A frequently overlooked factor by businesses looking for the right silicone molding process for their products is the surface finish on the molds themselves. They’re not just a cosmetic choice for the molds; they directly impact the performance, feel, and functionality of silicone products.
A surface finish refers to the texture or polish applied to a mold cavity, which in turn defines the texture of the final injection-molded part. For silicone and plastic materials alike, these finishes affect everything from grip and aesthetics t
In silicone molding, commonly used texture standards include SPI (Society of the Plastics Industry) grades such as Diamond Buff or Grit Paper, as well as VDI 3400 and Mold-Tech finishes. Advanced technology and specialized equipment are used to achieve these precise surface finishes. Commercial finish tolerances are available for less critical applications, offering a cost-effective solution, while higher-precision or custom finish options are chosen for more demanding requirements. Choosing between a dull finish, a low polish part, a glossy surface, or specifying a custom finish for unique design or functional needs comes down to design intent, product application, and the unique properties of silicone, including material hardness, color, and fillers.
With this guide, you’ll know just how these surface texture finishes ensure that both design and regulatory requirements are met from the start.
Why Surface Finishes Are Critical in Silicone Molding
The surface texture of silicone molded parts plays a crucial role in both performance and manufacturability.
- Product Function: For functional silicone or silicone rubber components like seals, buttons, or wearable grips, surface finish affects tactile experience, friction, and even product safety. A dry-blast matte finish, for instance, may enhance grip, while a glossy finish can improve cleanability or aesthetics. Flexible surface finishes are especially important for components that require adaptability in various environments.
- Affected by Material Properties: The material properties of the silicone product and the mold also dictate how finishes behave. The softness of liquid silicone rubber, the presence of fillers, and mold temperature all influence how textures are faithfully transferred from mold to part.
- Mold Behavior: Surface finishes affect the mold cavity’’s behavior during liquid injection molding, altering flow dynamics, cavity filling, venting, and demolding efficiency. Certain finishes can also facilitate easier removal of parts from the mold, improving production speed and reducing defects.
- Improves Mold Surface for Release: The right finish can reduce the need for mold release agents, minimize surface imperfections like gas bubbles, and extend mold life.
- Impacts Secondary Processes and Assembly: Mold surface finishes also play a critical role in downstream processes such as over-molding, labeling, ink adhesion, and bonding in multi-material assemblies, especially in regulated industries like medical devices, automotive, and consumer wearables. Additionally, surfaces can be further treated to enhance appearance or functionality, increasing the value and performance of the final product
Overview of Silicone Manufacturing at Kenvox
Kenvox offers a wide range of silicone molding capabilities, allowing designers and engineers to align manufacturing methods with product performance, surface texture, and production scale. Each technique has distinct implications for surface finish fidelity and tooling options.
- Liquid Silicone Rubber Injection Molding: Ideal for high-precision, high-volume components, liquid silicone injection molding (LIM) allows excellent surface finish replication due to the low viscosity of the silicone. Liquid injection molding is well-suited for medical devices and wearables where smooth, consistent textures and dimensional control are critical.
- Solid Silicone Rubber Injection Molding: Used when specific hardness or higher mechanical strength is required, and solid silicone rubber injection molding accommodates tighter tolerance parts. Though the material has less flow than LSR, proper tooling and mold cavity design can still support VDI and SPI finish replication.
- Silicone Compression Molding: Best for thick-walled or low-to-medium-volume components. It allows broader material selection but has slightly less control over fine surface detail. Compression molding still supports SPI standard texture replication like Grit Paper and Dry Blast Glass Bead, but may require adjusted demolding angles.
- Silicone Epoxy Processes: This hybrid process incorporates both silicone and epoxy materials for parts requiring chemical resistance and structural stiffness. The surface finish can be critical here for adhesion, coating compatibility, and seamless bonding at material transition points.
- Silicone Extrusion: For continuous profiles such as tubing and seals, extrusion offers minimal surface finish customization. However, surface roughness and part gloss can be affected by die design and the curing process. It’Controlling curing time and temperature during extrusion is essential to achieve the desired surface finish and optimal product properties. Improper curing time or exposure to high temperatures can result in silicone products that are too soft or become brittle, negatively impacting both surface quality and mechanical properties. It’s often used in conjunction with post-processing to enhance texture.
Tooling Capabilities for Silicone Surface Finishes
Kenvox supports both silicone injection and compression tooling or mold making, with high-precision mold fabrication to ensure consistent surface texture reproduction.
Tooling materials include:
- Hardened steel
- Aluminum molds
Both can be customized with VDI or SPI finishes and textures.
- Advanced CAM programming and three-axis milling ensure collision avoidance routines and optimal toolpath strategies for creating complex surface geometries.
- Simulation software such as Autodesk Moldflow supports cavity filling, venting, and gating design, ensuring that textures transfer cleanly without voids or defects.
- Electric discharge machining (EDM) and polishing techniques (Grit Diamond Buff, Grit Stone) are used to minimize tool marks on the mold surface, improving the cosmetic quality and aesthetic appeal of the final silicone product while allowing the tooling surface to meet strict surface finish specifications.
- Mold surface validation using gloss unit testing and profilometry to meet FDA standards and product design requirements.
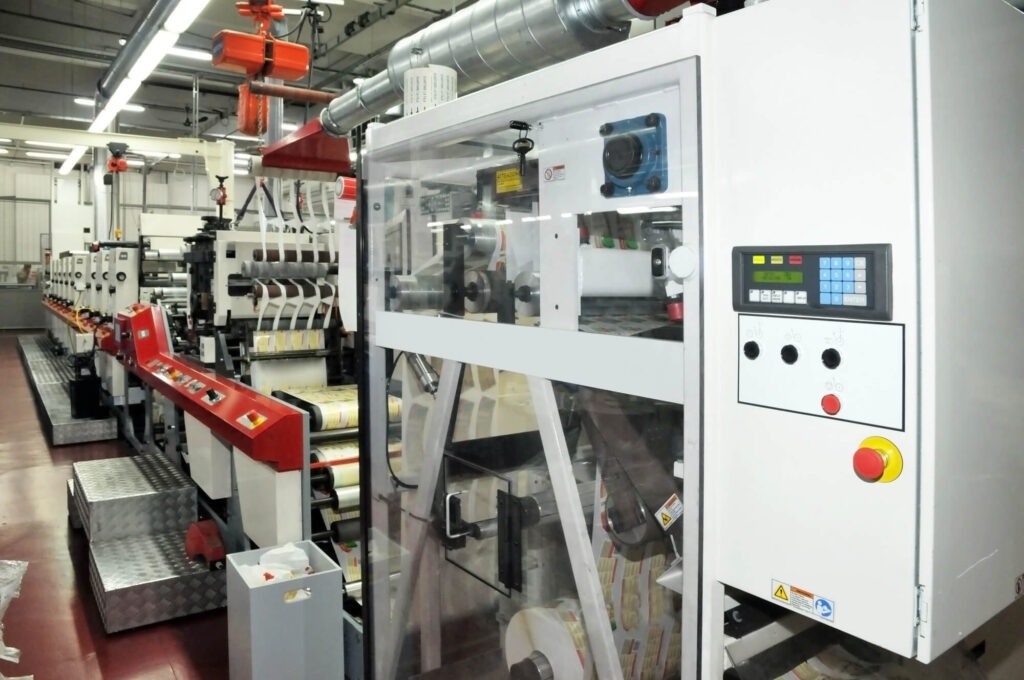
Mold Release and Its Impact on Surface Finish
Mold release plays a pivotal role in the injection molding process, directly influencing the surface finish of the final silicone product. The application of mold release agents is essential for ensuring that silicone products can be easily removed from the mold without damage. However, the type and method of mold release used can significantly affect the appearance and performance of the finished part.
Residues from mold release agents may remain on the surface of silicone products, sometimes resulting in an oily or uneven appearance that detracts from the desired finish. This can be particularly problematic for products requiring a high-gloss or flawless surface, as even minor residues can interfere with the final look. Additionally, leftover mold release can hinder the adhesion of coatings, labels, or printing applied during secondary processes, potentially compromising both aesthetics and functionality.
To achieve the best possible surface finish, it is crucial to select a mold release agent that is compatible with the specific silicone material and the intended use of the product. For example, a mold release with good adhesion and abrasion resistance is often suitable for silicone products that demand a durable, glossy finish. Proper application techniques are equally important—using the right amount and ensuring even coverage can help minimize residue and maintain the integrity of the surface.
Ultimately, careful consideration of mold release in the molding process helps guarantee that the final product meets both visual and performance expectations, supporting the overall quality and reliability of silicone products.
Common Types of Surface Finishes & Their Characteristics
SPI finishes, VDI textures, and Mold-Tech; these different finishes can affect factors such as tactile feel, gloss, and resistance to wear or dirt, s. A rough surface finish can negatively impact product appearance and reduce sealing effectiveness, making it important to select the appropriate texture. So let’’s explore some of the most common types of surface finishes and their unique attributes.
SPI Finish Standards
SPI (Society of the Plastics Industry) finish standards are widely used to categorize surface finishes in injection molding. These include:
- A-series (Grit Diamond Buff): High-gloss finishes ideal for parts requiring optical clarity or a sleek, reflective surface. Common in consumer electronics and medical housings.
- B-series (Grit Paper): Semi-gloss or satin finishes, achieved through medium-grit abrasives. Suitable for general applications where gloss is not critical.
- C-series (Grit Stone): Matte or low-luster finishes, offering excellent mold release and low visibility of scratches or imperfections.
Each SPI grade correlates to a specific polishing method and texture depth, influencing not just aesthetics but demolding and downstream processing.
VDI 3400 Finishes
Developed by the German engineering association (Verein Deutscher Ingenieure), VDI 3400 finishes are based on surface roughness values achieved through blasting techniques. Common types include:
- Dry Blast Glass Bead: Produces a fine matte texture, which is excellent for improving grip and hiding surface flaws.
- Dry Blast Aluminum Oxide: Offers a coarser finish suitable for technical parts requiring higher friction.
- Stone Finish (gloss control): Used for managing gloss levels in medical, automotive, and wearable applications.
VDI textures are often specified using numeric codes that directly reflect micrometer roughness values, making them easy to quantify and reproduce. They have some SPI finish analogues or counterparts, although some VDI textures can be unique to them.
Mold-Tech and Custom Etching Finishes
Mold-Tech finishes offer proprietary mold cavity textures for branding, style, or improved functionality. These can include leather-like textures, geometric patterns, or custom logos etched directly into the mold. Laser etching and custom finishes can also be used to form unique visual effects or functional symbols on the silicone surface, enhancing both aesthetics and usability. Often used in high-end consumer products or where branding is crucial.
H3: Dull Finish vs Gloss
- Dull finishes: Tend to be more forgiving in production, masking flow lines and tool wear.
- Gloss finishes: Visually striking but demand rigorous mold polishing and cleaning to maintain consistency across production runs.
The transfer of surface texture also depends on material hardness and processing conditions like cavity temperature and venting.
Factors to Consider When Choosing a Silicone Surface Finish
Choosing the right silicone surface finish depends on a combination of material, functional, and manufacturing variables. Below are the primary factors to evaluate:
- Material Properties: Silicone rubber varies in hardness, cure chemistry, and filler content. Softer grades like Dry Blast or those with higher filler loads may dull the sharpness of transferred textures. Heat-cured materials and transparent silicone also behave differently under pressure and heat in terms of how they replicate surface textures. Deformation under compression can affect the ability of silicone seals to recover their original shape and maintain a proper seal, which is critical for preventing leaks. Selecting the wrong material can increase the risk of break or cracking in low-temperature environments, so it’s important to consider the flexibility and durability of the elastomer. When evaluating performance and regulatory requirements, consider other materials in addition to silicone to ensure optimal results.
- Product Functionality: Aesthetics, grip, tactile sensation, and cleanability are all tied to surface texture. Medical devices often require matte textures for anti-glare and tactile control, while consumer goods might favor a glossy surface for premium appeal. Sealing components may require rougher textures for improved adhesion. The elasticity of silicone is important, as it allows the material to conform to curved surfaces or recover after stress, which can be beneficial for certain applications.
- Mold Design: Draft angles, cavity venting, gating, and ejector pins all affect the ability of the mold to reproduce textures cleanly. For more complex textures like Mold-Tech or deep VDI finishes, mold temperature control and gas flow modeling can improve texture fidelity and reduce defects.
- Manufacturing and Maintenance Considerations: High-gloss finishes require regular cleaning and maintenance to avoid degradation. Matte textures from dry blasting may extend tool life but reduce surface gloss. Cycle time, material flow, and cooling strategies also play a role in achieving consistent finishes across high-volume production.
These considerations ensure the silicone surface finish not only meets the design specification but also aligns with the realities of mass manufacturing and quality control. Before full-scale production, verify that the surface finish and material properties meet the expected performance standards to ensure reliable results.
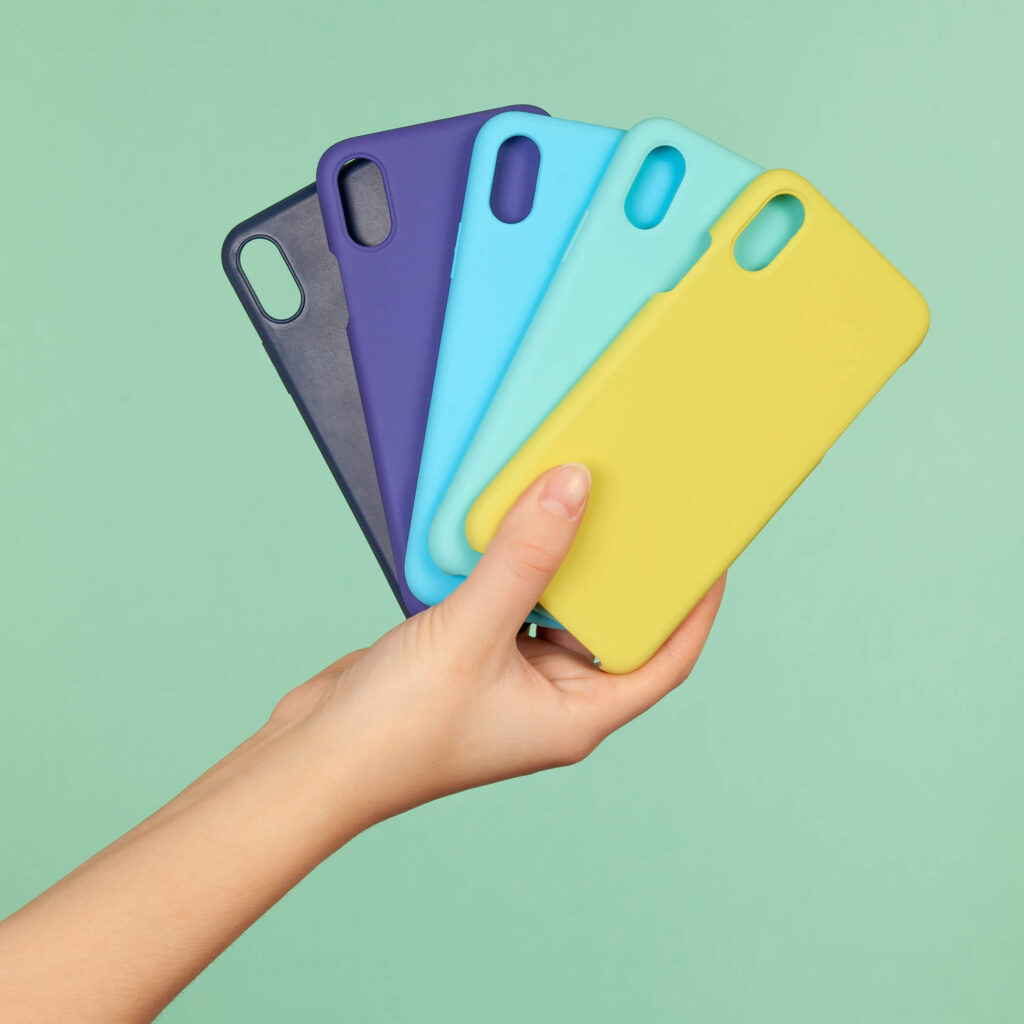
Pros & Cons of Each Surface Finish Option
Each surface finish option offers specific benefits and trade-offs depending on product needs, mold tooling, and application context. Below is a breakdown:
- SPI Finish A-1 (Grit Diamond Buff)
Pros: Ultra-glossy, premium appearance, excellent mold release, ideal for transparent or polished parts.
Cons: High tooling cost, time-intensive polishing, requires mold maintenance, and is less forgiving of imperfections. - SPI Finish B-2 (Satin / Grit Paper)
Pros: Balanced surface feel, easier demolding, moderate cost, reduced polishing requirements.
Cons: Less shine, may not hide surface imperfections as effectively. - SPI Finish C-3 (Matte / Grit Stone)
Pros: Excellent for non-slip finishes, masks imperfections, and cost-effective surface texturing.
Cons: The manual labor is intensive, and there is texture inconsistency in large surface areas. - VDI 3400 Dry Blast Finishes (Glass Bead, Aluminum Oxide)
Pros: Matte aesthetic, effective at hiding flow lines and flash, good for tactile grip.
Cons: It can reduce mold life due to abrasive wear, and rougher textures may affect cleanability. - Mold-Tech / Custom Etching
Pros: Branding potential, high visual differentiation, wide design latitude.
Cons: Longer lead times, increased tooling complexity and cost, potential transfer inconsistencies in high-durometer silicone. - Gloss vs. Dull Finishes
Glossy Finishes: Premium look, easier to clean, better for aesthetics, but demands exact tooling control.
Dull Finishes: Better grip and anti-glare properties, lower maintenance, ideal for functional components.
After molding, trimming is a crucial post-molding process used to remove flash and refine the final surface finish of silicone products. Methods such as die trimming, hand trimming, and tumble trimming help achieve a smooth, polished, or specific texture, ensuring the finished part meets appearance and quality requirements.
Surface Treatment Techniques for Enhanced Performance
Enhancing the surface finish of silicone products often involves specialized surface treatment techniques tailored to the application’s requirements. These methods not only improve the appearance of silicone surfaces but also boost their durability, functionality, and resistance to wear.
- Screen Printing: Ideal for relatively flat silicone surfaces, screen printing allows for the application of detailed graphics, logos, or text. This method is widely used for branding and labeling, providing a crisp, durable finish.
- Pad Printing: More versatile than screen printing, pad printing can be used on both flat and uneven silicone surfaces. It is suitable for adding intricate designs or markings to complex shapes, ensuring consistent quality across a range of products.
- Laser Etching: This technique uses focused laser beams to create precise patterns, textures, or identification marks directly on the silicone surface. Laser etching is valued for its ability to produce permanent, high-contrast designs without adding extra material.
- Epoxy Coating: Applying an epoxy coating to silicone products results in a hard, glossy finish that enhances abrasion resistance and overall durability. This method is particularly effective for products that require a smooth, protective surface.
- Spray Painting: Spray painting can be used to apply a uniform coating to silicone surfaces, improving their resistance to scratches and environmental factors. It also allows for a wide range of color and finish options, from matte to high-gloss.
By selecting the most suitable surface treatment method, manufacturers can achieve the desired surface finish, improve product performance, and extend the lifespan of silicone products in demanding applications.
Quality Control for Silicone Surface Finishes
Ensuring that silicone products meet stringent surface finish standards requires a robust quality control process. This process begins with thorough inspection of the silicone product’s surface for any defects, such as scratches, dust, or other imperfections that could affect appearance or performance.
Real‑World Examples & Applications
Understanding how surface finishes impact silicone products becomes clearer through real-world use cases across industries:
- Medical Devices: Silicone buttons, valves, and wearable components benefit from dry blast matte finishes to reduce glare, enhance tactile feel, and support safe skin contact. Texture also affects the effectiveness of sterilization and bonding with adhesives.
- Consumer Electronics: Devices such as earbuds, protective cases, and grips often use B-2 or A-2 SPI mold finishes to combine premium aesthetics with functionality. Gloss finishes give sleek appeal, while satin options reduce smudging. In some cases, spraying is used to apply protective or decorative coatings to silicone surfaces, enhancing durability and appearance.
- Gaskets and Seals: Dull or textured finishes from a Dry Blast standard improve the surface energy and adhesive compatibility for silicone gaskets, enabling stronger sealing under compression. These finishes also support consistent compression set performance.
- Wearables and Sports Gear: Compression-molded silicone rubber components like wristbands or handle grips typically are low-polish parts. Grit Paper or VDI matte finishes are used to increase grip, manage sweat, and provide long-term comfort during use.
Each application emphasizes a different priority—from hygiene to adhesion to brand perception—all impacted by surface finish choice.
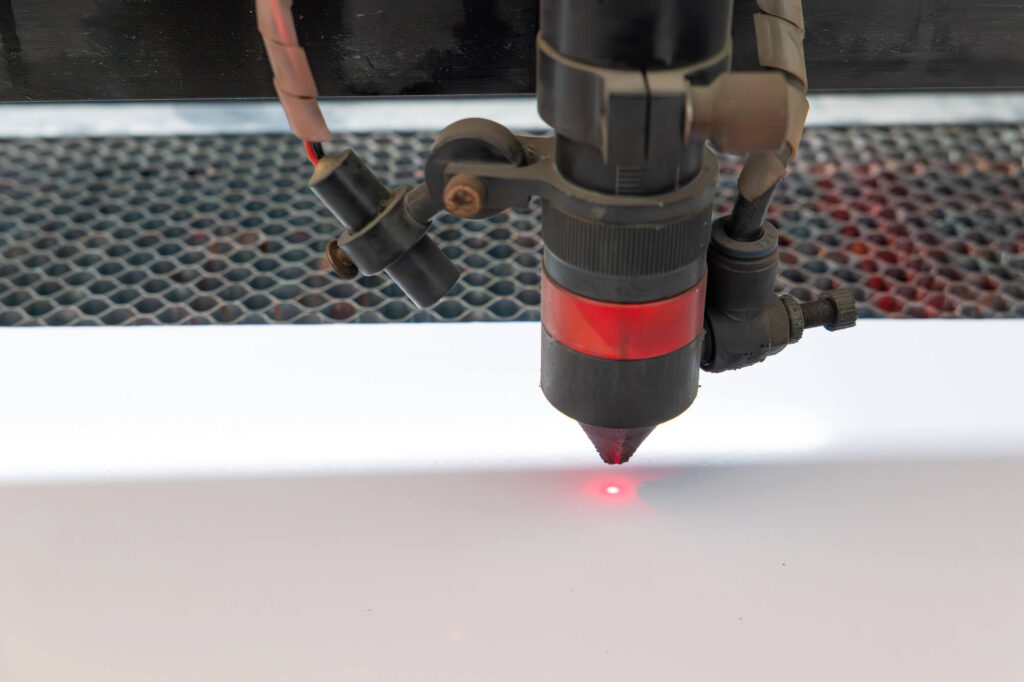
Maintenance for Consistent Surface Quality
Consistent surface quality in silicone products starts with diligent mold maintenance throughout the manufacturing process. The condition of the mold directly affects the surface finish of every final product, making regular upkeep essential for high-quality results.
Routine cleaning and inspection of molds help prevent the buildup of residue, dust, or debris that can mar the surface of silicone products. Periodic polishing and refurbishment restore the mold’s surface, ensuring it remains smooth and free from scratches or other imperfections that could transfer to the molded part. Additionally, storing molds in a clean, dry environment protects them from corrosion and damage, further preserving their ability to produce flawless finishes.
By prioritizing mold maintenance, manufacturers can reduce the risk of defects, maintain consistent surface finishes across production runs, and enhance the overall efficiency of the injection molding process. This attention to detail not only improves the quality and performance of silicone products but also extends the lifespan of valuable tooling, supporting long-term manufacturing success.
Getting Your Silicone Surface Finish Right
Selecting the right surface finish for your silicone molded product is a strategic design choice that affects function, manufacturability, user experience, and compliance. Whether the goal is enhanced grip for rubber parts, cleanability, or brand aesthetics, the finish must align with the product’s purpose, raw material properties such as silicone rubber, and the overall molding process.
With expertise across liquid and solid silicone injection molding, compression molding, plastic injection mold fabrication, and tooling strategies for SPI, VDI 3400, and custom textures, Kenvox ensures that your surface finishes are not only visually effective but also production-ready. From SPI mold classifications and SPI surface standards to advanced EDM and machining techniques, our team delivers finishes compatible with stainless steel tooling as well as specialized applications that meet strict regulatory compliance.
Have a product that requires precise surface finish control? Reach out to Kenvox today to start your next project with expert support in mold design, surface validation, and silicone manufacturing.