Imagine creating complex, multi-material products in a single mold cycle that reduces assembly steps, enhances part reliability, and unlocks new levels of design freedom.
This is the promise of multi-shot silicone molding, a transformative technology revolutionizing how integrated components are manufactured across a wide range of industries.
From medical devices and consumer products to automotive applications, the ability to mold multiple materials together, especially with Liquid Silicone Rubber (LSR), is reshaping what’s possible in product integration.
Read on and learn more about how two-shot molding can revolutionize your manufacturing process as well.
What Is Multi-Shot Silicone Molding?
Multi-shot molding, also known as two-shot injection molding or 2K molding, is an advanced injection molding process where two or more distinct materials (or colors) are injected into a mold in successive stages. Unlike single-shot molding, which requires post-mold assembly or bonding, multi-shot processes produce fully integrated parts within a single cycle.
When silicone is introduced into this process, especially Liquid Silicone Rubber (LSR), its compatibility with thermoplastic materials allows for the combination of soft and hard elements into one seamless finished product. Specialized liquid injection molding machines equipped with multiple injection units, dynamic mixers, and heated mold cavities enable this level of precision.
Role of Liquid Silicone Rubber (LSR)
Liquid Silicone Rubber is a versatile material valued for its:
- High tensile strength and elongation, allowing it to stretch without breaking.
- Exceptional chemical resistance, abrasion resistance, and UV stability.
- Outstanding biocompatibility with human tissue and body fluids, making it ideal for medical-grade silicones and medical applications.
- Consistent rubber behavior under extreme temperatures (up to 200°C), retaining its shape and function.
These properties make LSR the material of choice for medical products, infant products, electronic products, and personal care items.
Differences Between Overmolding and Two-Shot Liquid Silicone Rubber Injection Molding
While overmolding and two-shot molding can yield similar outcomes—a combination of two different materials—their manufacturing processes are fundamentally different:
- In two-shot liquid silicone injection molding, the materials are injected sequentially into a single mold, achieving a chemical and physical bond with superior integration.
- In contrast, overmolding places a pre-molded component into a new mold, where liquid silicone rubber material is injected over or around it. This is often used when bonding to metal or other substrates; and despite its advantages, does present potential issues.
The key takeaway? Two-shot molding ensures stronger bond strength, better process efficiency, and more consistent results over periods of time.
Core Benefits of Multi-Shot Silicone Molding in the Production Process
Material and Design Flexibility
Multi-shot injection molding supports a wide range of plastic materials, thermoplastic elastomers, and liquid silicone materials, enabling:
- Multi-colored, multi-textured, or multi-hardness products
- Integration of ergonomic, soft-touch surfaces with rigid frameworks
- Production of complex geometries and intricate designs to meet exacting design requirements
Improved Manufacturing Efficiency
- Eliminates separate processes and manual assembly
- Reduces labor costs, production steps, and cycle time
- Yields higher production speed and lower production costs per unit
Enhanced Precision and Surface Finish
- Supports tight tolerances and high-quality surface finish
- Minimizes material waste with cold runner and sprue runner systems
- Delivers smooth surfaces even in multi-cavity molds
How Multi-Shot Silicone Molding Enhances Product Integration
Unified Component Structures
Multi-shot molding allows for the integration of distinct materials, such as thermoplastics and LSR, into one cohesive unit:
- Avoids the need for adhesives or mechanical fasteners.
- Ensures tight bonds and eliminates misalignments.
- Common in pet products, baby bottles, and electric connectors.
Structural & Functional Synergy
Using liquid injection molding processes, manufacturers can embed functionalities directly into the molding project:
- Soft buttons on electronic housings.
- Water-tight seals on medical equipment.
- Ergonomic grips on power tools.
Reduced Risk of Failure
- Reduces risks from bacteria growth, chemical solutions, and interface breakdowns.
- Withstands steam autoclaving, ethylene oxide sterilization, and extreme heat.
- Enhances product integrity in critical applications.
Why Silicone? – The Ideal Material for Advanced Molding
Silicone, specifically liquid silicone rubber injection, has emerged as a preferred choice for the two-shot molding process due to its unique characteristics. This versatile material offers exceptional durability, flexibility, and resistance, making it ideal for innovative design and manufacturing solutions across a wide range of applications and industries.
Key Properties Supporting Integration
LSR exhibits a range of properties that support complex integration:
- Excellent mechanical properties and electrical surface insulations
- Exceptional color consistency and color diversity options
- Molding accuracy is ideal for volume production and medical sector regulations
Durability Across Environments
- Highly resistant to high temperatures, chemical inertness, and UV degradation
- Withstands both hot and cold runner systems
- Remains stable in automotive components and electronic devices used in extreme conditions
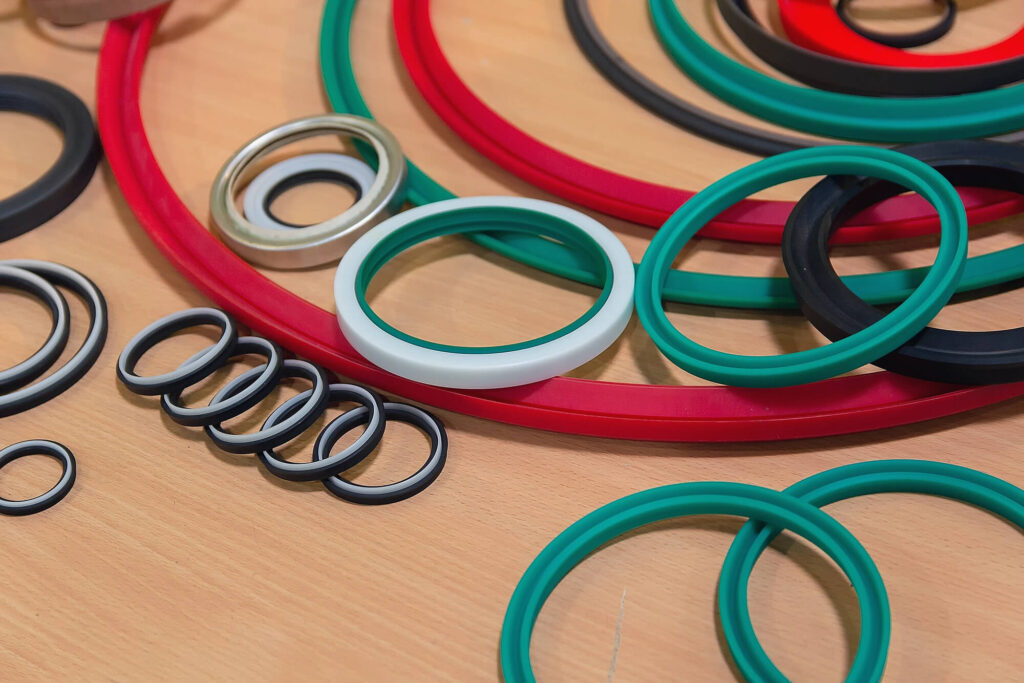
Top Industrial Applications of Multi-Shot Silicone Molding
In today’s manufacturing landscape, multi-shot silicone molding has emerged as a pivotal technology, driving advancements across a wide range of products and industries.
Multi or two-shot molding’s versatility and efficiency make it an ideal choice for production strategies, enabling companies to create innovative, durable, and highly integrated products.
Here, we explore common applications where multi-shot silicone molding is making a significant impact.
Medical Industry
- Medical devices such as seals, valves, and components used with body fluids
- Wearable sensors, biosensors, and infant products like bottle nipples
- Applications demanding sterilization and consistent quality over time
Consumer & Electronics
- Kitchen tools, personal care items, and smartphone cases.
- Electronic components like multi-pin connectors, switches, and housing with embedded LSR seals.
Automotive & Aerospace
- Automotive applications requiring tight bonds and heat resistance.
- Vibration dampeners, gaskets, and special applications in aerospace assemblies that require complex designs.
Kenvox’s Expertise in Silicone Molding and Integration
Kenvox is right at the forefront of innovation in silicone molding, leveraging advanced technology and industry expertise to deliver exceptional multi-shot molding solutions.
With a commitment to precision and quality, Kenvox helps businesses across various industries achieve superior product integration and performance.
Proprietary Tools & ERP-Based Control
Kenvox operates with over 50 advanced injection molding machines and proprietary ERP-based systems for:
- Monitoring every production cycle and optimizing molding methods
- Managing mold clamp pressure, mold designs, and sets of molds in multi-injection molding environments
Their expertise includes:
- Liquid silicone injection molding
- Silicone compression molding
- Transfer molding process
- LSR 2-shot injection molding process
End-to-End Manufacturing Capabilities
- In-house secondary processes: laser engraving, ultrasonic welding, vacuum plating.
- Integrated solutions for product requirements from single-component to multi-component molding.
- ISO9001, ISO14001, ISO13485, TS16949 certified.
The Future of Integrated Manufacturing with Kenvox
The evolution of silicone injection molding technology, particularly LSR 2-shot molding, marks a significant leap in how integrated products are conceived and produced.
For companies looking to optimize design complexity, reduce initial investments, and ensure product reliability, multi-shot or multi-component injection molding with silicone presents the ideal solution.
Explore more on our Silicone & Rubber Molding and Manufacturing pages.
Contact Kenvox today to bring your next silicone molding project to life with precision, performance, and unmatched process efficiency.