Liquid Silicone Rubber (LSR) injection molding has revolutionized the manufacturing landscape, offering a unique blend of flexibility, durability, and precision that traditional materials often struggle to achieve. This advanced process allows for the production of intricate components with remarkable detail, making LSR an ideal choice for industries ranging from automotive to consumer goods and medical applications.
However, the success of LSR injection molding is not solely reliant on the material itself; it hinges significantly on the mold design. Effective mold design serves as the backbone for achieving high-quality molded parts, ensuring that they meet rigorous performance standards and patient safety requirements. Everything from gate location, mold temperature, and draft angles to the injection pressures used in the manufacturing process impacts the physical properties of the finished product. Careful attention to mold design can profoundly influence the final product’s integrity and functionality.
In this guide, we will explore key mold design considerations, LSR part design guidelines, quality challenges, and best practices to optimize the silicone molding process for high-quality LSR parts. By understanding these fundamental aspects, manufacturers can harness the full potential of LSR injection molding to create high-quality, reliable products.
Understanding Liquid Silicone Rubber (LSR) and Its Applications
LSR is a thermoset plastic material that offers a wide range of benefits over thermoplastic materials. Unlike traditional methods like thermoplastic injection molding, LSR is injected as a liquid and undergoes a curing process in a closed cavity to form a solid, rubber-like material. The material’s mechanical properties make it an ideal material for intricate geometries that require tight tolerances and finer tolerances.
Liquid silicone rubber molding stands out with these key advantages:
- Versatility: LSR can be molded into intricate shapes and designs, making it suitable for a wide range of applications, from automotive components to medical devices.
- Lightweight yet strong: Ideal for wearable medical devices, consumer electronics, and industrial seals.
- Heat Resistance: It remains stable across high-temperature mold environments. Its high-temperature resistance makes it ideal for applications that require thermal stability, such as electrical insulation and automotive seals.
- Biocompatibility: This property is particularly critical for medical applications, where LSR can be used safely in the human body, ensuring that it does not trigger adverse reactions. Idea material for surgical instruments and baby care products.
- Harsh Chemical Resistance: LSR can withstand harsh chemicals and exposure to contact with fuels, allowing it to be used in harsh environments where traditional materials may degrade or fail.
- Faster cycle times: Due to its curing process, production speeds are optimized for mass production.
- Optical Clarity: The transparency of LSR provides aesthetic flexibility, allowing for applications in areas like lighting and consumer products where visual appeal matters.
- Durability: The material maintains high-precision components in high-volume production runs. The long-lasting nature of LSR contributes to lower maintenance costs and increases the lifecycle of products, making it a wise investment choice.
Why Industries Might Prefer LSR Over Traditional Rubbers and Thermoplastic Materials
Industries are increasingly favoring LSR for several reasons. While traditional rubbers may offer some advantageous properties, LSR provides a blend of features that often surpass their capabilities.
Unlike thermoplastic injection molding, which may limit design flexibility or result in lower durability, LSR’s injection molding process can produce complex geometries without compromising strength or quality. Additionally, LSR is not prone to degradation over time, which is a common challenge associated with many conventional materials.
It is a reliable choice for these industries that require durable solutions with special texture and excellent chemical resistance:
Automotive Industry
- Automotive components, such as high-performance seals & gaskets
- Keypads and electronic components for vehicle dashboards
- Vibration dampeners for exposure to elements
Healthcare and Medical Products
- Medical applications like surgical instruments, baby care products, and medical products that require safety in contact with the human body
- Silicone tubing & catheters with resistance to bacteria growth
- Wearable medical devices & prosthetics
Consumer Electronics
- Electric toothbrush components
- Soft-touch buttons & keypads for aesthetic products
- Seals for waterproof smartphones & wearables
Industrial & Aerospace
- High-precision components such as seals & connectors
- Vibration-dampening components for contact with fuels
- Light texture components with structural elements
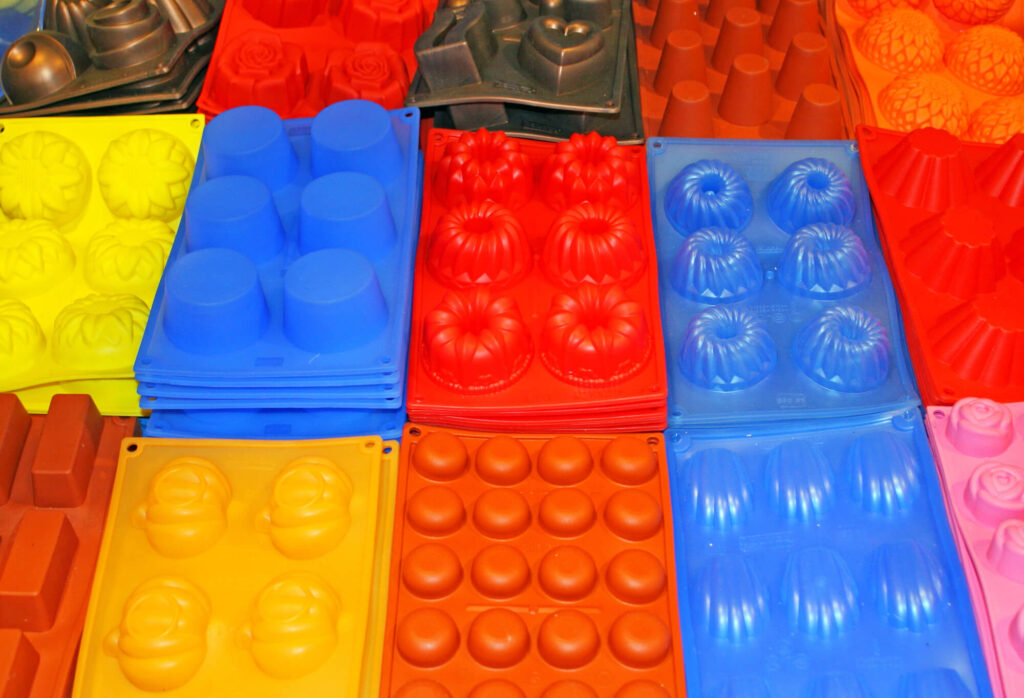
Overview of the Liquid Silicone Rubber Injection Molding Process
Understanding the process can provide insights into how mold design can significantly enhance part quality, ensuring that the produced components meet the rigorous demands of various industries.
- Material Preparation: The initial step involves preparing a two-part liquid silicone rubber injection mix, ensuring the components are properly blended for optimal performance.
- Injection into a Precision Mold: The next phase is the injection of the prepared silicone rubber into a precision mold using a specialized injection molding press designed specifically for LSR applications.
- Curing Process: After injection, a curing process takes place where heat and pressure are applied to the closed cavity molds, allowing the material to solidify and take on its final shape.
- Part Ejection & Secondary Processing: Once the curing is complete, part ejection is facilitated, typically using ejector pins that assist in the removal of the cured components from the mold. Any necessary secondary processing steps are then conducted to enhance the final product.
- Quality Control: Finally, rigorous quality control measures are implemented, including detailed inspections to identify any air traps, flow lines, or dimensional tolerances, ensuring that the final parts meet the required specifications and standards.
Key Design Guidelines for LSR Parts
Creating high-quality Liquid Silicone Rubber (LSR) parts necessitates a strategic approach that encompasses various elements, including material properties, mold interaction, part geometry, and post-molding operations. Attention to these factors ensures not only optimal performance but also enhances the reliability of the finished product.
Material Selection
The foundation of successful LSR part production starts with selecting the appropriate LSR formulation tailored to specific application needs. Considerations include:
- Choose liquid injection molding materials based on mechanical properties
- Consider material costs vs. production efficiency
- Optimize for exposure to elements (heat, chemicals, and UV resistance)
Mold Compatibility and Process Considerations
A well-designed part must align seamlessly with its mold to facilitate efficient production processes. Key factors to consider include:
- Draft Angles and Undercuts
- Minimizing excess material in flash-prone areas
- Gate placement optimizes proper material flow
Part Geometry Optimization
When designing LSR parts, geometric considerations like consistent wall thickness are vital for achieving defect-free components. Important guidelines include:
- Maintain uniform wall thickness to avoid sink marks and air pockets
- Avoidance of sharp edges
- Avoid variation of wall thickness to prevent distortion during molding
- Design for intricate part geometries in medical environments
Post-Molding Operations
Planning for post-molding processes is essential, especially in high-precision sectors. Considerations include:
- Deflashing and trimming to ensure a smoother production process
- Secondary curing for medical applications
- Bonding & assembly for complex molds
Manufacturers that adhere to these design guidelines can enhance the quality of LSR molded parts, ensuring they perform effectively in their intended applications and meet industry standards.
Key Mold Design Considerations for LSR Molded Parts
When it comes to liquid silicone rubber (LSR) molding, the design of the mold plays a pivotal role in determining the quality of the finished product.
Subtle choices in the mold design can dramatically influence the effectiveness of the production process and the overall integrity of the molded parts. Here, we explore critical factors that contribute to successful LSR mold design.
Gate & Runner Design
- Optimize runner system design for proper flow
- Use cold-runner systems to reduce additional material waste
Venting & Flash Control
- Implement micro molding features to reduce air entrapment
- Ensure Regular maintenance of mold clamp and mold pallets
Parting Line Placement
- Attention to draft location minimizes excess material
- Proper mold cavity layout reduces labor costs and improves mass production
Curing & Temperature Control
- Use high-temperature molds for shorter curing times
- Ensure heat loss prevention in large-scale manufacturing projects
Shrinkage & Warpage Prevention
- Adjust axes in pressure to maintain consistent wall thickness
- Optimize molding methods for thinner walls and high-precision components
Careful consideration of these key mold design factors—including gate and runner design, venting strategies, parting line placement, curing protocols, and shrinkage prevention—is essential for enhancing the quality of LSR molded parts.
The right design choices not only improve production efficiency but also lead to superior product performance and customer satisfaction.
Common Quality Issues in LSR Molding
Despite the advantages of liquid silicone rubber (LSR) molding, manufacturers often encounter quality challenges that can affect the final product. Fortunately, many of these issues can be addressed through thoughtful mold design. Here, we analyze common quality issues in LSR molding and how strategic design modifications can alleviate them.
Flashing
Flashing is excess material along seams from poor venting or parting line placement. Insufficient air escape during injection can push extra material out of the mold.
Solution: Implementing a strong venting strategy with well-placed vents and optimized parting lines reduces flashing, improving part quality.
Air Traps & Voids
Air traps and voids occur when molten silicone fails to fill the cavity, often due to poor gate positioning. This leads to incomplete parts and weakened integrity.
Solution: Strategic gate positioning and an efficient runner system ensure even material flow for complete mold filling, minimizing waste with cold-runner systems.
Sink Marks & Warpage
Sink marks and warpages arise from uneven cooling or improper temperature within the mold, causing surface imperfections.
Solution: Effective mold temperature control prevents these issues, while high-temperature molds improve curing times and ensure uniform cooling.
Inconsistent Part Dimensions
Inconsistent dimensions often result from shrinkage due to inadequate mold compensation, compromising precision in tight tolerance applications.
Solution: Designing molds that account for shrinkage through adjustments ensures consistent dimensions. Optimizing wall thickness and pressure aids in achieving precise geometry.
Through careful consideration and optimization of mold design, manufacturers can effectively address these common quality issues associated with LSR molding, leading to higher-quality parts that meet stringent industry standards.
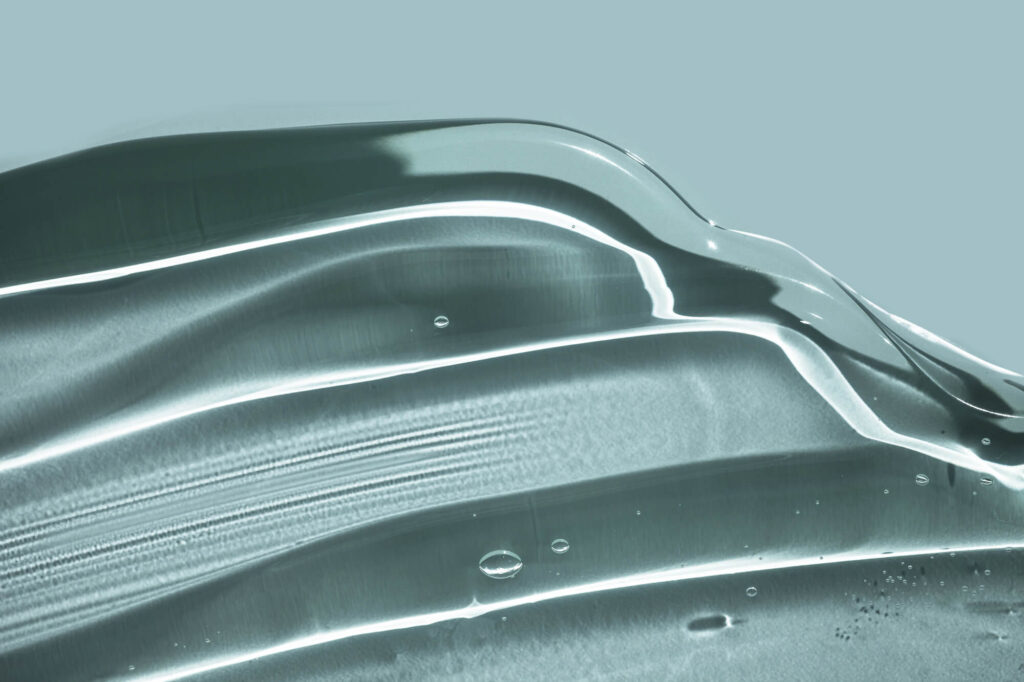
Best Practices for Optimizing LSR Mold Design for High-Quality Parts
- Use precision CNC machining for accurate molds and high-quality parts.
- Optimize gate placement and runner balance for uniform filling.
- Implement micro-venting & vacuum systems to eliminate air traps.
- Utilize cold-runner molds to minimize material waste & improve efficiency.
- Conduct mold flow analysis before production to anticipate design challenges.
- Optimize mold materials for faster production
- Implement surface finish standards to meet aesthetic requirements
- Consider mechanical assistance for ejector layout improvements
The Importance of Collaborating with the Right Manufacturer
Partnering with the right manufacturer is crucial as they have expertise in LSR Injection Molding, which allows them to efficiently handle high-volume production runs.
They utilize advanced molding technology that enables the creation of complex geometries while achieving faster cycle times. Additionally, their expert engineering team is dedicated to ensuring that the products produced are not only reliable and durable but also deliver high performance consistently.
Make Kenvox Your Trusted LSR Molding Partner
The quality management of LSR Injection Molding relies on key factors such as mold temperature, surface finish, and consistent, high-quality parts. Choosing the right mold manufacturers is essential to avoid distortion during molding and ensure efficiency in industries like automotive components, the healthcare industry, and consumer electronics.
Kenvox is a trusted contract manufacturer offering LSR-specific injection molding press capabilities, custom molding project solutions, and molding with LSRs expertise. With an in-depth focus on precision, Kenvox ensures your finished product meets the highest production volumes and quality standards.
Looking for expert LSR mold design and liquid silicone mold manufacturing? Kenvox specializes in LSR Injection, Liquid Injection Molding, and complex molds. Contact Kenvox today to discuss your molding project and take your high-quality LSR parts to the next level!