Injection molding is a cornerstone of modern manufacturing, allowing businesses to create complex parts with precision and efficiency. However, with thousands of plastic materials on the market, each with its unique properties, the decision-making process can quickly become daunting. From thermoplastics to thermosetting plastics, understanding the characteristics and applications of each material is crucial to your project’s success.
Did you know that choosing the wrong material can significantly affect not only the quality of your product but also its cost and functionality?
Whether you’re designing components for automotive, consumer goods, or medical devices, selecting the right plastic material is the first step toward achieving your project goals. A well-informed choice can enhance mechanical strength, improve aesthetics, and even reduce production costs. In this guide, we’ll explore essential factors to consider and highlight key plastics to help you make an informed decision that aligns with your project requirements.
Get ready to demystify the injection molding material selection process and find the perfect material for your next project!
Injection Molding: Understanding It
Injection molding is a manufacturing process that involves melting plastic or other materials and injecting the molten substance into a mold cavity under high pressure. Once injected, the material cools and solidifies, taking the shape of the mold to form a three-dimensional component or product.
This technique is widely used across various industries due to its ability to produce complex shapes with high precision and efficiency.
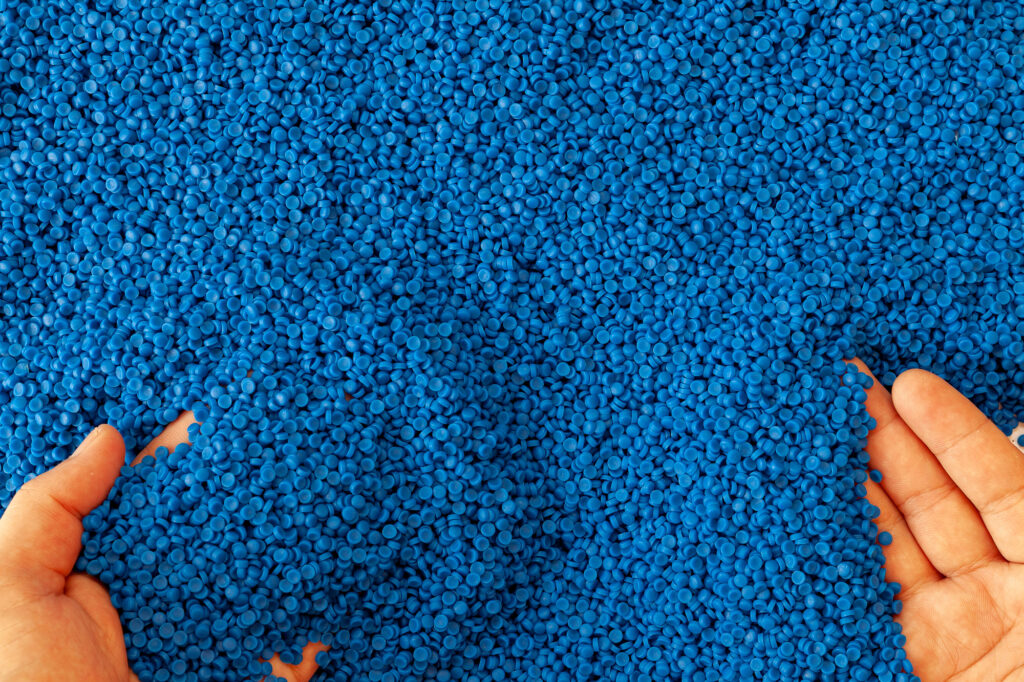
What Are Thermosets and Thermoplastics?
Plastics can be broadly classified into two categories in injection molding: thermosets and thermoplastics. While both are polymers, their structural behavior during heating and cooling sets them apart, determining their use cases, processing methods, and recyclability.
Thermosets: The Early Pioneer
Thermosetting plastics, or thermosets, are polymers that undergo an irreversible chemical reaction during curing, creating a rigid, crosslinked structure. Once set, these materials cannot be melted or reprocessed. This unique property provides excellent thermal stability, chemical resistance, and durability. However, their lack of recyclability and more complex molding processes have limited their use in modern manufacturing.
- Examples of Thermosets:
- Epoxy resins: Common in adhesives and coatings.
- Phenolics: Used in electrical insulators and heat-resistant parts.
- Polyurethane (when used as a thermoset): Found in foams and automotive components.
Historically, thermosets were used in automotive, electrical, and aerospace industries for parts requiring high durability and high heat resistance. However, as thermoplastic technologies advanced, thermosets’ share of the plastics market declined to about 15% of annual processed materials.
Thermoplastics: The Modern Standard
Thermoplastics are polymers that can be repeatedly melted and reshaped without undergoing chemical changes. This reversibility makes them highly versatile and suitable for a wide range of applications, from consumer goods to industrial components. Thermoplastics dominate the injection molding industry due to their ease of processing, recyclability, and wide variety of material options.
- Properties of Thermoplastics:
- Can be melted and reformed multiple times.
- Available in a broad range of strengths, flexibilities, and thermal resistances.
- Generally easier and faster to mold than thermosets.
- Recyclable, making them more environmentally sustainable.
Thermoplastics are used across industries, including automotive, electronics, medical devices, packaging, and consumer goods.
Why Focus on Thermoplastics in This Guide?
While thermosets were the first commercial polymers to gain widespread adoption, the advantages of thermoplastic materials have led to their dominance in the injection molding process.
Their recyclability, versatility, and compatibility with modern manufacturing processes make them the preferred choice for most injection molding projects today. For this reason, the majority of this guide (but not all of it) focuses on thermoplastics, which account for approximately 85% of all materials processed annually.
Key Plastic Material Properties and Attributes to Consider
Choosing the right plastic for injection molding is crucial because it directly influences the properties of the final product, including its strength, flexibility, durability, and overall functionality.
The characteristics of different plastics, such as melting points, shrink rates, and environmental compatibility, can affect the manufacturing process and the product’s performance in its intended application.
A well-informed material selection ensures not only the quality and reliability of the product but also its cost-effectiveness and compliance with industry standards.
Tensile Strength
You’ll need to contemplate the tensile strength of plastic when choosing materials for injection molding.
Tensile strength determines how much stress your product can withstand without stretching or breaking.
For example, nylon is renowned for its high tensile strength and dimensional stability, making it ideal for parts requiring precision and durability.
Impact Resistance
You’ll want a material that absorbs shocks without breaking. Seek out plastics with high impact strength or resistance as part of the material’s broader mechanical strength.
Impact strength guarantees your product can withstand rough use and exposure to chemicals, giving you control over its durability and functionality.
One commonly used method to measure the impact resistance of materials is the Notched Izod test. This standardized test evaluates how a material behaves when subjected to a sudden force, simulating real-world impacts. During the test, a notched specimen of the material is struck by a swinging pendulum, and the energy absorbed in breaking the material is measured. A higher energy absorption indicates greater impact resistance, making it an essential factor to consider when selecting materials for applications where durability and resilience are vital.
By choosing a plastic that performs well in the Notched Izod test, you can ensure that your molded parts will perform reliably in challenging environments.
Heat Resistance
While considering impact resistance is important, don’t overlook the heat resistance of your chosen plastic for injection molding.
Heat or temperature resistance is a plastic’s ability to withstand wide temperature ranges without melting, warping, or losing its mechanical integrity. These thermal properties are crucial for products exposed to extreme temperatures and high heat, such as automotive engine components or cooking utensils.
Key metrics include:
- Heat Deflection Temperature (HDT): The temperature at which a material begins to deform under a specified load.
- Glass Transition Temperature (Tg): The temperature where the plastic transitions from rigid to rubbery.
Materials like Polyetheretherketone (PEEK) or Polycarbonate are ideal for elevated-temperature applications. On the other hand, plastics like Polystyrene may not fare well in environments with fluctuating or high temperatures.
Flexural Strength (Flexural Modulus)
Flexural strength, or flexural modulus, determines how well the material resists bending under load. Ideal for automotive components, plastics with high flexural strength maintain their integrity under stress.
You’ll want to choose materials that offer superior resistance, ensuring durability and performance in demanding applications.
Chemical Resistance
For products that will come into contact with chemicals—such as cleaning agents, oils, or solvents—the chemical resistance of the material is paramount. Plastics like polypropylene (PP) and polyethylene (PE) are excellent choices because of their resistance to acid and other chemicals.
However, some plastics, like ABS, may degrade or discolor when exposed to certain chemicals. Evaluating the chemical environment in which the product will operate ensures longevity and performance.
Shrink Rate
The shrink or shrinkage rate of a plastic material used in injection molding refers to the amount by which a molded part decreases in size as it cools and solidifies, typically expressed in inches per inch (e.g., 0.014″ – 0.023″ per inch for nylon).
This parameter is critical in the material selection process, as it directly influences the final dimensions and tolerances of the product. A higher shrink rate can lead to challenges such as dimensional inaccuracies, potential warping, and difficulties in assembly, particularly when tight tolerances are required. Therefore, when choosing a plastic material for a product, it is essential to consider the shrinkage rate in conjunction with the design specifications, the required performance characteristics, and the intended application.
Selecting a material with a suitable shrink rate can help mitigate issues related to dimensional stability and ensure the final product meets the desired quality and functionality.
Electrical Insulation Properties
Many applications, especially in the electronics and electrical industries, require materials that can effectively insulate against electrical currents to prevent short circuits or electrical failures.
Plastics, such as epoxy and certain grades of polycarbonate, offer varying degrees of electrical insulation, making them suitable for use in components like circuit boards, connectors, and housing for electrical devices. The ability of a plastic to resist electrical conductivity not only protects sensitive electronic parts but also enhances the longevity and reliability of the product in diverse environmental conditions. Therefore, selecting a plastic with the appropriate electrical properties is essential to ensure optimal functionality, compliance with industry standards, and the safety of both the device and its users.
Melt Flow Rate
It’s also important to look at melt flow rate, another key property in choosing the right plastic for the injection molding process.
The melt flow rate determines how easily the molten material flows in the mold. ABS and nylon vary in this aspect; ABS typically has a higher melt flow rate, offering you more control in processing and finer detail in your final product.
Material Cost
Different plastics vary widely in price, impacting your production budget.
You’ll want to balance cost with performance.
Assess how material cost influences your overall expenses without compromising quality.
Prioritizing this allows you to manage your resources effectively, ensuring that you remain in control of both production costs and final product quality.
Manufacturing Process and Cost
When choosing the right plastic for injection molding, it’s crucial to take into account how different materials behave during the manufacturing process.
Consider the rate at which each material flows, as this impacts your production cost and speed.
Materials used for electrical components may require specific properties as well, further affecting the production process.
Opt for a plastic that aligns with your production process to control both quality and expenses effectively.
FDA and Regulatory Requirements
Considering FDA and other regulatory requirements is essential for your material choice.
You’ll need to guarantee the plastics comply with specific standards relevant to your product’s application.
Don’t overlook this step; it’s vital for market success and legal compliance, especially if your product has food and medical applications.
Familiarize yourself with these regulations to maintain control over your project’s outcome and avoid future complications.
Environmental Impact
Evaluating the environmental impact of different plastic materials has increasingly become crucial in the injection molding material selection process.
Consider the properties of each plastic and its sustainability profiles. You’ll find that some plastics have lower environmental impacts due to recyclability or less energy-intensive production processes.
Choose wisely, control your project’s footprint, and align your choices with your environmental values.
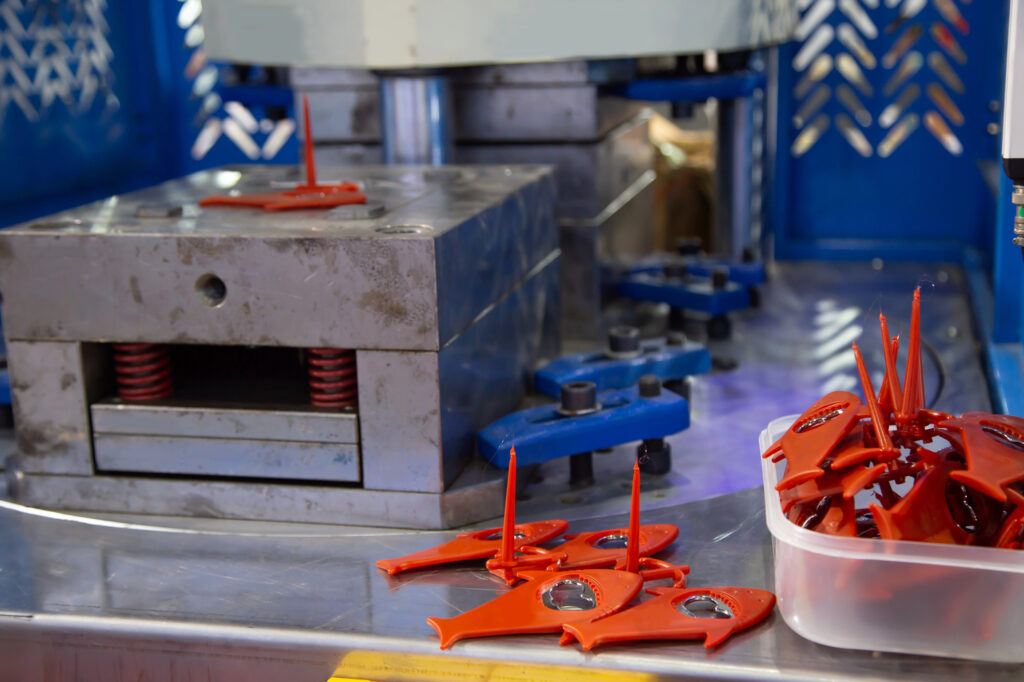
The Most Common Injection Molding Materials
Choosing the right material for injection molding is vital for project success. Different plastics provide unique properties suited for various injection molding applications. This section will highlight key injection molding materials, detailing their characteristics, benefits, and typical uses.
Understanding these options is essential for designing consumer products, automotive components, or medical devices, ensuring you achieve optimal performance and quality.
Acrylic (PMMA)
Acrylic, known by trade names like Plexiglas and Lucite, is a lightweight, transparent thermoplastic often used as a shatter-resistant alternative to glass. It is valued for its clarity and aesthetic versatility, making it ideal for applications requiring transparency and weather resistance.
- Advantages:
- Exceptional optical properties and clarity, with up to 92% light transmission.
- Lightweight, with half the density of glass.
- Excellent resistance to weathering and UV radiation, suitable for outdoor use.
- Easy to shape, mold, and polish for aesthetic applications.
- Disadvantages:
- Brittle and prone to cracking under stress compared to other transparent plastics like polycarbonate.
- Poor impact resistance in certain conditions.
- Limited heat resistance, softening at lower temperatures.
- Applications: Display cases, skylights, signage, aquariums, and lenses.
ABS (Acrylonitrile Butadiene Styrene)
ABS, or Acrylonitrile Butadiene Styrene, is a widely used thermoplastic known for its excellent combination of toughness, strength, and ease of processing. Its versatility makes it suitable for a broad range of applications, especially in consumer and industrial products.
- Advantages:
- High impact resistance and toughness.
- Easy to mold, with a low melting point for efficient processing.
- Excellent dimensional stability and resistance to wear.
- Accepts finishes like painting or plating for aesthetic purposes.
- Disadvantages:
- Poor resistance to UV light and weathering; prone to discoloration when exposed to sunlight.
- Limited resistance to solvents and high temperatures.
- Applications: Interior parts in the automotive industry, consumer electronic housings, and electronic components, toys like LEGO bricks, and household appliances.
Nylon (Polyamide)
Nylon, or polyamide, is a durable and versatile plastic commonly used in mechanical and industrial applications. It comes in multiple grades, such as PA6 and PA66, each offering unique benefits.
- Advantages:
- Excellent strength and wear resistance.
- High flexibility and elasticity, with the ability to withstand repeated stress.
- Good resistance to chemicals, oils, and greases.
- Can be reinforced with glass fibers to enhance mechanical properties.
- Disadvantages:
- Absorbs moisture from the environment, leading to dimensional changes and reduced strength.
- Requires drying before molding for optimal performance.
- Applications: Gears, bearings, bushings, industrial components, and textile fibers.
Polypropylene (PP)
Polypropylene is a lightweight, economical, and versatile plastic used in a wide variety of applications. It is particularly valued for its resistance to moisture, fatigue, and chemicals.
- Advantages:
- Exceptional chemical and moisture resistance.
- High fatigue resistance, ideal for applications like living hinges.
- Lightweight and moldable with excellent flexibility.
- Recyclable, making it a sustainable choice.
- Disadvantages:
- Poor resistance to UV light unless treated with stabilizers.
- It can become brittle at low temperatures.
- Applications: Food packaging and containers, automotive components, medical equipment and devices, and outdoor furniture.
Polycarbonate (PC)
Polycarbonate is a high-performance plastic valued for its exceptional strength, transparency, and impact resistance. It is often used in demanding environments where durability and clarity are required.
- Advantages:
- Excellent impact resistance, nearly shatterproof.
- Good heat resistance and flame retardancy.
- Excellent optical clarity, ideal for transparent components.
- Lightweight yet strong, making it a practical alternative to glass.
- Disadvantages:
- Prone to scratching unless treated with a protective coating.
- It can turn yellow over time with prolonged UV exposure unless stabilized.
- Relatively high cost compared to other general-purpose plastics.
- Applications: Safety goggles, bulletproof glass, electronic displays, and protective equipment.
Polyethylene (PE)
Polyethylene is one of the most commonly used plastics globally, available in multiple densities like Low-Density Polyethylene (LDPE), High-Density Polyethylene (HDPE), and Ultra-High-Molecular-Weight Polyethylene (UHMWPE). Its properties make it suitable for a wide range of applications.
- Advantages:
- Excellent moisture resistance and toughness.
- Chemically inert and safe for food contact.
- Lightweight and flexible, with good impact resistance.
- Disadvantages:
- Limited resistance to high temperatures; can deform under heat.
- Poor adhesion to paints and coatings without surface treatment.
- Applications: Plastic bags, water pipes, containers, and cable insulation.
Polystyrene (PS)
Polystyrene is a rigid, economical plastic often used for disposable or single-use products. It is available in two main forms: General Purpose Polystyrene (GPPS) and High Impact Polystyrene (HIPS).
- Advantages:
- Easy to process and mold into intricate shapes.
- Inexpensive and widely available.
- Can be made transparent or opaque, offering aesthetic flexibility.
- Disadvantages:
- Brittle and prone to cracking, especially in its general-purpose form.
- Poor heat resistance and flammability unless treated.
- Applications: Disposable cutlery, packaging materials, foam insulation, and CD cases.
Thermoplastic Polyurethane (TPU)
TPU is a flexible and highly durable material with excellent abrasion resistance and elasticity. It is often used in products requiring long-term durability or when polyvinyl chloride (PVC) might cause adverse reactions, especially in medical applications.
- Advantages:
- Highly elastic and flexible.
- Resistant to wear, oils, and greases.
- Available in a range of hardness levels to suit different applications.
- Disadvantages:
- Sensitive to UV light and moisture unless treated, making it unsuitable for outdoor applications.
- Higher cost compared to general-purpose plastics.
- Applications: Flexible hoses, phone cases, gaskets, and footwear.
Thermoplastic Elastomer (TPE)
Thermoplastic Elastomer (TPE) is actually a class of polymers that combines the elasticity of rubber with the processability of thermoplastics. It is available in various grades and types, such as Styrenic Block Copolymers (TPE-S), Thermoplastic Polyurethanes (TPU), and Thermoplastic Vulcanizates (TPV). Its flexibility and durability make it a popular choice in diverse industries.
- Advantages:
- Highly flexible and elastic, mimicking the properties of rubber.
- Resistant to wear, fatigue, and environmental factors like UV radiation.
- Wide range of hardness levels and excellent grip properties.
- Recyclable and easy to process compared to traditional rubber.
- Disadvantages:
- Typically, it has lower chemical and heat resistance compared to rigid thermoplastics.
- Some grades may have limited strength and durability for heavy-duty applications.
- Applications: Grips for tools and electronics, medical tubing, automotive seals, footwear soles, and soft-touch handles.
PEEK (Polyetheretherketone)
PEEK is a high-performance plastic with exceptional strength, thermal stability, and high chemical resistance. It is commonly used in extreme environments.
- Advantages:
- Outstanding mechanical and thermal properties.
- Resistant to harsh chemicals and high temperatures.
- Suitable for highly demanding applications in aerospace, automotive, and medical fields.
- Disadvantages:
- Extremely high cost compared to other plastics.
- Requires specialized processing equipment.
- Applications: Aerospace components, medical implants, and high-performance industrial parts.
Polyoxymethylene (POM)
Polyoxymethylene (POM), also known as Acetal or Delrin (a brand name), is an engineering thermoplastic widely used for precision components requiring high stiffness, low friction, and good dimensional stability. It is available in two main types: Homopolymer (better mechanical properties) and Copolymer (better chemical resistance).
- Advantages:
- Excellent strength, stiffness, and wear resistance.
- Low friction, making it ideal for moving parts.
- Good resistance to chemicals, oils, and solvents.
- Dimensional stability for high-precision applications.
- Disadvantages:
- Limited resistance to UV light and high temperatures.
- Prone to shrinkage during molding, requiring careful mold design.
- Applications: Gears, bearings, zippers, conveyor belts, under-the-hood components, and plumbing fixtures.
Fillers and Additives
Fillers and additives are elements that are added to all these plastic materials to achieve the desired characteristics and properties if the materials themselves don’t quite comply with your needs.
These substances can improve mechanical strength, flexibility, thermal stability, and various other characteristics that the base material may not provide sufficiently on its own. Here’s a closer look at some common fillers and additives used in injection molding.
Glass Fibers
Glass fibers are a widely used filler in thermoplastics, providing an excellent strength-to-weight ratio. When incorporated into plastics, they can dramatically improve the material’s rigidity and dimensional stability.
- Advantages:
- Increased tensile strength and stiffness.
- Improved heat resistance, making it suitable for applications that require thermal stability.
- Enhanced impact resistance.
- Disadvantages:
- Can make the material more brittle if overused.
- Processing can be challenging due to the abrasiveness of glass fibers, requiring specialized equipment.
- Applications: Automotive parts, electrical enclosures, and structural components.
Carbon Fibers
Carbon fibers are known for their remarkable strength and lightweight characteristics, making them a popular choice for high-performance applications. When added to plastics, they can create composites that exhibit superior mechanical properties.
- Advantages:
- Excellent strength-to-weight ratio for enhanced performance in demanding applications.
- Good fatigue resistance and thermal stability.
- Enhanced conductivity properties when appropriate grades are used (making them suitable for electronic applications).
- Disadvantages:
- High cost compared to other fillers.
- More challenging processing and requires advanced molding techniques.
- Applications: Aerospace components, sporting goods, automotive applications, and high-performance industrial parts.
Talc
Talc is a naturally occurring mineral that serves as a filler in various plastic formulations, particularly polypropylene. Its unique properties make it an appealing option for improving the performance of molded parts.
- Advantages:
- Provides improved rigidity and dimensional stability, especially in high-temperature environments.
- Reduces the overall cost of the material without significantly compromising mechanical properties.
- It can enhance surface smoothness and aesthetics.
- Disadvantages:
- It can affect the clarity of clear plastics.
- Overuse can lead to reduced impact resistance and toughness.
- Applications: Household products, automotive interior components, and packaging.
Additives
In addition to fillers, various additives can be used in injection molding to enhance specific properties or functions of the base material. Some common types of additives include:
- Stabilizers: Protect against degradation from heat and UV light.
- Flame Retardants: Reduce flammability and enhance safety in applications prone to fire hazards.
- Colorants: Add visual appeal and branding options by providing a range of colors.
- Plasticizers: Improve flexibility and processing characteristics, making the material easier to mold.
- Advantages:
- Tailoring material properties to meet specific application needs.
- Enhancing performance and longevity.
- Disadvantages:
- This may increase processing complexity and cost.
- Certain additives can negatively impact recyclability.
- Applications: Widely used across various industries, including automotive, consumer goods, medical devices, and electronics
Understanding the role of fillers and additives is crucial when choosing materials for injection molding. By selecting the right combinations, manufacturers can achieve desired performance traits while optimizing costs and processing efficiencies.
Steps in the Injection Molding Material Selection Process
It might be tempting to just look at a table or list of data for the materials, but take some time to read these basic steps for deciding the best material for your injection molding application:
Define Application Needs and Requirements
Before selecting a material for your injection molding project, assess your product’s functional requirements and operational conditions.
You’ll need to clearly define what your product must withstand—be it high temperatures, chemical exposure, or mechanical stress.
Consider the product’s end use, whether it’ll be indoors, outdoors, or in abrasive environments.
This step guarantees you’re in control, paving the way for informed, strategic decisions.
Evaluate Material Properties and Compare
Having defined your application needs and requirements, it’s important to closely evaluate various material properties and compare them to ascertain the best match for your project.
Consider factors like tensile strength, impact resistance, and thermal stability.
You’ll need to weigh up cost-effectiveness against performance criteria to make sure you’re making an informed decision that aligns with your project’s specific demands.
Choose wisely to control outcomes.
Consult with Injection Molding Experts and Material Suppliers
Your next vital step is to consult with injection molding experts and material suppliers.
Engage them to dissect the nuances of each material’s performance under your specific conditions. Their insights can guide you in honing in on the best choice, ensuring your project’s success while maintaining control over the production quality and cost-effectiveness.
Use Prototyping with Materials on the Shortlist
Once you’ve narrowed down your options, it’s essential to prototype with the materials on your shortlist.
This step lets you see how each material behaves under real-world conditions. You’ll witness firsthand their strengths and weaknesses, ensuring you make an informed decision.
Don’t skip this; what works on paper doesn’t always pan out in practice. Control your project’s outcome by testing thoroughly.
Kenvox Ensures Your Material Selection is the Best for Your Injection Molding Needs
Kenvox takes the guesswork out of selecting injection molding materials for your projects.
They’ll analyze your product’s requirements, ensuring you choose the ideal plastic to meet your needs.
Whether it’s durability from ABS, clarity from polycarbonate, or strength from nylon, Kenvox empowers you to make informed decisions, optimizing your product’s performance and cost-efficiency.
Trust their expertise to guide you right every time.