Material selection is a critical step in industrial molding and manufacturing. The properties of the material directly impact the product’s performance, durability, and application suitability. Among the most popular materials used in molding are rubber, silicone, and Liquid Silicone Rubber (LSR). While these materials share some similarities, they also have distinct characteristics that make them suitable for different applications.
Kenvox specializes in Liquid Silicone Rubber (LSR) molding and other manufacturing services, making them a trusted partner for industries that demand high-quality and precision-molded components. This blog explores the key differences between rubber, silicone, and LSR, highlighting their properties, applications, and manufacturing processes.
Defining the Materials
Understanding the foundational materials used in molding is essential for making informed decisions in manufacturing. Below, we delve into the characteristics of rubber, silicone, and Liquid Silicone Rubber (LSR), each of which serves distinct purposes in various industrial applications.
Rubber
Rubber, a versatile material, comes in two primary forms: natural and synthetic.
- Natural Rubber: Harvested from rubber trees, natural rubber has a gummy consistency and excellent elasticity.
- Synthetic Rubber: Produced from petrochemical derivatives, synthetic rubber offers enhanced resistance to extreme temperatures, chemicals, and harsh conditions.
- General Properties: Rubber is known for its excellent elasticity, resilience, and durability. Chemical resistance to oils and gases. It maintains its shape under stress and returns to its original form when the stress is removed. These properties make it ideal for shock absorption, vibration damping, and sealing applications.
- Common Uses in Industrial Applications: Rubber is widely utilized in manufacturing tires, seals, gaskets, and belts, as well as consumer goods like baby products and personal hygiene products. It plays a crucial role in the automotive, aerospace, and construction industries, where its strength and flexibility under various conditions are paramount.
Silicone
Silicone is a synthetic polymer made up of silicon, oxygen, carbon, and hydrogen. It is engineered to create a material that exhibits remarkable thermal and chemical resilience, setting it apart from traditional rubber.
- Properties: Silicone is notable for its flexibility, heat resistance, and biocompatibility, which allows it to sustain performance across a vast temperature range (from -100°F to +500°F). Its non-toxic composition makes silicone a suitable choice for food and medical applications.
- Applications Across Industries: Silicone is commonly found in medical device components (e.g., implants, tubing), electrical applications, food and beverage industries (e.g., bakeware, cooking utensils), consumer products (electric toothbrushes and baby bottle nipples), and consumer products (e.g., sealants, adhesives). Its stability under various conditions allows for diverse and innovative applications.
Liquid Silicone Rubber (LSR)
Liquid Silicone Rubber (LSR) is a specific type of silicone that is in a liquid state, which allows it to be injected into molds for precise shapes and designs. Unlike solid silicone rubber, LSR is processed at high temperatures and can be easily molded into complex geometries, offering exceptional performance characteristics.
Unique Characteristics:
- One of the defining features of LSR is its flowability, enabling it to fill intricate mold cavities effortlessly.
- Additionally, LSR cures when exposed to heat, making it suitable for high-volume production where consistency and efficiency are critical.
- Its resistance to extreme temperatures and moisture makes it ideal for applications in harsh environments.
- Excellent tear strength and resistance to harsh chemicals
- Ideal for intricate products with precise details
- Biocompatibility suitable for direct contact with human tissue or bodily fluids
By clearly understanding the unique attributes of rubber, silicone, and LSR, manufacturers can strategically select the most appropriate material for their specific needs, thus enhancing product performance and efficiency. Definition as a subtype of silicone. Unique characteristics (flowable, heat-cured, etc.).
Characteristics of Liquid Silicone Rubber (LSR)
LSR stands out due to its unique combination of physical and mechanical properties:
- Heat Resistance: Performs well across a wide temperature range.
- Chemical Stability: Resistant to harsh chemicals and peroxide byproducts.
- Flexibility and Durability: Retains original shape even under stress.
- Biocompatibility: An excellent choice for medical device products and food-grade applications.
- Ease of Molding: The automated nature of injection molding processes allows for complex shapes and consistent quality.
- Low Compression Set: Ideal for industrial components that require dimensional stability.
Applications of Liquid Silicone Rubber (LSR)
LSR’s versatility makes it a popular material for critical applications in diverse industries:
- Medical Applications:
- Implantable silicone components
- Drug delivery devices
- Laryngeal masks
- Baby bottle nipples and medical-grade silicone tubes
- Automotive Industry:
- Engine mounts
- Seals and grommets
- Impact-resistant devices
- Consumer Products:
- Electric toothbrushes
- Wearable devices
- Personal hygiene products
- Electronics:
- Keyboards and protective components
Manufacturing Process for LSR
The manufacturing process for Liquid Silicone Rubber (LSR) molding involves several critical steps that enhance production efficiency and ensure product quality. This advanced method of molding has gained prominence due to its precise fabrication capabilities and ability to produce high-volume outputs with minimal waste.
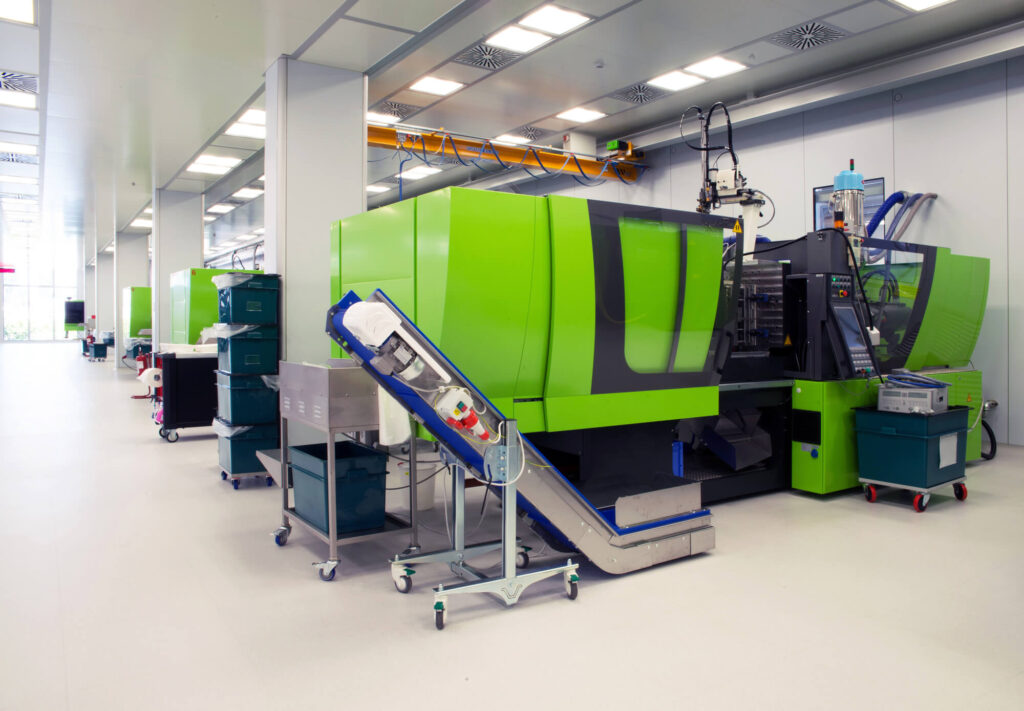
Overview of the Molding Process
LSR molding typically employs an injection molding machine, which is designed for high-volume production efficiency while ensuring precise product design and accurate dimensions. The steps in the LSR injection molding process are as follows:
- Material Injection: Raw materials are injected into a carefully prepared mold cavity, where they start their transformation into the desired product.
- Curing Process: The injected material undergoes a curing process facilitated by a platinum catalyst, which transforms the liquid silicone rubber into a solid form.
- Fully Automatic Production: Adopting a fully automatic production line ensures consistent output while significantly reducing labor costs. This automation supports high precision and minimizes the risk of human error.
Curing Process
The curing process is pivotal to achieving the desired properties of the final product and involves high temperatures and specific chemical solutions:
- Vulcanization: This occurs when the material is exposed to heat, promoting a chemical reaction that strengthens the silicone through cross-linking.
- Chemical Bonding: The chemical bonds formed during vulcanization ensure that the final product retains its shape and mechanical properties over an extended period, making LSR products highly durable and reliable for various applications.
As you can see, the LSR molding process is designed to maximize efficiency while producing a broad range of high-quality silicone products, thanks to its meticulous steps and advanced technology.
Solid Silicone Rubber (SSR)
Solid silicone rubber, also known as High Consistency Rubber (HCR), has unique characteristics that make it ideal for specific industrial applications. Understanding its properties and how it compares to other silicone types, particularly Liquid Silicone Rubber (LSR), can help businesses make informed decisions about their manufacturing processes.
Properties of SSR
Solid Silicone Rubber offers a dense, putty-like consistency that provides distinct advantages in various manufacturing environments. Here are some of its key properties:
- Heat and Chemical Resistance: HCR or SSR exhibits excellent resistance to extreme temperatures and harsh chemicals, making it an ideal choice for applications in challenging conditions.
- Durability: The inherent strength of SSR makes it ideal for producing durable parts that can withstand the demands of large-scale industrial use.
LSR vs. SSR
When comparing LSR and SSR, several differences emerge that influence their applications and processing methods:
- Ease of Processing: LSR utilizes automated injection molding techniques, enabling faster and more efficient production. Conversely, HCR requires a more labor-intensive compression molding process, which can lead to higher operational costs and longer production times.
- Applications: LSR is particularly well-suited for producing intricate and complex designs with shorter production cycles. HCR or SSR is often favored in robust, high-volume industrial applications where durability is paramount.
- Cost and Scalability: The automation of LSR molding translates into reduced labor costs and the ability to scale production rapidly, making LSR an attractive option for manufacturers looking to optimize their processes. In contrast, the manual nature of SSR production can limit scalability and increase expenses.
Understanding these differences will help businesses select the appropriate material and molding technique to fit their specific needs and ensure the success of their products.
Considerations for Material Selection
Selecting the right material involves evaluating several factors:
- Mechanical Properties: Tensile strength, elasticity, and tear resistance.
- Environmental Conditions: Resistance to bacteria growth, body fluids, and harsh chemicals.
- Production Requirements: Initial capital equipment costs, production volume, and labor costs.
- Application Needs: Medical-grade, food-grade, or high-temperature applications.
For precision manufacturing and challenging handling properties, LSR is often the material of choice.
Why Choose Kenvox for LSR Molding?
- Robust quality standards
- Design flexibility for complex shapes
- Cost-effective production efficiency
Contact us today for expert guidance and top-quality LSR molding solutions tailored to your needs.