In manufacturing, selecting the right molding process can make all the difference in efficiency, cost, and product quality. Injection molding and compression molding are two of the most popular molding techniques, each with unique advantages and ideal applications.
Whether you’re creating compression-molded parts or intricate plastic injection molds, understanding the difference between compression molding and the injection molding process is essential for making an informed decision, particularly when it comes to which is optimal for high-volume production.
In this blog, we’ll dive into the details of both injection molding and compression molding, compare them across key factors, and help you determine which is best for your project.
What is Plastic Injection Molding?
Injection molding is one of the most widely used manufacturing methods for creating high-volume production runs of plastic materials and other components. Known for its ability to produce complex shapes with precision, injection molding is the go-to method for industries ranging from consumer products to aerospace components.
How the Injection Molding Process Works
The injection molding process involves several key steps to shape raw materials into finished products:
- Material Preparation: Raw plastic material, often in the form of resins, is melted in the heating barrel of an injection molding machine.
- Injection: The molten plastic is injected into a closed mold cavity using high pressure via specially designed gates.
- Cooling and Solidifying: As the material cools, it hardens to form the desired geometry or complex molds.
- Ejection: The finished product is removed from the mold using ejection pins.
This method allows for the efficient production of intricate components with exceptional consistency.
Advantages of Injection Molding
- Faster production cycles make it ideal for high-volume production.
- Creates detailed designs and complex shapes with minimal excess material.
- Works with a wide range of thermoplastic materials and thermoset materials.
- Cost-effective for large-scale production runs despite higher initial tooling costs.
Disadvantages of Injection Molding
- Requires significant upfront expenses for injection molds and tooling.
- Best suited for parts with consistent geometry and detailed designs.
What is Compression Molding?
Compression molding is another popular molding technique, often chosen for its simplicity and ability to work with specialized raw materials. It’s particularly useful for creating compression-molded parts, such as engine components or sheet molding compounds.
How the Compression Molding Process Works
The compression molding process is straightforward yet effective:
- A pre-measured amount of bulk molding compound or other material is placed in the mold.
- The mold cavity is heated, and hydraulic pressure is applied to shape the material into the desired form.
- The material hardens as it cools, creating the finished part, which is then ejected.
This process is especially suitable for simple shapes or large, thick components.
Advantages of Compression Molding
- Lower tooling costs compared to injection molds.
- Works well with composite materials and rubber injection molding.
- Efficient for creating larger, thicker compression-molded components.
- Produces minimal waste by efficiently utilizing raw materials.
Disadvantages of Compression Molding
- Slower cycle times compared to injection molding.
- Limited suitability for complex geometries or intricate designs.
- Not ideal for high-volume production runs due to its longer production time.
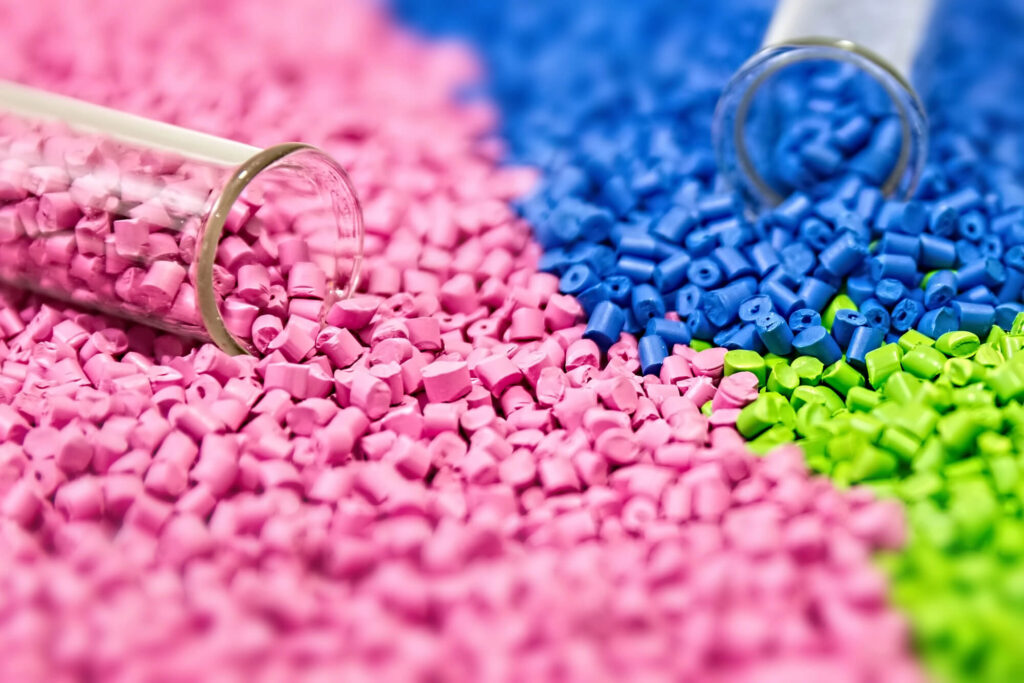
Key Comparisons Between Injection and Compression Molding
Choosing between injection molding and compression molding depends on several factors, including cost, materials, and production speed. Below, we’ll break down the molding methods across critical criteria.
1. Cost and Tooling
- Injection Molding: While the initial tooling costs are typically higher when it comes to injection molding, the unit prices tend to decrease significantly for large-scale production runs. This makes it more economical in the long run for products that require mass manufacturing.
- Compression Molding: On the other hand, compression molding has lower tooling costs upfront, making it a more budget-friendly option initially. However, for larger production volumes, the costs per unit can become more expensive compared to injection molding processes.
2. Materials and Resins
- Injection Molding: This method is compatible with an extensive variety of materials, including both thermoset injection molding materials and various types of plastic resins. Common materials used in injection molding include:
- Polypropylene (PP)
- Acrylonitrile Butadiene Styrene (ABS)
- Polycarbonate (PC)
- Nylon (PA)
- Polyethylene (PE)
- Thermoplastic elastomers (TPE)
- Compression Molding: This process excels when working with composite materials, as well as various forms of rubbers and bulk molding compounds. Typical materials used in compression molding include:
- Phenolic resins
- Rubber (natural and synthetic)
- Glass-reinforced plastics
- Thermoset polymers
- Silicone rubber
- Bulk molding compounds (BMC)
3. Shapes and Geometry
- Injection Molding: This method is particularly well-suited for creating intricate designs and components that feature complex geometries and detailed shapes, allowing for high precision and versatility in manufacturing.
- Compression Molding: In contrast, this technique is more effective for producing simpler shapes or components that have larger cross-sectional areas, making it ideal for parts that do not require intricate detailing.
4. Production Speed
- Injection Molding: This method boasts significantly shorter cycle times, which enhances its efficiency, making it an excellent choice for high-volume production runs where speed and consistency are crucial.
- Compression Molding: Conversely, compression molding operates at a slower pace, rendering it more suitable for medium-volume production or specialized parts that may not require the rapid throughput associated with high-volume manufacturing.
5. Environmental Considerations
- In the debate between compression molding vs injection molding when it comes to sustainability, both are designed with waste reduction in mind, effectively minimizing the amount of raw materials that go to waste during the manufacturing process. However, injection molding has the advantage of managing excess material more effectively, as it can be recycled and reused more proficiently than in compression molding.
- Additionally, injection molding tends to have lower energy consumption rates, making it a more sustainable and eco-friendly choice, especially for large-scale projects where efficiency is key to reducing the overall environmental impact.
Common Applications of Compression Molding vs Injection Molding
Understanding where each molding process excels can help manufacturers choose the right technique for their specific needs.
Injection Molding
Injection molding is widely used across various industries due to its ability to produce high-quality, precise parts at scale. Here are some key industries and examples of products produced through this method:
- Automotive Industry: Injection molding is employed to make components like dashboard panels, bumpers, and various interior parts due to its precision and ability to handle complex shapes.
- Consumer Goods: Many everyday items, such as containers, toys, and household appliances, are manufactured via injection molding, allowing for intricate designs and consistent quality.
- Medical Devices: Components such as syringes, surgical instruments, and medication delivery devices benefit from the high precision and customization capabilities of injection molding.
- Electronics: This industry uses injection molding for parts like housings, connectors, and switch buttons, capitalizing on the method’s detail and consistency.
Compression Molding
Compression molding is particularly suited to industries that require durable and robust parts, often from specific materials. Here are some significant industries and products relevant to compression molding:
- Automotive Industry: Similar to injection molding, compression molding is used for parts such as bumpers, gaskets, and interior components, particularly those made from rubber and composites, for improved strength.
- Aerospace: High-performance components, such as interior panels and parts made from composite materials, benefit from the lightweight yet robust properties provided by compression molding.
- Electrical Industry: Compression molding is utilized to make insulating parts and connectors, often using thermosetting plastics that enhance electrical resistance.
- Consumer Goods: Products like rubber mats, seals, and cookware often take advantage of the durability and cost-effectiveness offered by compression molding.
Which Molding Process Should You Choose?
Deciding between compression molding and injection molding comes down to your specific project needs. Consider the following:
- Cost and Budget: If you need lower upfront costs, compression molding may be preferable. However, for long-term cost-efficiency, injection molding is better for high-volume production.
- Material Requirements: Select injection molding for a broader range of materials; choose compression molding for specialized composite materials.
- Product Design: For complex molds and detailed parts, injection molding is the best fit. For simple designs, compression molding is more practical.