Silicone often comes up in everyday discussions about its use in medical devices, implants, and other healthcare applications, leaving many wondering why it’s such a common material in health and medicine.
That’s due to one of the most crucial properties of silicone: biocompatibility.
Biocompatibility refers to the ability of a material to come into direct contact with the human body or biological tissue without adverse effects. This is particularly crucial in medical applications, where materials must not cause adverse reactions or trigger immune responses. Silicone has emerged as a key material in the industry due to its unique combination of chemical inertness, mechanical properties, and thermal stability.
From surgical tools to wearable medical devices, the application of silicone in skin-contact and biomedical applications continues to grow. Its compatibility with human tissues and bodily fluids makes it ideal for use in medical-grade products that meet the stringent requirements of the medical device industry.
What Is Silicone and Why It Matters in Medical Manufacturing
Silicone is a synthetic polymer, or elastomer, primarily composed of silicon, oxygen, carbon, and hydrogen. Its backbone structure grants it a remarkable balance of elasticity and stability, making it ideal for use in complex structures and extreme conditions. There are two primary types of silicone materials used in medical manufacturing:
- Liquid Silicone Rubber (LSR): Characterized by low viscosity, high precision, and excellent tear strength. LSR is optimal for high-volume production of complex geometries such as medical tubing and silicone hydrogel lenses.
- Solid Silicone Rubber (SSR): Known for its high mechanical strength and thermal cycling resistance, suitable for robust applications including artificial heart valves and medical implants.
For either liquid silicone rubber or its solid version to be used in any type of medical application, they must pass through a curing process (drying, essentially) that removes any possible impurities or byproducts that can be harmful to the human body. Afterward, it becomes medical-grade silicone rubber.
Silicone Molding Techniques at Kenvox
Kenvox specializes in both compression and injection molding techniques. With over 40 dedicated silicone molding machines and decades of expertise, Kenvox is equipped to produce silicone components with exceptional consistency and quality. The company utilizes advanced technologies to enable direct printing, rapid prototyping, and large-scale silicone part production across a wide variety of medical device applications.
Understanding Biocompatibility in Silicone
Silicone’s excellent biocompatibility stems from its:
- Chemical inertness: It does not react with bodily fluids or cause poisoning of silicones.
- Non-toxicity and hypoallergenic nature: Reduces the risk of allergic reactions and foreign body reactions.
- Thermal stability and chemical stability: Withstands elevated temperatures and harsh sterilization methods without degrading.
- High gas permeability: Ideal for implantable devices and wound care products.
These properties allow silicone adhesives, silicone elastomers, and silicone rubber compounds to be safely used in direct contact with biological tissue. Biocompatible silicone adhesives and silicone sheets offer strong bond strength and consistent performance in both temporary and long-term implant applications.
Biocompatibility Testing Standards
Medical-grade silicone must pass rigorous testing, including:
- USP Class VI: A standard that evaluates systemic toxicity, intracutaneous reactivity, and implantation effects.
- ISO 10993: A comprehensive series of biological evaluations covering cytotoxicity, sensitization, and systemic effects.
Kenvox is also fully compliant with ISO13485, demonstrating its commitment to meeting international standards in medical device manufacturing and ensuring traceability throughout the production cycle.
Key Benefits of Biocompatible Silicone for Medical Use
- High purity: Medical-grade silicone rubber is manufactured using ultra-clean raw materials, which are essential for sensitive medical procedures and long-term implants.
- Exceptional physical properties: These include high tensile strength, elongation, permeability to gases, and tear strength, ensuring the silicone retains integrity under stress and dynamic conditions.
- Excellent flexibility across a broad range of temperatures: Silicone maintains its elasticity and function in both cold storage and elevated temperatures, making it suitable for environments with thermal cycling.
- Sterilizability: Silicone can be sterilized using a variety of methods, including autoclaving, gamma radiation, and ethylene oxide, making it highly adaptable to different clinical environments.
- Chemical resistance: It resists degradation from biological fluids, body fluids, soft tissue, and environmental exposure, which enhances long-term durability and safety.
- Minimal adverse reactions: The material shows low levels of microorganism adhesion and bacterial adhesion, reducing risks associated with infection and biofilm formation.
- Transparency and surface properties: These characteristics support advanced diagnostic devices and direct printing applications where visual monitoring is crucial.
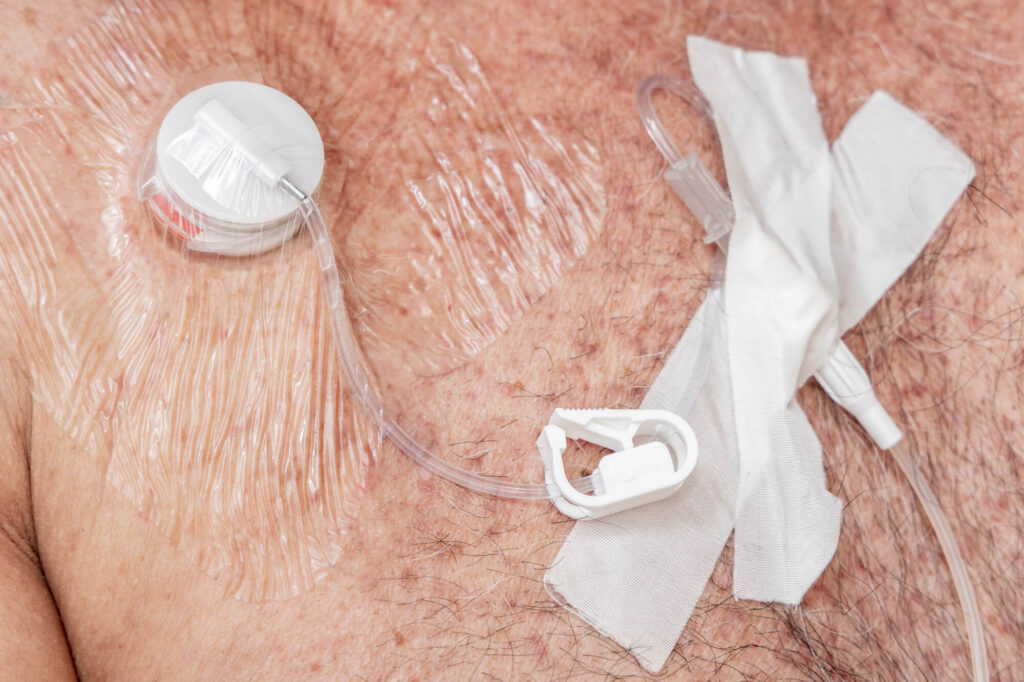
Use Cases in the Medical & Skin-Contact Industries
Biocompatible silicone has become a pivotal material in the medical and skin-contact industries due to its unique mechanical properties and wide range of uses.
From implants and prosthetics to wearable medical devices, its adaptability and reliability provide effective solutions that meet the complex requirements of these fields.
Examples of Biocompatible Silicone in Medical Devices
Silicone is integral to numerous medical technologies due to its excellent biocompatibility and adaptability, especially for long-term implantation on human tissues. Common applications include:
- Catheters and medical tubing: Providing flexibility and strength, crucial for patient comfort and fluid management.
- Wound care products and dressings: Ensuring breathable, non-stick contact layers that promote healing.
- Surgical tools and components: Resistant to environmental stress and repeated sterilization cycles.
- Implantable devices: From artificial heart valves to orthopedic supports and silicone breast implants, silicone is used for long-term implant applications.
- Prosthetic devices: A wide range of uses in prosthetics, from auricular prosthesis to orbital prosthesis, and mammary prosthesis, due to their lifelike texture and appearance.
Applications in Skin-Contact Products
Medical grade silicone rubber is also widely used in products intended for regular or prolonged skin contact:
- Baby pacifiers, bottles, and teething rings: Safe, hypoallergenic, and compliant with global safety regulations.
- Wearable devices and monitoring patches: Providing soft, conformable contact with human skin.
- Cosmetic tools and applicators: Durable, washable, and antimicrobial properties make silicone ideal for repeated skin use.
- Silicone adhesives and sheets: Used in transdermal patches and scar treatment, offering strong adhesion without skin irritation.
Why Kenvox is a Trusted Partner for Biocompatible Silicone Manufacturing
Kenvox brings decades of experience in silicone molding and medical manufacturing. Key differentiators include:
- Cleanroom-certified facilities for producing silicone medical products and medical-grade silicone rubber components.
- ISO9001, ISO13485, IATF16949, and BSCI certifications, ensuring high compliance and quality control.
- Proprietary ERP systems for managing raw materials, adhesive viscosity, paste viscosity, and maintaining traceability.
- Ability to handle complex geometries and custom assembly requirements for the medical device industry.
- Proven expertise with LSR, SSR, and silicone dispersions, delivering optimal performance across diverse biomedical applications.
Beyond Healthcare: Other Industries Benefiting from Silicone Molding
Silicone’s versatility extends into many sectors outside of the medical industry, owing to its durability, thermal resistance, and chemical inertness:
- Consumer Goods: Silicone is widely used in kitchenware like baking mats, spatulas, and molds due to its non-stick properties and safety at extreme temperatures. In personal care, it is used for brushes, containers, and cleansing tools.
- Baby Products: Beyond pacifiers, silicone is trusted for bottles, nipples, spoons, and toys that require both softness and durability when on an infant human body. It is also resistant to UV exposure and repeated sterilization.
- Automotive Applications: Silicone components such as gaskets, seals, and tubing are essential in automotive systems that demand high temperature tolerance, low gas permeability, and long-term durability.
- Aerospace and Industrial Applications: Used in vibration damping, insulation, and sealing, silicone resists chemical degradation and maintains structural integrity under extreme operational stress.
- Pharmaceutical Industries: Silicone sheets, elastomers, and gels are employed in drug delivery devices, lab equipment seals, and bioactive agents carriers due to their non-reactive nature and sterilization compatibility.
Silicone, the Winning Material Kenvox Can Offer to Any Medical Manufacturer
Silicone continues to define the future of biocompatible materials in medical technology. Its unique combination of mechanical, thermal, and chemical properties makes it an indispensable material for medical device manufacturers and skin-contact product innovators.
At Kenvox, we bring together cutting-edge silicone molding techniques, robust quality assurance, and decades of experience to deliver high-performance silicone components for your most critical applications.
Contact Kenvox today to explore how our medical-grade silicone solutions can elevate your next project.