In today’s fast-paced and ever-evolving industrial landscape, manufacturing innovations are vital in meeting the specific needs of various sectors. As technology progresses, the demand for customized solutions continues to rise, pushing manufacturers to refine their processes and capabilities. One standout method that has emerged is custom injection molding—a highly versatile technique that empowers companies to create unique parts tailored to their particular requirements.
Custom injection molding parts are at the forefront of this manufacturing transformation. Whether it’s automotive, aerospace, medical, or consumer products, custom plastic injection molding stands out as a key player, enabling businesses to turn their innovative ideas into tangible products.
In this blog post, we will delve into the world of custom injection molding, exploring its benefits, applications, and the latest trends shaping the future of manufacturing.
What Is Plastic Injection Molding?
Plastic injection molding (IM) is a specialized manufacturing process that involves injecting molten plastic into a precisely designed mold. This method enables the production of intricate shapes and detailed parts, making it a favored choice among manufacturers looking to create high-quality plastic components quickly and efficiently and for a large range of applications.
Basic Process Overview
The plastic injection molding process consists of several key stages:
- Mold Creation: The first step involves designing and fabricating an injection mold. This mold is customized according to the specifications of the part to be produced and can be made from various materials, including steel or aluminum.
- Injection: Once the mold is ready, plastic pellets made from raw plastic materials are fed into a heated barrel where they are melted, part of the overall plastic injection molding machine. The molten plastic is then injected into the mold under high pressure, filling the cavity to form the desired shape.
- Cooling: After injection, the mold is cooled, allowing the plastic to solidify and maintain its shape. This cooling phase is critical as it affects the dimensional accuracy and surface finish of the final part.
- Ejection: Finally, the mold is opened, and the finished part is ejected. This step often includes automation for efficiency, allowing for rapid production cycles and high output rates.
Advantages of Plastic IM
The plastic injection molding process offers numerous advantages, making it a preferred manufacturing technique for many industries:
- High Production Speed and Efficiency: Injection molding is known for its rapid production capabilities. Once the mold is created, thousands of identical parts can be produced in a short amount of time, significantly increasing manufacturing throughput.
- Consistency in Part Quality and Design: One of the hallmarks of IM is its ability to produce parts with remarkable and consistent quality. Each injection cycle produces a finished product that meets strict tolerances, ensuring uniformity in quality and design across large production runs.
- Wide Variety of Material Options: With advancements in materials technology, IM can accommodate a highly diverse set of plastic resins, from thermoplastics to thermosetting plastics and alternative material options. This flexibility allows manufacturers access to broader material choices that best suit their specific requirements, whether durability, flexibility, or resistance to chemicals.
As you can see, IM stands as a cornerstone of modern manufacturing, enabling the creation of high-quality, bespoke parts that meet the unique demands of a wide range of industries industries.
What Is Custom Injection Molding?
Custom injection molding is a specialized manufacturing process designed to produce distinct parts that cater to specific industry needs and requirements. Unlike the standard injection molding process, which usually employs pre-existing molds to create large quantities of uniform parts, custom injection molding focuses on creating unique components that meet precise specifications.
The key difference lies in the adaptability and precision of the molds used in the custom process. While standard IM typically limits production to a restricted range of sizes and designs, custom IM enables designers and engineers to create specialized molds that can accommodate intricate shapes, sizes, and materials, a critical need in a wide range of industries.
This flexibility allows businesses to innovate and develop products that stand out in competitive markets and are made to fit their unique applications and operational demands.
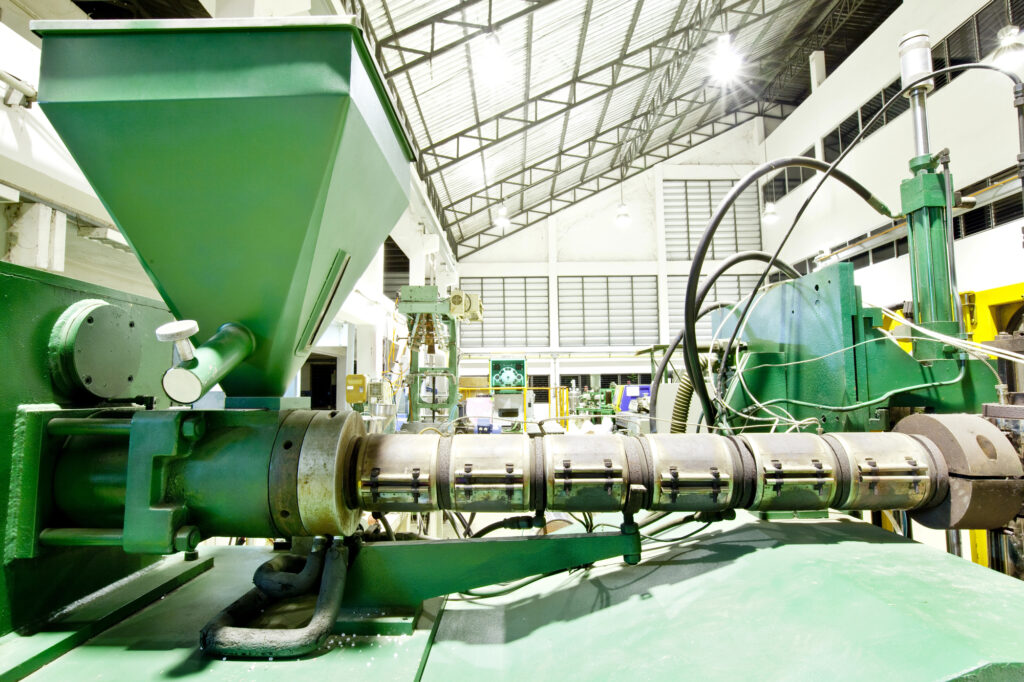
Key Benefits of Custom IM Parts
Custom IM offers a multitude of advantages that make it an attractive choice for businesses seeking tailored solutions in their manufacturing processes.
Below are some of the primary benefits that underscore its significance:
Design Flexibility
One of the standout features of custom plastic injection molding is its design flexibility. This process allows product designers and manufacturers to produce highly complex designs that would be nearly impossible to achieve using traditional manufacturing methods. Furthermore, it enables the creation of parts that meet specific performance and aesthetic requirements, facilitating innovation and customization.
Material Variety
Custom IM grants access to a wide selection of materials, including thermoplastics, thermosets, and specialty resins. This diverse material palette allows manufacturers to select substances that are best suited to their industrial applications, ensuring optimal performance characteristics such as durability, flexibility, and chemical resistance.
Precision and Consistency
Custom plastic injection molding is synonymous with precision. The process delivers reliable results that maintain strict tolerances, thereby ensuring that every part produced in a batch is consistent in quality and design. This reliability is vital for industries where exact specifications and production requirements are crucial for functionality.
Scalability
The process of custom injection molding is scalable, making it suitable for both small-batch production and large-scale manufacturing. Whether a company needs a limited run of specialized parts or plans to ramp up production for a mass market, custom injection molding can easily adapt to meet those needs.
Cost-Effectiveness
One of the compelling reasons to invest in custom injection molding is its cost-effectiveness, particularly for high-volume production. While the initial setup costs can be higher than other methods, the efficiency and speed of production ultimately reduce the cost per unit, making it a financially savvy choice for businesses looking to produce large quantities of specialized parts.
Reduced Waste
Custom injection molding employs sustainable production methods that often incorporate recyclable materials, leading to a reduction in waste. The precision of the process means less excess material is left over at the end of production, enhancing environmental responsibility while also cutting costs associated with raw material use.
Its clear benefits of custom parts extend far beyond just meeting design specifications; they encompass versatility, efficiency, and sustainability, making it a cornerstone of modern manufacturing solutions.
Industries That Most Rely on Custom Injection Molding Parts
Custom injection molding is a versatile manufacturing process that serves a wide array of industries. This adaptability is crucial for companies that require specialized components tailored to their specific needs. Below, we explore the key sectors that significantly benefit from custom IM parts.
- Healthcare and Medical: In the healthcare sector, the demand for precision and reliability is paramount. Custom IM can create a variety of products like surgical tools, prosthetics, and diagnostic equipment components that meet stringent regulatory standards. The ability to create sterile, high-quality parts ensures that medical devices function effectively and safely in critical environments.
- Automotive: The automotive industry relies heavily on custom injection molding services for the production of both interior and exterior components. This includes everything from dashboards and door panels to connectors and engine parts. The ability to design lightweight yet durable components contributes to improved fuel efficiency and overall vehicle performance, addressing both safety and consumer demand.
- Aerospace: In aerospace applications, where weight and strength are essential, custom IM can offer lightweight components designed to withstand extreme conditions. Parts produced for aviation—from cabin interiors to structural elements—benefit from technological innovations that ensure reliability while minimizing weight, thereby enhancing fuel efficiency.
- Consumer Goods: For companies in the consumer goods sector, differentiation is key. Custom injection molding allows for the creation of unique product designs that help brands stand out in competitive markets. This process not only provides aesthetic appeal but also enhances functionality in everyday products ranging from kitchenware to personal care items.
- Electronics: The electronics industry extensively utilizes custom injection molding to produce housing, connectors, and intricate internal components. The ability to manufacture precise parts that integrate seamlessly within devices is vital in a market characterized by rapid technological advancement and consumer demand for reliability and performance.
How Custom Injection Molding Works
Custom injection molding is a sophisticated process that combines engineering prowess with innovative design to create parts tailored to specific needs.
Understanding how the entire process works is essential for both manufacturers and consumers looking to leverage its benefits.
Design and Prototyping
The journey of custom injection molding begins with collaboration between designers and engineers. This partnership is crucial for conceptualizing and creating the molds that will shape the final products. Product designers employ advanced Computer-Aided Design (CAD) software to visualize and detail every aspect of the component, ensuring that all specifications are met before moving to the next phase.
Additionally, prototyping is utilized to create initial models, allowing for testing and adjustments to design, ultimately leading to a final part design that meets performance and aesthetic demands.
Material Selection
Choosing the right materials is a critical step in the custom injection molding process, as it directly impacts the performance and durability of the final product. Materials are selected based on the specific requirements of the application, considering factors such as temperature resistance, strength, and flexibility. The process often involves a thoughtful analysis of material types, including thermoplastics for lightweight and versatile applications, thermosets for heat resistance and durability, and specialty resins designed for unique conditions and functionalities.
Production Process
Once the design and material have been finalized, the production process begins. This stage involves precision molding techniques capable of creating complex shapes and features that are often unattainable through other manufacturing methods. The injection molding machines inject molten plastic into the mold under high pressure, allowing for detailed and high-quality parts. To ensure consistency and reliability, rigorous quality control measures are implemented throughout production. This attention to detail helps manufacturers deliver parts that meet or exceed the specified standards, assuring customers of their reliability and performance in various applications.
Specialized Techniques
Custom injection molding offers vast possibilities not only in terms of part function but also regarding aesthetics. The ability to create specialized finishes, textures, and designs can significantly enhance a product’s appeal and usability. This section explores various options available for customizing injection-molded products.
- Surface Finishes: Surface finishes are crucial for the aesthetic and functional qualities of injection-molded parts. Manufacturers can choose from matte, gloss, textured, or polished options, each serving its specific purpose. For instance, a glossy finish may attract attention from consumer electronics, whereas a matte finish is suitable for products needing to minimize glare.
- Texture Customization: Texture customization significantly influences grip and visual design. By incorporating patterns, manufacturers can improve user experience through enhanced friction or comfort during handling. Textured surfaces not only ensure better grip but can also elevate a product’s overall aesthetic quality.
- Advanced Techniques: Advanced molding techniques like overmolding, insert molding, and multi-shot molding enhance the complexity and functionality of custom plastic parts. Overmolding combines two materials for varied attributes, while insert molding integrates components like metal inserts for added strength. Multi-shot molding allows for the production of multi-colored or multi-material parts in one cycle.
- Unique Design Elements: Custom injection molding supports unique design elements that let brands differentiate themselves in a competitive market. This includes integrating branding or logos into the molded parts, reinforcing brand identity while streamlining production, and reducing costs. Such creativity in design opens new avenues for enhancing product offerings and appealing to consumer demands for authenticity and style.
Thermoset and Thermoplastics: The Main Materials Used in Injection Molding
Injection molding primarily utilizes two types of materials: thermosets and thermoplastics.
Each type has distinct material properties and characteristics that make them suitable for various applications.
Thermoset Materials
Thermoset materials are characterized by their ability to undergo a chemical change when subjected to heat, resulting in a hardened structure that cannot be re-melted. This unique mechanical property offers several advantages for specific applications.
- Epoxy Resins: Known for their high mechanical strength and excellent heat resistance, epoxy resins are commonly used in applications requiring durability and stability under temperature fluctuations.
- Phenolic Resins: Recognized for their outstanding electrical properties, common applications of phenolic resins are in electrical housings and components, ensuring safety and reliability.
- Melamine Formaldehyde: This thermoset possesses scratch-resistant and heat-stable qualities, making it suitable for injection molding projects that require a durable finish, such as kitchen countertops and laminates.
- Applications: Thermoset materials find extensive applications in industries such as automotive (for components exposed to high temperatures), electrical (for housings and insulations), and environments requiring heat resistance.
Thermoplastics
Thermoplastics are a class of materials that can be melted and reformed multiple times without altering their chemical structure. This versatility allows for a wide range of applications and efficiencies in production, making thermoplastics the most commonly used material in injection molding today.
Their ease of processing, recyclability, and ability to adopt various color and finish options contribute to their popularity among manufacturers.
Common Thermosplastics Used for Custom Injection Molding Parts
Below are some of the most commonly used thermoplastics in injection molding and a quick overview of their mechanical properties:
- Nylon (Polyamide): Known for high tensile strength, abrasion resistance, and flexibility, it is ideal for automotive and industrial components where durability and performance are crucial. Its lightweight nature and resistance to harsh conditions enhance its applicability in demanding environments.
- ABS (Acrylonitrile Butadiene Styrene): A favorite among manufacturers for its reliable mechanical properties, particularly durability and impact resistance. This thermoplastic is easy to mold, suitable for a wide range of consumer goods and electronic housings, and offers a favorable balance of strength, weight, and cost-effectiveness.
- Polycarbonate (PC): Recognized for its transparency, strength, and heat resistance. Ideal for safety equipment such as helmets and goggles, as well as optical components like lenses. Its ability to withstand significant impacts while maintaining clarity makes it essential for protective applications.
- POM (Polyoxymethylene): Offers excellent stiffness and low friction and is widely used in precision mechanical parts like gears and bearings. Its dimensional stability under load ensures consistent performance in applications requiring high accuracy, making it a preferred material for various industrial components.
- Acrylic (PMMA): Valued for its transparency and weather-resistant properties. Commonly used in light fixtures, displays, and signage where clarity and durability are essential. Additionally, acrylic can be easily fabricated into various shapes, enhancing its versatility in design and construction.
- Polypropylene (PP): Lightweight, flexible, and resistant to chemicals, making it ideal for applications such as packaging, automotive parts, and medical devices. Its recycling potential and low environmental impact further enhance its appeal in industries focused on sustainable innovation.
- PBT (Polybutylene Terephthalate): PBT is a robust thermoplastic known for its excellent dimensional stability, high resistance to heat, and chemical resilience. It is widely used in electrical connectors, automotive parts, and more. Its strength and durability make it an ideal choice for applications that require both mechanical integrity and reliability under stress.
A Quick Guide to Choosing the Ideal Material for Your Custom IM Project
When choosing the best plastic material for an injection molding project, consider the following factors:
- Tensile Strength: The resistance of a material to being pulled apart; critical for applications where weight-bearing is essential.
- Durability: The ability of the material to withstand wear, pressure, or damage over time; important for longevity in functional applications.
- Cycle Time: The time it takes to complete one cycle of the injection molding process influences production efficiency and cost. Other factors that impact cycle times besides the material are mold design and part complexity.
- Melting Point: The temperature at which a material transitions from solid to liquid affects processing conditions and thermal stability during molding.
- Temperature Resistance: The material’s ability to maintain performance under extreme heat or cold; crucial for applications in high-temperature environments.
- Mechanical Strength: Overall resistance to deformation or failure under applied forces; vital for structural components.
- Chemical Resistance: The ability of the material to withstand exposure to various chemicals; important for applications in harsh environments.
- Dimensional Stability: The ability of a material to maintain its dimensions under varying temperature and humidity; critical for precision parts.
- Impact Resistance: The material’s ability to absorb energy from impacts without breaking; significant for safety-related applications.
- Surface Finish: The aesthetics and texture of the part may be important for consumer-facing products.
- Moisture Resistance: The material’s ability to resist absorption of moisture; important for applications in wet or humid environments.
- Cost: The expense associated with the material and processing influences budget and project feasibility.
- Ease of Processing: How easily the material can be molded affects production techniques and equipment requirements.
- Additives Compatibility: The potential for incorporating additives to enhance properties (e.g., colorants, UV stabilizers) influences performance and aesthetics.
- Environmental Impact: Considerations around recyclability and sustainability of the material are increasingly relevant in product design and consumer preference.
In summary, the selection of thermoplastics in injection molding provides manufacturers with the flexibility and performance needed to meet diverse consumer demands while ensuring quality and efficiency in production.
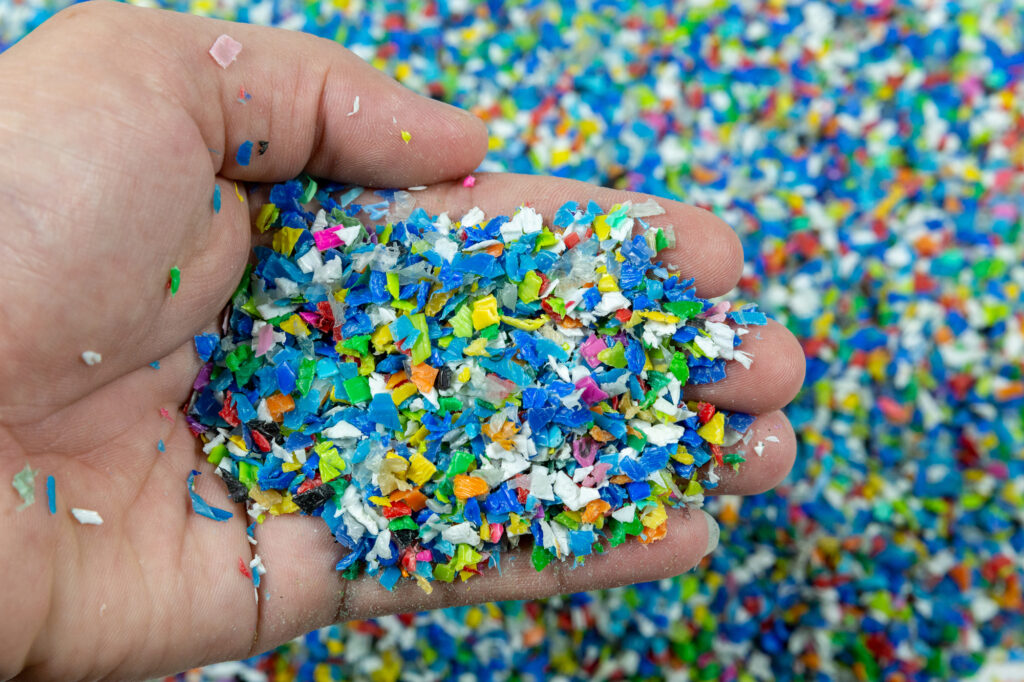
How to Choose the Right Custom Injection Molding Partner
Selecting the right partner for custom injection molding is crucial for achieving high-quality parts that meet your specific needs. Here are key factors to consider when evaluating potential providers:
Experience and Expertise
When it comes to injection molding, experience matters; look for manufacturers that have a proven track record in the industry. An established provider typically has dealt with a variety of projects and challenges, equipping them with the knowledge to navigate complex requirements and deliver superior results.
Material Knowledge
The variety of materials available for injection molding can greatly influence the final product. Ensure that the provider you choose has extensive knowledge and access to a range of thermoplastics and other suitable materials. This capability not only allows for tailored solutions but also ensures that the selected material aligns with the performance needs and environmental considerations of your project.
Technology and Equipment
The efficiency and quality of the molding process heavily depend on the technology and equipment used. Check whether the manufacturer is equipped with modern machinery that offers advanced capabilities, such as precise temperature control and automation. State-of-the-art equipment can significantly enhance production accuracy, reduce cycle times, and ultimately lower costs.
Quality Assurance
Quality should never be compromised in manufacturing. It’s essential to partner with a provider that prioritizes quality assurance processes. Look for certifications that demonstrate adherence to industry standards, as well as robust testing protocols, to ensure that every part meets your specifications. A commitment to quality not only fosters reliability but also builds a strong long-term partnership.
By considering these factors, you can select a custom injection molding partner that aligns with your goals, ensuring a successful project from start to finish.
Future Trends in Custom Injection Molding
As the manufacturing landscape continues to evolve, custom injection molding is also transforming to meet emerging demands and innovations. This section explores the key trends that are shaping the future of this industry.
Advanced Materials
The integration of advanced materials is revolutionizing custom injection molding. Bioplastics and composites are gaining popularity due to their environmental benefits and enhanced performance characteristics. These materials not only reduce reliance on fossil fuels but also offer lightweight solutions that can meet the rigorous demands of various applications, from automotive to consumer goods. As research continues, the development of new formulations will further expand material options and capabilities.
3D Printing and Hybrid Production Techniques
The combination of 3D printing with traditional injection molding processes is paving the way for innovative production methods. By using 3D-printed molds for injection molding, manufacturers can achieve lower production costs and shorter lead times for low-volume production. This hybrid approach allows for rapid prototyping and flexibility in design, enabling companies to adjust quickly to market demands without large financial investments in tooling.
Automation and AI
Automation and artificial intelligence (AI) are poised to redefine injection molding production. The use of AI and machine learning algorithms can optimize production processes by predicting maintenance needs, improving cycle times, and minimizing waste. Automated systems can enhance precision and consistency while allowing for real-time adjustments throughout the production cycle. These technologies not only boost efficiency but also improve the overall quality of the end product.
Sustainability
Sustainability is becoming a central focus in manufacturing, and custom injection molding is no exception. Eco-friendly practices, such as utilizing recycled materials and reducing energy consumption, are increasingly being integrated into production processes. Manufacturers are exploring ways to minimize their environmental footprint while maintaining high-quality standards. The shift towards sustainable practices is not only beneficial for the planet but also appeals to a growing market of environmentally conscious consumers.
Embracing these trends will be essential for manufacturers aiming to stay competitive in an ever-evolving marketplace.
Kenvox Is Here for Any Custom Injection Molding Project
Custom injection molding offers businesses the ability to design components that fully align with their unique operational needs, enabling improved performance and competitive advantage.
By leveraging tailored solutions in custom injection molding, companies can optimize their production processes, reduce material waste, and significantly shorten time-to-market.
If you’re considering how custom injection molding can elevate your next project, look no further. Partnering with a trusted provider like Kenvox can make all the difference. With our expertise and commitment to quality, we are equipped to turn your design visions into reality. Contact us today to discuss how we can support your custom injection molding needs and help you achieve your manufacturing goals!