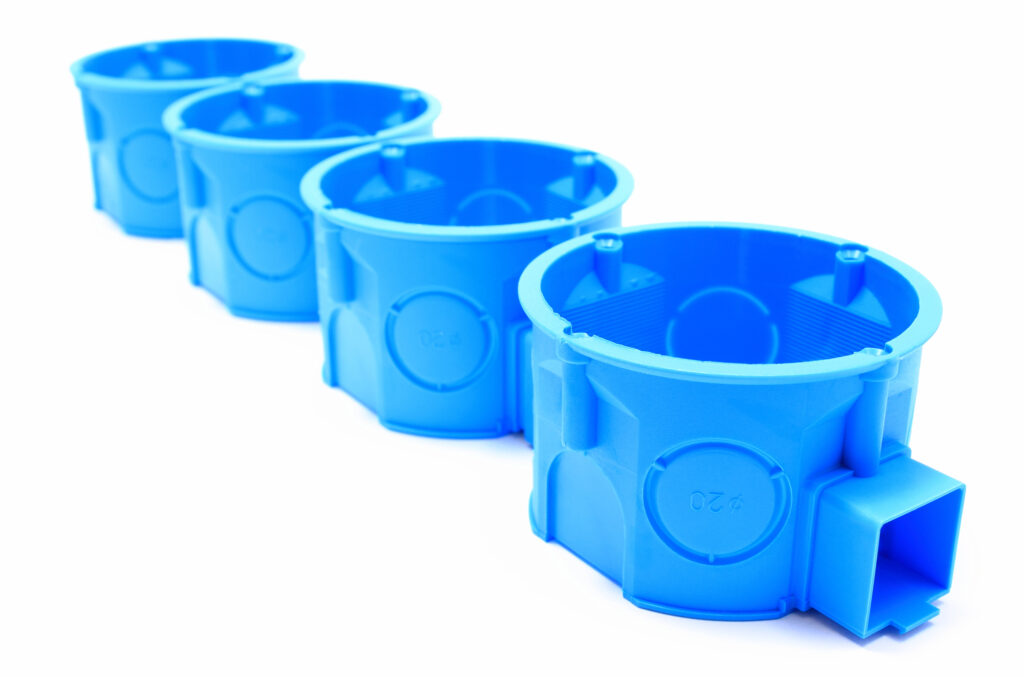
Key Challenges in Overmolding with LSR
Despite its advantages, the overmolding process with LSR presents several potential issues, including poor adhesion, mechanical bonding difficulties, molding temperature inconsistencies, and production costs.
Before achieving strong chemical bonds and consistent quality, manufacturers must address the following overmolding material challenges:
Adhesion Issues Between LSR and Substrate Materials
One of the most significant challenges in overmolding with liquid silicone rubber is achieving a strong chemical bonding between LSR and the substrate materials. LSR does not naturally adhere well to many plastic materials or metal substrates, leading to poor adhesion or even delamination over time. The surface energy of the substrate plays a crucial role in determining bond strength. Surface treatments such as plasma treatment, corona treatment, or primers are often required to improve adhesion and enhance mechanical bonding.
Material Compatibility and Selection
Choosing the right overmolding material is critical for ensuring optimal adhesion and durability. Some plastic substrates, such as polypropylene (PP) and polyethylene (PE), have poor adhesion performance with LSR and require adhesion promoters or primers. Chemical compatibility between LSR and the base material must be assessed to ensure a strong chemical reaction during the bonding process.
Mold Design and Processing Challenges
Proper mold designs are essential for preventing defects such as flash formation, air entrapment, and inconsistent wall thickness. The molding temperature, shut-off designs, and injection pressure must be carefully controlled to avoid gas traps and incomplete filling of intricate designs.
Curing and Processing Time Considerations
The curing process in liquid silicone injection molding requires precise temperature and injection speed adjustments to balance cycle time and product quality. Over-curing or under-curing can lead to material waste and production costs.
Shrinkage and Dimensional Stability
During curing, LSR can shrink slightly, affecting tight tolerances and mechanical features. Adequate venting and injection hold pressure control help compensate for these dimensional changes.
Cost and Production Efficiency Challenges
LSR overmolding increases design complexity, impacting high-volume production costs. The use of automated molding machines and lean manufacturing processes is essential to enhance production efficiency while maintaining consistent quality.
Solutions to LSR Overmolding Challenges
To overcome these challenges, manufacturers implement advanced manufacturing processes and careful material selection.
Optimizing Adhesion Techniques
Applying surface treatments such as plasma, corona, and primer coatings significantly improves adhesion performance. Mechanical interlocks and textured surfaces further enhance the mechanical coupling of overmolded materials.
Proper Material Selection and Preparation
Selecting compatible materials is critical to achieving a strong chemical bond. Conducting pre-tests on overmold materials helps determine the most effective bonding process.
Best Practices in Mold Design and Process Control
Ensuring tight tolerances, adequate mold venting, and precise injection unit adjustments improves overmolded product durability.
Enhancing Production Efficiency and Cost Optimization
By incorporating automated molding machines, injection speed control, and modern manufacturing techniques, manufacturers can reduce production costs while maintaining quality control measures.
Why Kenvox is Your Ideal Partner for LSR Overmolding
Kenvox specializes in liquid silicone rubber injection molding, ensuring high precision, material compatibility, and optimal production efficiency. Our expertise in modern manufacturing techniques, intricate details, and high-volume production makes us the ideal choice for businesses requiring overmolded materials with enhanced durability.
Contact Kenvox today to discuss your LSR overmolding project and benefit from our expertise in LSR materials, product design, and manufacturing processes.