Whether you’re a seasoned professional or a newcomer in the manufacturing industry, navigating the challenges of this essential process can often feel like a daunting task. Have you ever experienced production delays or unexpected defects that left you scratching your head?
With the demand for high-quality plastic components on the rise, injection molding has become a cornerstone of modern manufacturing. However, like any intricate process, it comes with its own set of common pitfalls. The injection molding industry, valued at billions of dollars, encounters various challenges ranging from material inconsistencies to equipment malfunctions. Understanding these issues is crucial for optimizing production and maintaining efficiency.
To master the injection molding process, it’s vital to identify and address these common problems effectively. From misalignments in the mold to improper cooling times, numerous factors can disrupt the process and compromise quality.
We’ll explore the prevalent problems in injection molding and present actionable solutions that can help streamline operations and enhance product integrity. Get ready to transform your approach to injection molding and drive your success in this competitive field!
What Is Injection Molding?
Injection molding (IM) is a manufacturing process used to produce parts by injecting molten material—usually plastic resin—into a mold cavity, where it cools and hardens to the shape of the mold. This process is highly efficient and suitable for mass production, allowing manufacturers to create consistent, high-quality parts in large quantities. Injection molding is widely used across various industries, including automotive, medical, consumer goods, and electronics, due to its versatility and ability to produce complex shapes with minimal waste.
The process generally involves four main steps:
- Clamping: The two halves of the mold are securely closed by a clamping unit.
- Injection: Molten plastic resin is injected into the mold under high pressure.
- Cooling: The plastic cools and solidifies within the mold.
- Ejection: The finished part is ejected from the mold, and the process repeats.
Benefits of Injection Molding
By employing advanced methods, IM enables the quick and cost-effective production of intricate designs, offering numerous advantages to various industries:
- High Efficiency for Mass Production: Injection molding enables the fast and consistent production of large volumes of parts, making it ideal for mass manufacturing.
- Design Flexibility and Complexity: Allows for the creation of intricate and detailed shapes that would be difficult or costly to achieve with other manufacturing methods.
- Material and Color Flexibility: Compatible with a wide range of plastic materials and resins and allows for easy color customization.
- High Repeatability With Precesion: Once the mold is created, each part produced is virtually identical, ensuring high precision and consistent quality.
- Cost-Effectiveness: The automated nature of injection molding reduces labor requirements, lowering overall production costs. Additionally, excess material can often be recycled, reducing waste and making the process more cost-effective and environmentally friendly.
These benefits make injection molding a preferred choice in industries ranging from automotive to consumer electronics and medical devices.
Types of Injection Molding and Materials Used
There are several types of injection molding processes, each suited to different production needs and materials.
Here are the most common types:
- Thermoplastic Injection Molding: The most common form, this type, uses thermoplastic materials that soften when heated and solidify when cooled. This process can be repeated multiple times, allowing for recyclability and cost-effectiveness. It is widely used for consumer goods, automotive parts, and electronic housings.
- Thermoset Injection Molding: This process uses a type of plastic called thermosetting polymers, which are injected into the mold cavity. Unlike thermoplastics, these materials harden permanently after being heated, resulting in parts that are highly heat- and chemical-resistant but cannot be remolded or recycled. Ideal for high-heat applications, such as electrical insulators and appliance parts.
- Overmolding: Overmolding involves injecting one material over another to create a single, unified product with two or more materials. This process is often used to add a soft grip or ergonomic surface over a harder plastic base. Used commonly in handles, grips, and buttons, such as those on tools and electronic devices.
- Insert Molding: This is similar to overmolding; insert molding places a pre-fabricated component (like a metal insert) within the mold before injecting the plastic around it. This creates parts with embedded components, combining multiple materials in a single production step. It’s often used for parts with metal threaded inserts, such as in the automotive and electronics industries.
- Rapid Injection Molding: Rapid injection molding is designed for quick production cycles and swift prototyping, making it ideal for industries that need fast design testing and validation. This method utilizes less costly, lightweight molds typically crafted from materials like aluminum or low-temperature molten materials, which can be rapidly produced in small quantities. It enables businesses to trial designs, collect user feedback, and implement changes prior to ramping up to mass production. Moreover, it is well-suited for low to medium-volume production, offering a cost-effective solution for startups and companies looking to launch new products without the heavy financial commitment required by conventional IM techniques.
Each type offers unique advantages and is suited to specific materials and product requirements. By choosing the right type, manufacturers can optimize production for cost, durability, and efficiency.
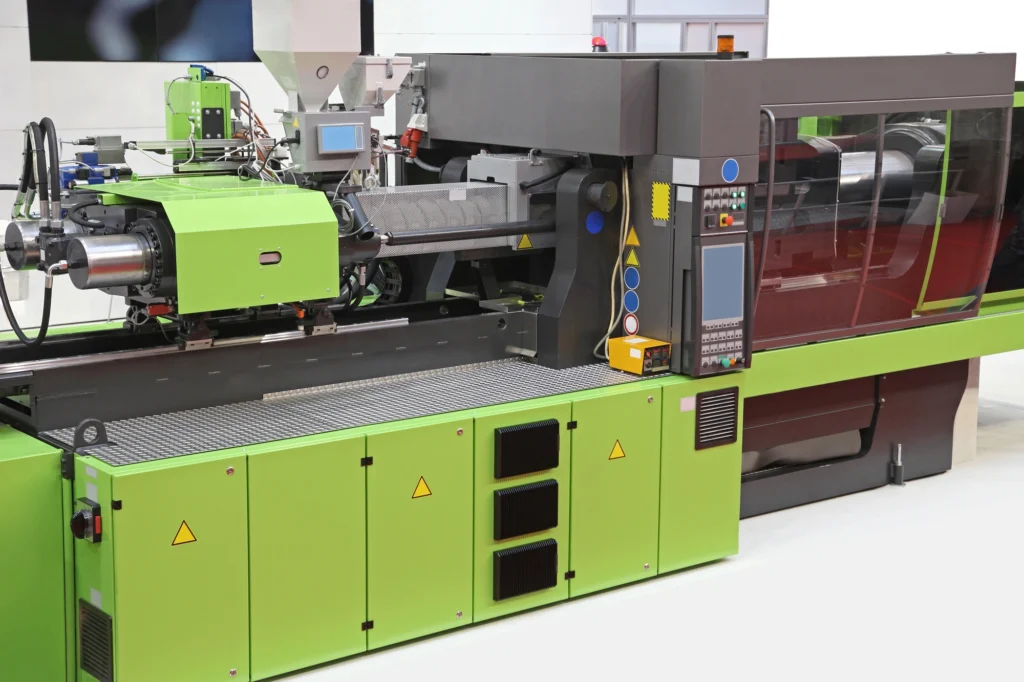
Common Defects in Injection Molding, They’re Solutions, and Why They’re Normal
While injection molding is a highly efficient and versatile manufacturing process, it can sometimes be prone to certain issues that lead to product defects. Various factors—such as material selection, mold design, and processing conditions—play crucial roles in achieving the desired quality.
However, slight variations in these elements can introduce potential injection molding defects like flow lines, warping, sink marks, and more. These imperfections can compromise the appearance, functionality, and strength of the injection molded parts, leading to increased production costs and time if not addressed.
Fortunately, most common injection molding problems have known causes and solutions. By understanding the root causes of common injection molding defects, manufacturers can make adjustments to the mold design, processing parameters, or materials, minimizing production issues and improving the quality and consistency of the final product.
The following section outlines some of the most common defects in injection molding and practical strategies to solve them.
Flow Lines
Flow lines or flow marks are visible patterns or streaks that appear on the surface of the molded part, often following the flow of the molten plastic as it enters the mold.
These lines occur when there are variations in the speed, temperature, or pressure of the molten plastic as it flows into the mold. They can also result from sudden changes in the wall thickness or the design of the mold.
How to Solve this Problem
- Increase the injection speed and pressure to ensure consistent filling.
- Raise the mold temperature to help the plastic flow more smoothly.
- Redesign the mold with smoother transitions and avoid sudden thickness changes.
- Consider using materials with better flow characteristics.
Warping
Warping is the bending or twisting of the molded part after cooling, leading to a distorted shape.
Warping happens when there’s uneven cooling or shrinkage in different parts of the molded part. Materials with high shrinkage rates or uneven wall thickness can exacerbate warping.
How to Solve this Problem
- Adjust the cooling rate to be more gradual and uniform.
- Use materials with lower shrinkage properties, such as resins designed for dimensional stability.
- Design the part with uniform wall thickness to reduce shrinkage variations.
- Optimize the mold’s temperature distribution, ensuring even cooling.
Splay Marks or Streaks
Splay marks, often manifested as silver streaks on the surface of the parts, present a significant cosmetic and structural concern in plastic injection molding. It happens when water, air, or char runs along the surface of the product during the injection process, following the material flow path.
The most common causes are too much moisture or air in the raw material or foreign material in it, although it can also be because of insufficient pressure in the flow.
Preventing these defects involves precise control over material, process, and injection molding equipment
How to Solve this Problem
- To effectively prevent splay marks in the injection molding process, it is essential to control moisture levels in the material before use.
Reduce melt temperature by lowering the barrel temperature. - Optimizing the design and refining the production process can greatly reduce the occurrence of these defects.
- Increase in the injection mold temperature or injection pressure.
- Additionally, the careful selection and application of mold release agents guarantee cleaner and more consistent outputs, further enhancing control over the final product quality in injection molding operations.
Sink Marks
Sink marks are small, sunken areas that appear on the surface of the finished product, often in thick sections. They occur when the inner part of a thick wall takes longer to cool and shrink than the outer surface, creating a sunken spot. Inadequate packing pressure or cooling can worsen this.
How to Solve this Problem
- Increase the packing pressure to ensure the mold cavity is fully filled.
- Extend the cooling time to allow more even solidification.
- Redesign the part to avoid thick sections or include ribs to reinforce the structure without adding bulk.
- Use materials that are less prone to shrinkage, particularly for thick-walled parts.
Vacuum Voids or Bubbles
Voids are air bubbles or empty pockets that appear within the molded part, weakening it and potentially affecting its appearance. It is one of the most common molding defects.
Vacuum voids can form when the mold cavity isn’t entirely filled, or the molten plastic doesn’t compress enough to expel trapped air. Insufficient injection pressure, inadequate venting, and an uneven cooling process can also contribute to void formation.
How to Solve this Problem
- Increase injection pressure and speed of injection to compress the plastic fully.
- Use a higher injection temperature to improve the flow and reduce the chance of air pockets.
- Optimize the gate locations to ensure better flow and compression, preferably nearer the thicker sections of the part.
- Change to a less viscous plastic resin.
- Consider using a vacuum-assist system to remove trapped air and poor venting
Burn Marks
Burn marks appear as dark or blackened areas on the part, typically near the end of the flow path.
They result from trapped air or gas overheating due to compression, leading to burns on the plastic surface. This can happen from excessive injection pressure and speed or improper venting.
How to Solve this Problem
- Add proper venting in the mold to allow trapped air to escape.
- Reduce injection speed and pressure to minimize heat from compression.
- Check for obstructions in the mold that could trap air or slow down the flow.
- The melting temperature of the plastic product is too high.
- Improper runners are another cause. Check the system.
Jetting
Jetting is a wavy pattern that forms on the part’s surface due to the molten plastic’s initial high-speed entry into the mold. When molten resin flows too quickly into the mold cavity, it can “jet” through narrow areas without touching the mold walls, creating a wavy, inconsistent surface.
Several factors can be at play here, from the injection gate design being too small to excessive injection speed.
How to Solve this Problem
- Lower the injection speed to reduce the initial momentum of the plastic.
- Increase the melt temperature to promote smoother flow and better filling.
- Redesign the gate location to allow for a more gradual flow rate and reduce abrupt changes in speed.
Weld Lines
Weld lines (or knit lines) are faint lines that form where two flow fronts meet in the mold.
When the molten plastic fills the mold from different gates or directions, the flows meet and may not bond perfectly, creating weak points.
How to Solve this Problem
- Increase the injection speed and temperature to improve the bonding between flows.
- Relocate gates in the injection molding machine to optimize the flow paths and reduce the number of weld points.
- Choose materials with better flow speed and weld line strength for improved bonding.
Fog
Fogging in injection molding can obscure the clarity of plastic parts, affecting their aesthetic and functional quality. It shows up almost as a cloud or “fog” on the surface of the product near the injection molding gate. Causes can include the gate being too small and excessive shear rate.
How to Solve this Problem
- Guarantee the mold and materials are pre-conditioned correctly to avoid moisture-related issues.
- A mold flow analysis and simulation might recommend moving the mold gate or other changes to the mold design.
Gate Vestige
Gate vestige refers to the small protrusion left on a molded part after the removal of the gate material, which can affect both the aesthetic and functional quality of the final product. It might be due to an unsuitable gate location or too much injection speed and pressure.
How to Solve this Problem
- To prevent this issue, careful consideration of gate location, size, and design during the tooling phase is essential.
- Additionally, optimize the injection molding process parameters such as injection filling speed and pressure, temperature, and cooling time.
Delamination
Delamination in injection molding refers to the separation of material layers into thin slices that can be peeled away, which can compromise the structural integrity of the final product.
The likely causes include foreign materials in the injection molding material, leading to areas where the molten plastic material cannot bond properly. It can also be due to inconsistent resin temperature, excessive moisture, and shape angles in the flow paths and angles.
How to Solve this Problem
- Ensure the purity of the raw materials.
- Avoid uneven flow from the gate.
- In the process, increase the barrel and mold temperature.
Discoloration
Discoloration appears as unwanted colors or streaks on the part. It’s often due to contamination in the material, prolonged heating, or improper temperature settings.
How to Solve this Problem
- Use clean, properly stored materials and ensure no contamination between colors.
- Lower the barrel temperature to avoid overheating the plastic.
- Purge the injection machine thoroughly between different material runs.
Flash
Flash is excess plastic material that leaks out of the mold cavity and solidifies on the part’s edges. It can happen when the mold halves don’t close properly or if the injection pressure is too high.
How to Solve this Problem
- Adjust clamping force to ensure a tight mold seal.
- Reduce injection pressure if it’s too high, which can prevent material from squeezing out.
- Check and repair mold surfaces to ensure there’s no wear or damage that could cause leaks.
Short Shots
Short shots occur when the mold cavity is not completely filled, leading to an incomplete part.
They’re typically caused by insufficient material or injection pressure, overly low melt temperature, or blockages in the mold (poor exhaust.) It can also happen because the part is too thin.
How to Solve this Problem
- Increase injection pressure and material temperature or resin temperature to ensure the cavity fills.
- Check for mold obstructions that could be blocking material flow.
- Check the feeding port to see if it has material or if it is bridged.
- Redesign the part of the mold to avoid thin sections that may cause flow stoppages.
Kenvox Injection Molding Offers Highest Quality Assurance to Prevent Costly Defects
In summary, injection molding, while efficient, is susceptible to various defects that can impair product quality. Addressing these challenges requires meticulous optimization of processing parameters, such as temperature, injection speed, and cooling rates.
Kenvox has implemented an extensive set of quality assurance protocols designed to mitigate costly defects in the manufacturing process. This rigorous approach involves multiple stages of checks and balances, ensuring every product meets the highest standards of quality and functionality.
By integrating advanced diagnostic tools and state-of-the-art monitoring systems, Kenvox effectively identifies and addresses potential issues before they escalate into expensive production errors. Additionally, the company invests in continuous training for its staff, equipping them with the knowledge to uphold exceptional quality control.
This proactive stance not only enhances product reliability but also reinforces customer trust, establishing Kenvox as a leader in delivering defect-free injection molded components.