Silicone is a vital material in manufacturing, with its ability to be as flexible or rigid as needed being a key reason. Just how soft or rigid is measured using a durometer, and its hardness is more than just a technical specification — it’s a critical design decision.
The durometer scale, most commonly the Shore hardness scale, measures a material’s resistance to indentation and plays a pivotal role in how silicone parts perform in real-world applications.
But selecting the right Shore durometer rating isn’t just about looking up numbers on a chart. It involves understanding the measurement standard, the environmental factors, and the interaction between the material characteristics and the application environment.
Read on and learn how silicone durometer selection impacts the durability of silicone, its mechanical properties, and its ability to function under a broad range of conditions.
Whether you’re designing for mouse pads, gasket materials, or temperature silicone rubber sheets, the right durometer reading can mean the difference between a reliable product and one that fails prematurely.
What Is Durometer? Understanding the Basics
Durometer is a standardized method of measuring the hardness of materials, including silicone rubbers. It quantifies how resistant a material is to physical indentation when force is applied. The most common scale used for silicones is the Shore A scale, although Shore 00 and Shore D are also used for very soft or very hard materials, respectively.
Albert F. Shore developed the Shore hardness scale, and today it serves as a critical reference for engineers and material scientists for measuring the hardness of elastomers. Within this system, durometer values range from 0 to 100, where lower numbers represent soft materials and higher numbers represent hard, less flexible materials. For instance, rubber bands are often rated around Shore A 20, whereas pencil erasers may fall closer to Shore A 60.
The Shore A scale is the most appropriate for hardness measurements of general-purpose silicone products, including silicone rubber sheets, gaskets, and molded seals. For very soft materials, such as gel-like silicones or latex rubber tubing, Shore 00 may be used. For semi-rigid materials or harder compounds, the Shore D scale becomes relevant.
Durometer scales are not interchangeable; each is tailored to a specific range of hardness and material type. That’s why accurate durometer selection is vital to aligning the measurement with the actual performance expectations of the finished product.
How Durometer Is Measured
The standard testing method for measuring the hardness of elastomers is outlined in ASTM D2240, a procedure recognized across industries. This test involves using a durometer gauge, a device that measures the depth of indentation made by a spring-loaded needle into the material’s surface.
Factors such as the thickness of the silicone, temperature during testing, and the time force is applied can all affect the reading. For example, thinner sections or softer silicone compounds may yield lower readings due to their tendency to flex under the gauge. Therefore, consistent testing conditions and adherence to the ASTM standard are essential for reliable, repeatable results.
Durometer readings provide crucial insights into how a silicone part will behave in real-world conditions. For high-pressure applications, a higher durometer might be necessary to resist compression and extrusion. For sealing solutions that require flexibility and a tight seal, a lower durometer is often more effective.
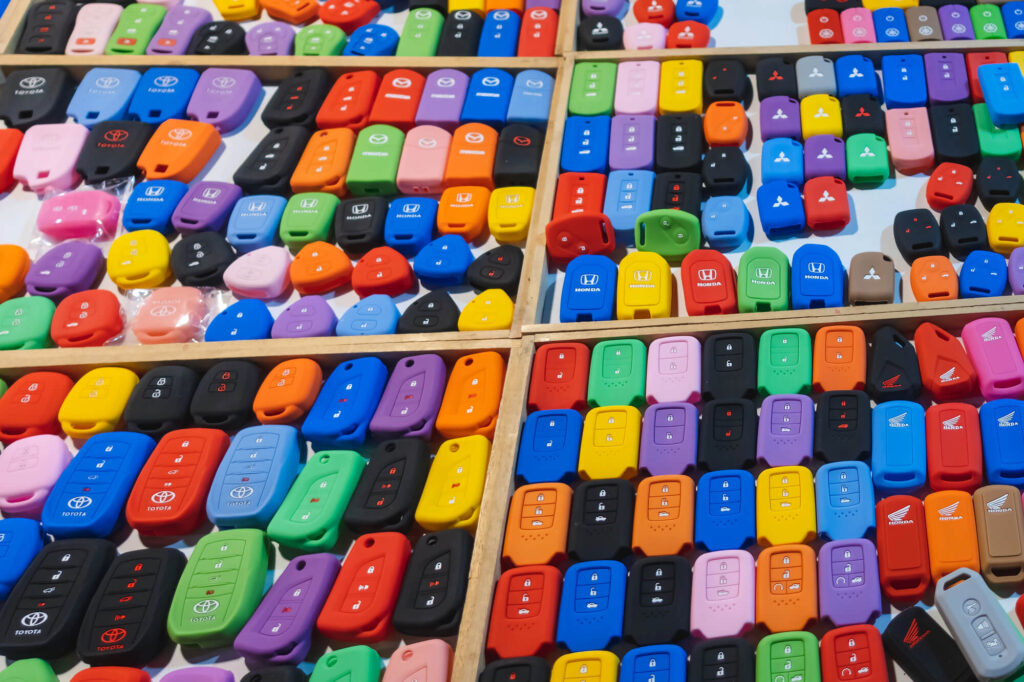
Durometer and Silicone Rubber: Key Characteristics
Silicone rubbers are among the most versatile elastomers available today, and they are used in a wide variety of applications where a balance between flexibility, durability, and environmental resistance is required. The durometer, or hardness, of a silicone rubber plays a defining role in determining its mechanical behavior, performance limits, and suitability for different operating environments.
How Silicone Durometer Affects Physical Properties
Softer materials offer enhanced flexibility and comfort, making them ideal for components that interface with human skin or require high elasticity.
Harder silicone compounds, on the other hand, resist deformation and provide better structural support in high-pressure or high-load environments.
A soft silicone rubber may compress easily for use in seals or cushioning elements. Still, it might also be prone to tearing or early material failure if used in high-compression systems. Harder materials provide durability and chemical resistance but may crack or fail to conform under flex.
Durometer Range in Silicone Elastomers
Silicone elastomers typically offer a Shore A durometer range between 10 and 80. This wide spectrum allows manufacturers to engineer components for everything from soft-contact consumer products to structural mechanical seals. Soft rubbers at the lower end provide maximum flexibility, while harder rubbers near the upper end offer superior resistance to physical abrasions and extrusion.
Specialty formulations, such as platinum-cured silicones, anti-static silicone, and temperature silicone material variants, can be tailored to meet specific industry requirements. These may be available in standard durometer options such as 40-50 medium silicone (for general-purpose seals), silicone 50A or 60A for the balance of toughness and flexibility, and even custom black silicone material designed for UV or thermal resistance.
Understanding this full range of durometers ensures engineers and designers can match the silicone compound’s characteristics precisely to the physical demands and constraints of the application environment.
Application-Specific Durometer Selection
No single durometer value fits all use cases. The right durometer selection depends heavily on the part’s functional role, the environmental conditions it will face, and the need for balance between flexibility, sealing ability, and structural integrity. Below is a breakdown of how different industries and product types dictate optimal durometer choices for silicone components.
Medical and Biotech
In medical devices, where bio-compatible silicone is a must, softer compounds (Shore A 10–40) are often selected for components like wearable sensors, tubing, and soft seals. These materials conform easily to human tissue and minimize irritation. Harder silicone materials are used in rigid housings, surgical tool grips, or implantable valves.
Automotive and Aerospace
Applications in these fields require resistance to deformation, vibration, and extreme conditions. Silicone components like O-rings, gaskets, and isolators often fall into the Shore A 60–80 range, offering high mechanical stability and excellent sealing under pressure and thermal cycling.
Consumer and Industrial Products
Everyday products such as remote control buttons, kitchen tools, and sports equipment rely on mid-range silicone durometers to strike a balance between tactile feel and durability. Industrial components like pump diaphragms or keypads may use different durometer levels depending on the required flexibility or structural support.
Factors to Consider When Choosing Silicone Durometer
A wide range of environmental and mechanical conditions must be evaluated when selecting silicone hardness:
- Environmental Conditions: Consider resistance to chemicals, oils, UV, and extreme temperatures. Harder silicones often perform better in harsh conditions.
- Mechanical Load: Softer silicones may deform or extrude under pressure. Harder silicones resist indentation but may lose flexibility and increase wear.
- Manufacturing Compatibility: Some durometer ranges perform better with specific molding processes. Harder materials release from molds more easily, while softer materials may require lower pressure and longer curing cycles.
Failing to align durometer selection with these factors can lead to premature material breakdown, suboptimal product performance, and increased manufacturing costs.A wide range of environmental and mechanical conditions must be evaluated when selecting silicone hardness:
- Environmental Conditions: Consider resistance to chemicals, oils, UV, and extreme temperatures. Harder silicones often perform better in harsh conditions.
- Mechanical Load: Softer silicones may deform or extrude under pressure. Harder silicones resist indentation but may lose flexibility and increase wear.
- Manufacturing Compatibility: Some durometer ranges perform better with specific molding processes. Harder materials release from molds more easily, while softer materials may require lower pressure and longer curing cycles.
Failing to align durometer selection with these factors can lead to premature material breakdown, suboptimal product performance, and increased manufacturing costs.
Durometer Mismatch: Risks of Poor Selection
Choosing the wrong silicone durometer for a given application can compromise product performance, reliability, and customer satisfaction. While silicone is a highly adaptable material, using a formulation that’s either too soft or too hard for its operating context can lead to a wide array of functional failures.
Underrated Risks of Too-Soft Silicone
Silicone materials on the lower end of the Shore A scale provide excellent flexibility and compression compliance, but when used in the wrong application, this softness can become a liability. Components such as seals, gaskets, or structural dampers made from too-soft silicone may experience:
- Permanent deformation under load or compression
- Leakage in sealing systems due to a lack of rebound force
- Early material failure from tearing, extrusion, or compression set
In pressure applications, overly soft materials may also lose their dimensional stability, resulting in ineffective seals or reduced structural support, especially when exposed to extreme temperatures or aggressive fluids.
Problems with Too-Hard Silicone
On the other hand, materials with excessively high durometer ratings may resist necessary deformation, leading to fitment issues, user discomfort, or cracking under stress. This is especially problematic in applications requiring tactile response, ergonomic performance, or soft interfacing with biological tissue.
Common challenges with overly rigid silicone compounds include:
- Poor sealing performance due to inadequate surface conformance
- User discomfort in touch-sensitive or wearable applications
- Cracking or micro-fracturing when flexed or over-molded into tight geometries
Striking the right balance between hardness and flexibility is therefore critical — one that considers not only material properties, but also application tolerances, sealing dynamics, and environmental demands.
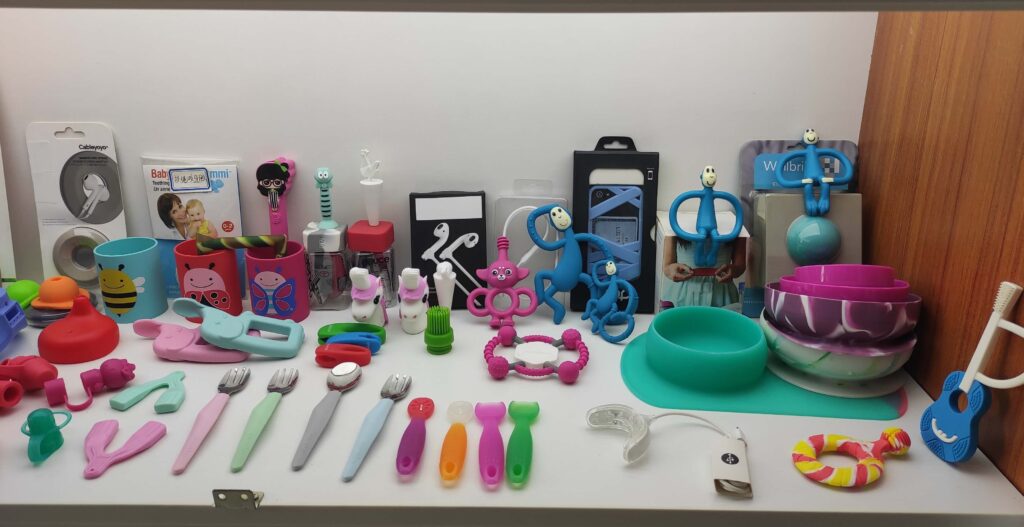
Silicone Durometer Selection in Kenvox Projects
At Kenvox, our approach to silicone part manufacturing begins with comprehensive material analysis. Our application engineers and silicone experts evaluate each component’s performance requirements, operational environment, and mechanical constraints to recommend the optimal Shore hardness level.
Using both industry standards and proprietary testing procedures, we help clients avoid costly missteps and optimize for material durability, process compatibility, and end-use reliability.
Kenvox offers silicone products across the full Shore A spectrum, with compound customization options for chemical resistance, temperature resilience, and mechanical reinforcement. From blue silicone sheets used in hygienic environments to black silicone sheet rubber formulated for heat shielding and UV stability, we provide turnkey solutions for medical, automotive, electronics, and industrial sectors.
Kenvox Helps With This Key Choice for Your Silicon Molding Project
Durometer is more than a material metric; it’s a design enabler. Choosing the right silicone hardness affects everything from the part’s mechanical behavior and sealing capability to its lifespan and user experience.
With a broad range of durometer options, accurate testing standards like ASTM D2240, and a wealth of application knowledge, manufacturers have the tools they need to make informed decisions.
At Kenvox, we help bring those decisions to life — from concept to finished product — with silicone solutions optimized for flexibility, durability, and performance under pressure.
Our materials include platinum-cured silicones, tin-based formulations, anti-static silicone, and more; each available in durometers tailored to your application needs.
Need expert support for silicone durometer selection?
Contact Kenvox to match your project’s unique demands with precision-engineered silicone rubber solutions.