Silicone molding plays a critical role in modern manufacturing, providing high-performance materials for various industries, with one industry standing out for its unique requirements that only silicone molding offers. Its physical properties make it an ideal choice for applications requiring precision, durability, and chemical resistance.
This is why advanced silicone is the material of choice for a broad range of applications in the healthcare industry. Medical-grade silicone has the ability to withstand extreme temperatures, harsh chemicals, and frequent sterilization.
With advancements in silicone materials, medical device manufacturers can now produce highly specialized medical components with complex geometries to improve patient outcomes.
Here, learn about the latest advancements in silicone molding for healthcare applications, including its manufacturing process, production efficiency, and range of applications.
What Is Silicone Molding?
Silicone molding is a manufacturing process that uses silicone materials to produce medical components, electronic components, and consumer products with intricate geometries and enhanced properties.
Silicone is a synthetic polymer made up of silicon, oxygen, carbon, and hydrogen. It is engineered to create an ideal material for many specialized industries and applications because it exhibits remarkable thermal and chemical resilience, setting it apart from traditional rubber.
Advanced silicones are known for their performance across a vast temperature range (from -100°F to +500°F). They have a non-toxic composition, making them a suitable choice in medical technology.
Types of Silicone Molding
There are several types of advanced silicones on the market used for molding, with the two main ones being liquid silicon rubber and solid silicon rubber. Both have high resistance to extreme conditions and harsh chemicals, but their applications vary because of the nature of their molding process and different limits.
Liquid Silicone Rubber (LSR) Molding
LSR molding is a widely used medical molding technique that involves injecting liquid silicone rubber into a heated mold cavity.
This specific type of silicone allows it to be injected into molds for precise shapes and designs. Unlike solid silicone rubber, LSR is processed at a high range of temperatures and can be molded easily into complex forms, offering exceptional performance characteristics.
- Key Benefits of Liquid Silicone Molding:
- High biocompatibility of silicone rubber
- Exceptional resistance to high-temperature conditions
- Precision for medical device manufacturing
- Cost-effective mass production for high-volume production runs
- Common Applications:
- Medical implants, such as breast implants and heart valve components
- Wearable technology, including heart rate sensors
- Drug delivery devices
Solid Silicone Rubber (SSR) Molding
Unlike LSR, SSR molding uses solid silicone rubber, which is heat-cured in a mold.
- Key Benefits:
- Enhanced mechanical properties for demanding applications
- Temperature resistance and improved heat resistance
- Durability under mechanical stress
- Common Applications:
- Dental devices
- Surgical grips and flexible components for medical procedures.
Other Silicone Molding Methods
- Compression Molding: Best for high-performance silicones
- Injection Molding: Ideal for high-volume production runs
- Transfer Molding: Used for detailed components with exceptional properties
How Silicone Molding Works
Silicone molding utilizes a highly efficient and cost-effective methodology, which is instrumental in guaranteeing consistent quality control throughout the medical manufacturing industry.
Important Steps in the Silicone Molding Production Process
- Preparation of Raw Materials: This step involves gathering and preparing the necessary raw materials that will be utilized in the molding process.
- Designing the Mold Cavity: Careful design of the mold cavity is essential to create intricate geometries that meet specific requirements.
- Utilization of Injection Machines: High-capacity injection machines are employed to facilitate mass production, ensuring a quick and efficient process.
- Curing Process Over Extended Periods: The molds go through a curing process that lasts for extended periods to achieve optimal performance and properties.
- Computerized Quality Control Systems: Advanced computerized systems are implemented to monitor the process, thereby significantly reducing the chances of human error and enhancing precision.
Key Benefits of Silicone Molding in the Medical Industry
Silicone molding has gained significant traction and remains a popular choice in the medical industry, primarily due to its exceptional and advantageous properties, which include the following:
- Biocompatibility – Silicone’s unique material properties ensure it is safe for direct contact with human tissue, making it suitable for a wide range of medical applications.
- Chemical Resistance – This material can withstand harsh conditions and exposure to a variety of chemicals, maintaining its integrity even in challenging environments.
- Durability – Silicone components offer long-lasting performance, ensuring that medical equipment remains reliable and functional over extended periods, reducing the need for frequent replacements.
- Precision – Silicone molding enables the production of intricate and detailed components, enhancing medical device functionality designed for various medical device applications.
- Scalability – The silicone molding process is highly effective for high-volume production, allowing manufacturers to efficiently produce large quantities of medical devices without compromising quality.
In addition to its significant advantages in the manufacturing of medical device components for the medical device industry, medical silicone molding presents a variety of benefits that extend to the broader healthcare sector as well.
- Regulatory Requirements: It ensures compliance with critical standards set by regulatory bodies such as the FDA and ISO 10993, which are essential for safety and efficacy.
- Innovative Applications: Medical silicone molding finds applications in an array of cutting-edge diagnostic tools, sophisticated surgical instruments, and life-saving medical implants.
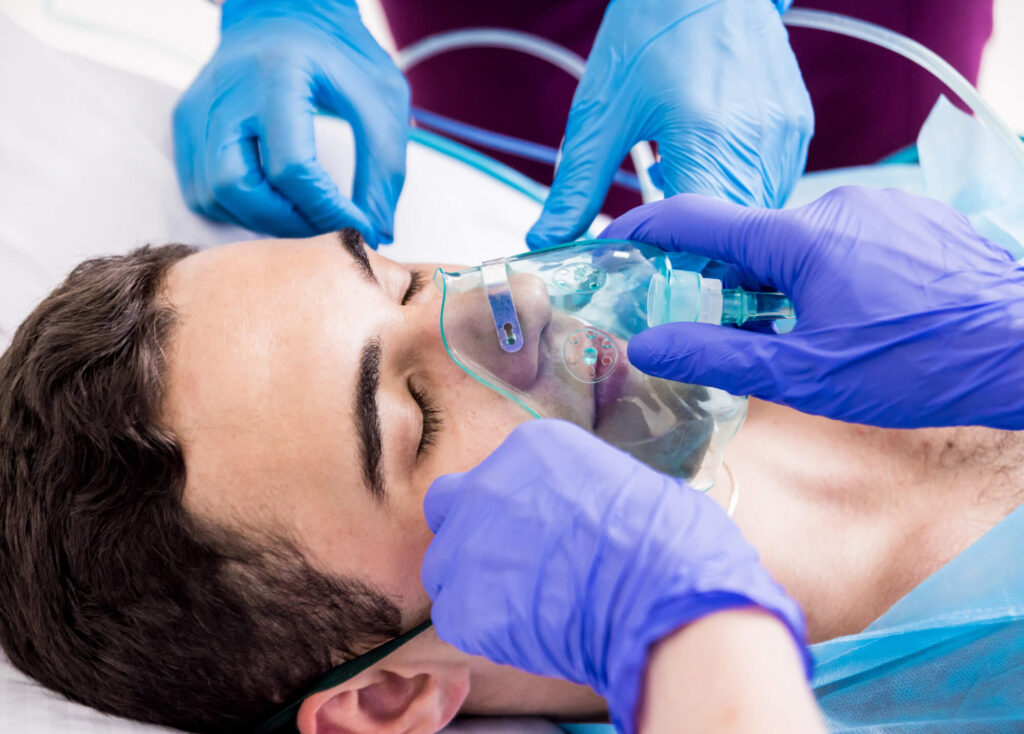
Examples of Silicone Molding in Various Healthcare Products
Medical Implants
- Breast Implants
- Heart Valve Components
- Artificial Joints
Surgical Tools & Instruments
- Scalpel Grips and Handles
- Medical-Grade Silicone Tubing
Wearable Medical Devices
- Heart Rate Sensors
- Continuous Glucose Monitors
Respiratory Devices
- CPAP Masks
- Oxygen Delivery Systems
Catheters & Tubing
- Drug Delivery Systems
- IV Components
Prosthetics & Orthotics
- Custom Prosthetic Liners
- Silicone Orthopedic Supports
Wound Care & Bandages
- Soft, Flexible Silicone Adhesives
- Advanced Wound Dressings
By leveraging the versatile properties of silicone, these healthcare applications enhance functionality and safety, significantly benefiting both providers and patients alike.
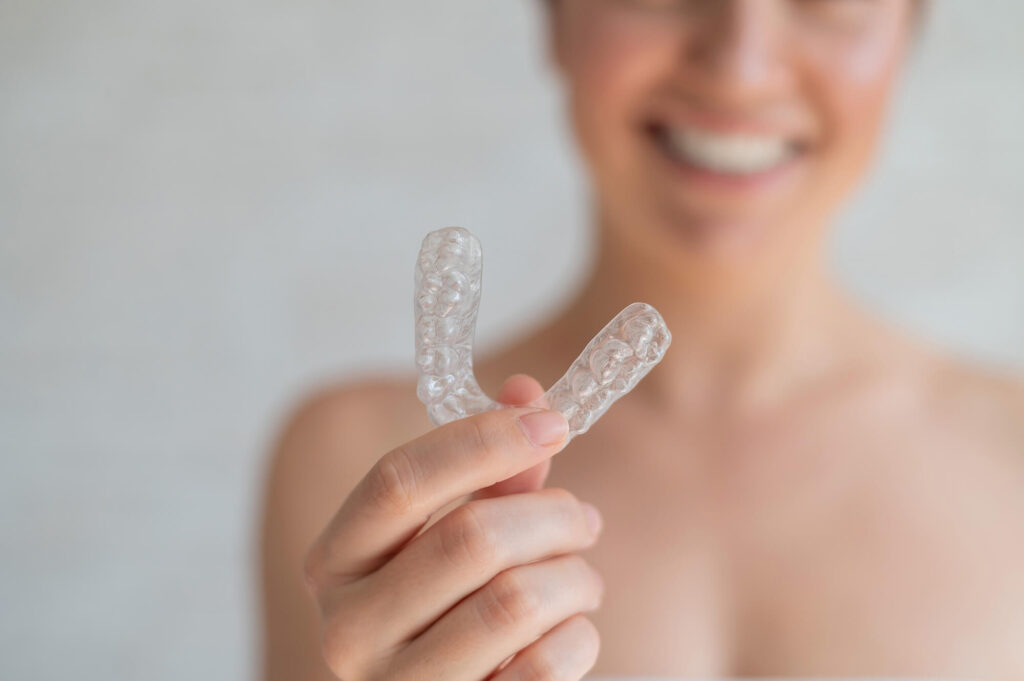
Other Industries Benefiting from Silicone Molding
- Automotive Industry – Silicone molding is utilized to create various essential components like seals, gaskets, and vibration-dampening parts, which are crucial for enhancing vehicle functionality and safety.
- Electronics Industry – In the realm of electronics, silicone molding is vital for producing protective coatings that shield delicate components from moisture and dust, ensuring reliability and longevity.
- Aerospace Industry – The aerospace sector relies on high-performance silicone materials that exhibit exceptional resistance to harsh chemicals and extreme environmental conditions, crucial for safe and efficient operations.
- Consumer Products – Silicone molding is an important process in developing consumer goods, including baby products and wearable devices, where safety, durability, and ease of use are paramount.
Emerging Trends in Medical Silicone Molding
The landscape of silicone molding in the healthcare industry is evolving rapidly, driven by innovations aimed at enhancing performance and sustainability. Below are key trends shaping the future of medical silicone molding:
- Bio-based Silicones: The development of eco-friendly silicone materials supports sustainability in manufacturing processes and reduces the environmental impact of production.
- Micro-Molding Techniques: Advances in micro-molding technology are facilitating the creation of small-scale medical devices, addressing the growing demand for compact and efficient healthcare solutions.
- Enhanced Heat Resistance: New formulations of silicone rubber exhibit improved heat resistance, including heat-conductive variants designed to perform safely under extreme conditions.
- Smart Materials with Integrated Sensors: The advent of smart silicone materials embedded with sensors paves the way for predictive maintenance, allowing for proactive monitoring of medical device performance and enhancing patient safety.
The Healthcare Industry Can Rely on Kenvox Manufacturing for Any Silicone Molding Needs
The healthcare industry depends on medical silicone molding to manufacture high-performance materials that improve patient outcomes. With advancements in silicone molding, medical device manufacturers can develop detailed components for implantable devices, drug delivery systems, and diagnostic equipment.
If you’re looking for a reliable contract manufacturing partner, Kenvox Manufacturing specializes in liquid silicone rubber (LSR) molding, solid silicone rubber (SSR) molding, and plastic injection molding. With advanced molding techniques, computerized quality control systems, and high-performance silicones, Kenvox ensures exceptional resistance in manufacturing medical devices.
Contact Kenvox today to discuss your custom silicone product needs and benefit from their cutting-edge silicone mold technology!